-
- News
- Books
Featured Books
- design007 Magazine
Latest Issues
Current IssueProper Floor Planning
Floor planning decisions can make or break performance, manufacturability, and timelines. This month’s contributors weigh in with their best practices for proper floor planning and specific strategies to get it right.
Showing Some Constraint
A strong design constraint strategy carefully balances a wide range of electrical and manufacturing trade-offs. This month, we explore the key requirements, common challenges, and best practices behind building an effective constraint strategy.
All About That Route
Most designers favor manual routing, but today's interactive autorouters may be changing designers' minds by allowing users more direct control. In this issue, our expert contributors discuss a variety of manual and autorouting strategies.
- Articles
- Columns
- Links
- Media kit
||| MENU - design007 Magazine
Estimated reading time: 4 minutes
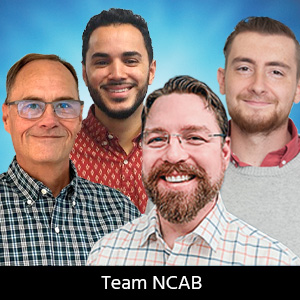
Fresh PCB Concepts: Why Material Selection Matters
Like most engineers, I started by designing hobby electronics. I learned about different components, connected them up on a breadboard, and created a PCB to show off what I had built to my friends. Whenever I had a problem, I would trace it back to the component datasheet or some code I had written. I didn’t realize the importance of the PCB until I ran into a problem that couldn’t be fixed with the code or components alone.
When you’re designing a PCB, it’s standard to call out FR-4 material, but you could be holding yourself back or even exposing your board to risk by not knowing more about PCB materials. Let’s take a small look into why.
What Is FR-4?
FR-4 material is made out of fiberglass weave impregnated with resin (Figure 1). It’s a fairly common reinforcement material that has good adhesion with the copper layers and plating. FR-4 is great to use for common electronics since it’s cheap and easy to work with.
Figure 1: FR-4 fiberglass weave pattern. (Source: NCAB Group Corporation)
When Material Selection Could Be Holding You Back
Application is key when designing a board. It allows you to define how reliable the design needs to be or how long the design must last. Material selection can help or hurt your design when designing for a specific application. Two cases where material selection can be a problem for a design are for high-speed and high-temperature applications.
If your product requires digital data, speed is important. Sending data reliably at higher speeds requires you to use a material that will not cause unintentional impedance or allow noise to affect the signal. The weave pattern of the FR-4 material results in copper layers that aren’t on a uniform surface. The ratio of fiberglass to epoxy along with the alignment of the copper traces to the weave pattern will cause signal integrity issues at higher speeds.
Understanding the application for a design also includes the temperature the design will be exposed to over its lifetime. For example, if your automotive application sees an average temperature of 180°C, you need to make sure the PCB material is rated for higher temperatures. Failure to do so can cause the device to work in a controlled environment but fail when tested in the field (Figure 2).
Figure 2: A cross-section of a six-layer PCB. (Source: HuMANDATA LTD.)
What to Know
When you first look at a material datasheet, there are a lot of specifications listed that can become overwhelming. If you don’t know where to start, focus on these four specifications:
- Glass transition temperature (Tg): The temperature region where the FR-4 material changes from a hard glass to a softened material. The substrate will harden back to its normal state when the heat is removed.
- Decomposition temperature (Td): The temperature region where the PCB substrate will decompose. The effect of the decomposition is irreversible.
- Coefficient of thermal expansion (CTE): The amount the substrate will increase in size. In this case, I will look at expansion in the Z-axis as temperature rises.
- Dielectric constant (Dk): A ratio that corresponds to how much loss a signal will experience as frequency increases.
If nothing else, a designer should understand these four specifications and look at them when comparing materials to use for a design.
Underconstraining
Knowing the application of your design, you must communicate key parameters to the factory. This will ensure that a design is using an FR-4 material with the correct Tg or has the correct Dk for the high-speed data transmission. This becomes even more important as you transition from a prototype design into production quantities.
For example, let’s look again at CTE values. Figure 3 shows a cross-section of a plated via that our team investigated. Notice that the copper of the top and second layer aren’t horizontal but skewed up; this is due to the FR-4 material expanding at a different rate compared to the copper plating. We’ve often seen Z-axis expansion leading to cracking at the knee of the via or even deeper in the barrel causing an open connection.
Figure 3: A cross-section of a PCB via after a thermal expansion; the black is the FR-4 material. (Source: NCAB Group Corporation)
Think about all of the vias on your next design. Consider what would happen if your board overheated. What could that field failure cost? A simple material change could avoid all of it.
Overconstraining
Overconstraining is also a concern when it comes to material selection. It might help at first to select a specific material when you first design a product, but things change. The factory you build with could change, the material could not be in stock, or the material might become outdated or expensive. I’ve seen customers who continue to call out a specific material only because the previous engineer used the material. This can become expensive and add lead time for a factory to purchase uncommon materials when there is possibly an equivalent in stock.
To help with this, IPC has created a classification for different types of materials. In IPC-4101, “Specification for Base Materials for Rigid and Multilayer Printed Boards,” and IPC-4103, “Specification for Base Materials for High-Speed/High-Frequency Applications.” The specifications organize the different material choices by characteristics—such as Tg, Td, Dk, CTE, resin system—or many of the other parameters of a laminate. When factories provide an alternative to a material you specified, you can use IPC as an agreed standard for finding an equivalent.
Conclusion
Overall, your material selection should match your design application. When you run into issues with a product, don’t just look at the components that go on top of the board; look at the materials that go inside of the board.
Harry Kennedy is a field application engineer at NCAB Group.
More Columns from Fresh PCB Concepts
Fresh PCB Concepts: Designing for Success at the Rigid-flex Transition AreaFresh PCB Concepts: More Than Compliance—A Human-centered Sustainability Approach
Fresh PCB Concepts: Assembly Challenges with Micro Components and Standard Solder Mask Practices
Fresh PCB Concepts: The Power of a Lunch & Learn for PCB Professionals
Fresh PCB Concepts: Key Considerations for Reliability, Performance, and Compliance in PCBs
Fresh PCB Concepts: Traceability in PCB Design
Fresh PCB Concepts: Tariffs and the Importance of a Diverse Supply Chain
Fresh PCB Concepts: PCB Stackup Strategies—Minimizing Crosstalk and EMI for Signal Integrity