-
- News
- Books
Featured Books
- smt007 Magazine
Latest Issues
Current IssueSupply Chain Strategies
A successful brand is built on strong customer relationships—anchored by a well-orchestrated supply chain at its core. This month, we look at how managing your supply chain directly influences customer perception.
What's Your Sweet Spot?
Are you in a niche that’s growing or shrinking? Is it time to reassess and refocus? We spotlight companies thriving by redefining or reinforcing their niche. What are their insights?
Moving Forward With Confidence
In this issue, we focus on sales and quoting, workforce training, new IPC leadership in the U.S. and Canada, the effects of tariffs, CFX standards, and much more—all designed to provide perspective as you move through the cloud bank of today's shifting economic market.
- Articles
- Columns
- Links
- Media kit
||| MENU - smt007 Magazine
Estimated reading time: 3 minutes
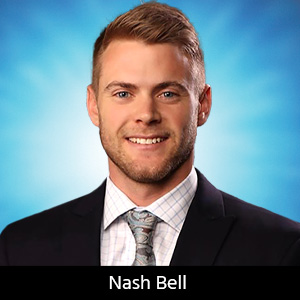
Knocking Down the Bone Pile: Process Methods for Reworking High Lead Count SMT Parts
There are numerous methods for getting the solder onto the right pads in the right volume during SMT rework of high pin count or very small footprint SMT devices. The most common types of solder deposition include printing, dispensing, and hand soldering. Each of these methods has pros and cons, depending on a variety of factors in the rework process.
Hand Soldering Rework
Hand soldering of high lead count or very small package SMT components for rework is fast and requires a high degree of skill from the operator. The good news about using the hand soldering process for these types of SMT components is that a device during debug can be quickly reworked and passed back to test or design engineering.
Figure 1: Hand soldering for rework of fine-pitched components.
However, there are some deficiencies in using a hand soldering rework process for electronic components. First, the lack of consistent solder volumes and consistent hand soldering uniformity makes this an uncontrolled process. When the process allows for adding flux, the lack of control over this flux volume means that flux residue and board cleanliness can be a potential reliability risk. For some of the fine-pitched parts in high-density areas, a high degree of rework technician skill is required, which limits the throughput (Figure 1) In addition, nearby components can become damaged if the technician is not careful when placing the soldering iron. Also, hand soldering is not a cost-effective option in some cases, as it can be very time-consuming.
Stencil Printing
Stencil printing for the rework of high pin count or very small package SMT components for PCB rework has some pluses and minuses. The advantages to using stencil printing for the rework of these devices are numerous and include this being a well-known technique with well-known materials, requiring a moderate degree of skill from the rework technician. The speed of the rework method is also fast compared to the other methods.
Figure 2: Flexible stencil paste print.
The flexible, single-use stencils (Figure 2), while still being space-constrained, allow the rework technician to get into tight spaces. These adhesive-backed stencils have overcome the limitations of the metal stencils, including board coplanarity, the bending of the stencils during handling, getting into tight spaces, the necessity to tape around the device to prevent solder paste from contaminating the area, and the necessity for a holding fixture for alignment and time it takes to clean the stencils.
But this rework method has drawbacks, including the handling of stencils when very small packages are involved, the “messiness” related to solder paste printing, and the time it takes to have the stencils on hand (24–48 hours) all limit the usefulness of stencil printing solder paste for rework.
Dispensing
Dispensing, along with jet printing, offers an alternative to both stencil printing as well as hand soldering. There are several advantages for dispensing when it comes to the rework of high I/O count and/or very small package components (Figure 3). The biggest differentiator of this technology is the precision of the dispensing technique. Modern Archimedes screw-type dispensers can dispense 20,000 dots per hour down to 800-um sizes. A single jet printing setup can print at a constant speed of up to 300 Hz, or 1,000,000 dots per hour, with the dots getting down to 200-μm in size.
Figure 3: Dispensed solder paste on ultra-fine-pitch SMT component.
One of the other big advantages of jetting is that multilevel boards and odd-shaped lands—such as RF shields with the same deposited solder volume—offer high repeatability. In addition, this method is more automated than the stencil or hand solder rework methods. While this method offers many advantages, it is not for every scenario due to its capital-intensive nature, the programming required, and the relatively slow speed of deposition. Dispensers that can be used for solder paste deposition start at several thousand dollars and range up to over $100,000 U.S. dollars. And each of the package footprints take time and skill level to program.
This method, even when finely tuned, is very slow compared to the methods. Finally, any process that involves a liquid and dispensing like this requires expertise so that lines, nozzles, and other elements of the dispensing system are kept clean and optimized. This is rheological “tightrope to walk” with dispensing technology and the associated precision deposition upside.
Conclusion
The process engineer has to take each rework situation and consider the turn time required, the reliability of the assembly in the end-use operating environment, the skill level of the operators, the available funds, and the economics to make the right decision.
Bob Wettermann is the principal of BEST Inc., a contract rework and repair facility in Chicago.
This article was originally published in the September 2019 issue of SMT007 Magazine.
More Columns from Knocking Down the Bone Pile
Knocking Down the Bone Pile: Addressing End-of-life Component Solderability Issues, Part 4Knocking Down the Bone Pile: Tin Whisker Mitigation in Aerospace Applications, Part 3
Knocking Down the Bone Pile: Gold Mitigation for Class 2 Electronics
Knocking Down the Bone Pile: Basics of Component Lead Tinning
Knocking Down the Bone Pile: Package on Package Rework—Skill Required
Knocking Down the Bone Pile: 2023’s Top Challenges in BGA Rework
Knocking Down the Bone Pile: Eliminating Solder Balls in Hand Soldering
Knocking Down the Bone Pile: Opening a Trace on the Surface of a PCB