-
- News
- Books
Featured Books
- pcb007 Magazine
Latest Issues
Current IssueInventing the Future with SEL
Two years after launching its state-of-the-art PCB facility, SEL shares lessons in vision, execution, and innovation, plus insights from industry icons and technology leaders shaping the future of PCB fabrication.
Sales: From Pitch to PO
From the first cold call to finally receiving that first purchase order, the July PCB007 Magazine breaks down some critical parts of the sales stack. To up your sales game, read on!
The Hole Truth: Via Integrity in an HDI World
From the drilled hole to registration across multiple sequential lamination cycles, to the quality of your copper plating, via reliability in an HDI world is becoming an ever-greater challenge. This month we look at “The Hole Truth,” from creating the “perfect” via to how you can assure via quality and reliability, the first time, every time.
- Articles
- Columns
- Links
- Media kit
||| MENU - pcb007 Magazine
Estimated reading time: 2 minutes
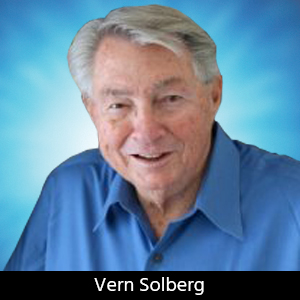
Designers Notebook: Focus of Interest at SMTAI 2019—Low-temperature Solder
Both suppliers and users of solder materials participated in discussions at SMTAI 2019 related to low-temperature solder (LTS). The solder supply companies present had a wide range of material compositions that employed elements of bismuth or indium to reduce the liquidus temperature of the alloy during the joining process. Key issues that user companies are concerned with are the lower-temperature alloys selected must be reliable and exhibit shear strength, creep resistance, and resistance to thermal fatigue for the duration of the product’s life cycle.
Indium-based alloys are said to have very good thermal conductivity and ductility when compared to other low-temperature alloys. Bismuth-based alloys are also good for low-temperature soldering; however, thermal conductivity and ductility may not meet the expectation. Tin-bismuth and tin-bismuth-silver are the most common choices for low-melting solder pastes used for surface-mount assembly. The peak reflow temperatures provided by tin-bismuth alloys are low (160–170°C) compared to tin-silver-copper solders (220–230°C). The lower peak temperatures required for joining the LTS alloys are preferred when soldering thermally sensitive assemblies.
LTS has been a subject of research at Hewlett-Packard’s Electronic Assembly Development Center (EADC). The company believes that several benefits may derive from adopting this technology. They trust that a significant decrease in the peak reflow temperature during the reflow solder process will reduce physical stress to both the components and PCBs. HP further acknowledged that a single LTS alloy is not likely to be a universal solution for all product applications or suitable at all for products exposed to harsher operating environments and that extensive qualification testing of these materials is paramount.
Alloy selection is only the first step in developing a low-temperature soldering process. A suitable flux must be chosen for use in a solder paste, and the alloy-flux interaction must be evaluated. The ability of fluxes to activate at temperatures 20–30°C below the melting point of the alloy must be evaluated. In the case where different solder metallurgies have similar mechanical properties, the optimal metallurgy for a low-temperature process may be determined by the availability of the appropriate flux chemistry.
For the flux selection phase, there is no standard procedure for testing the activity of a solder flux. The degree of wetting in a system (solder, substrate, atmosphere, flux) may be characterized with a sessile spread test or by a wetting force measurement. The two tests are complementary. Each of the tests is said to involve a balancing of surface tensions at a three-phase junction. For an assessment of flux activity, a dynamic measurement is more appropriate than a static measurement. Thus, the wetting force measurement is preferred to the sessile spread measurement.
Intel is committed to implementing LTS for a broad number of products as well. The company noted that repeated exposure of array-configured components to the high peak temperature experienced during the tin-silver-copper (SAC) alloy solder reflow process often impacts the integrity of the terminal interface. It is not uncommon to experience package warp, causing momentary separation of the terminal from the circuit board’s land pattern. When the warp condition subsides, the solder interface is often compromised.
Intel has also performed extensive testing and evaluation of the LTS product offerings and anticipates implementation for a broad range of products. In addition to production cost savings from reduced energy consumption and environmental benefits, the company anticipates faster technology scaling for a wide range of applications.
Vern Solberg is an independent technical consultant based in Saratoga, California, specializing in SMT and microelectronics design and manufacturing technology.
More Columns from Designer's Notebook
Designers Notebook: Basic PCB Planning Criteria—Establishing Design ConstraintsDesigners Notebook: Layer Stackup Planning for RF Circuit Boards
Designers Notebook: Addressing Future Challenges for Designers
Designers Notebook: Impact of Advanced Semiconductor Packaging on PCB Stackup
Designers Notebook: Implementing HDI and UHDI Circuit Board Technology
Designer's Notebook: Heterogeneous Integration and High-density SiP Technologies
Designers Notebook: PCB Design and IPC-CFX for Assembly Automation
Designer’s Notebook: What Designers Need to Know About Manufacturing, Part 2