-
- News
- Books
Featured Books
- smt007 Magazine
Latest Issues
Current IssueSupply Chain Strategies
A successful brand is built on strong customer relationships—anchored by a well-orchestrated supply chain at its core. This month, we look at how managing your supply chain directly influences customer perception.
What's Your Sweet Spot?
Are you in a niche that’s growing or shrinking? Is it time to reassess and refocus? We spotlight companies thriving by redefining or reinforcing their niche. What are their insights?
Moving Forward With Confidence
In this issue, we focus on sales and quoting, workforce training, new IPC leadership in the U.S. and Canada, the effects of tariffs, CFX standards, and much more—all designed to provide perspective as you move through the cloud bank of today's shifting economic market.
- Articles
- Columns
- Links
- Media kit
||| MENU - smt007 Magazine
Estimated reading time: 5 minutes
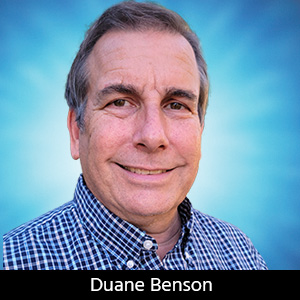
Powerful Prototypes: Panelization—What Is It and Why Would You Want It?
If I came up with an “average” or “typical” prototype PCB order, I would probably say that it consists of 20 boards that are 4” x 5” in size. Each board would have 25 different types of components with 125 placements in total. However, it’s difficult to define either “average” or “typical” in the prototype world, hence the quotes.
We see orders for a single board, and we see orders for thousands. “A few thousand” falls way outside the realm of “prototype,” but in the startup and open-source worlds, the lines are blurred. Once you order more than about 50 boards, a few things change; for example, you should consider ordering your boards in a panel, also called arrays or a palette, of multiple boards.
All PCBs start in sheets of a raw fiberglass-like material with a layer of copper, at about 30 x 30 inches square. Multiple sheets of the material are etched and pressed together to form a full panel. The finished panel will have as many copies of your board as can fit into that space. That’s a bit of an oversimplification, but essentially, that’s the standard way of building a large number of boards and has been for decades. Often, that large panel will be cut into quarters to better fit assembly machines before being delivered.
The panel is great if you need a lot of copies of a board, but if you need two boards that are 4” x 5”, you’re going to pay for a lot of wasted material, at least you did back in the old days (Figure 1). In a standard panel, each copy of the board will be exactly the same. There are some cases, though, where the boards will be different. Some designs require a set of several different circuit boards. In what’s called a “family panel,” all of the different boards are combined into one panel. Then, you may see a panel with multiple sets of four or five different boards.
Figure 1: Full panel.
About 20 years ago, our raw board fabrication partner company in this business, Sunstone Circuits (called PCBExpress, at the time) took the family panel a step further. They started combining small quantities of different board designs from different customers, which allowed them to fill up an entire panel and split the fixed costs amongst a lot of different jobs.
Before shipping, each board would be cut out with a router. Today, that is called the “individually routed” option. It delivers a nice smooth edge with none of the little nibs protruding that you see on may boards that came out of a panel. It’s a very cost-effective way to purchase a small number of blank PCBs.
When you order PCBs, you’re typically given four panel options: individually routed, as I just described, V-score, tab routed, and tab routed with perforations, or “perfs.” Individually routed boards sound nice, and they are, so why would you want to buy boards in a panel?
Some professional assembly shops can only assemble boards in panels. Panels come with a thin strip of board material around the outside of the array of circuit boards. This allows the boards to go through automated assembly equipment. Many shops these days, like mine, can take boards either individually or in panels, so this isn’t a hard and fast requirement as it was a decade or so ago. But when boards are panelized, the surface-mount machines can run a lot more efficiently.
If you’re hand assembling your boards, or only having a few professionally built, you probably don’t want a panel. Panels aren’t typically required anymore for small quantities, but if your boards are super small, or you need more than about 50 built, a panel is a really good idea. Once you get into the hundreds, panelization is really the only practical option.
V-score Panelization
V-score panelization is pretty handy for boards that are pure rectangles. With V-scoring, a saw blade, with the edge shaped like a “V,” is run across the panel, top and bottom, to cut most of the way, but not all the way, through the boards. The panel still has mechanical stability, but can be easily separated after the parts are put on (Figures 2 and 3). Note that it's all straight lines. V-score can only separate rectangular panelized boards. For curves, you'll need to use a different technique.
Tab Routing
The other common panelization method is called tab-routing, as in routed, but with tabs (that's "routed" like using a router, not as in Napoleon being chased out of Russia.) Figure 4 shows a tab-routed panel; I've obscured the detail of the PCB to protect the innocent.
Figure 4: Panel rails.
You can get tabs without the perfs, but if you're separating the individual boards yourself, you'll most likely be glad to have the perfs there. If we (most assembly houses, but not all) deem that snapping will cause undue stress on the board, we’ll use a special tool to avoid putting that stress on the boards. If you're separating them manually, the perfs can make a big difference. Figure 5 shows the actual tabs, including a close-up of a tab, both with and without perfs.
Figure 5: Panel tab without (L) and with (R) perfs.
A big advantage of tab routing is the ability to make boards in shapes other than rectangles. However, it takes a bit more PCB material and can put a lot of stress on the area near the tab. That being the case, we recommend that you not put components too close to the tabs. Now, the definition of "too close" is interesting. IPC–Association Connecting Electronics Industries–seems to have a specific standard covering the subject; 100 mils, or thereabouts, is a reasonable target because larger or stiffer parts might require a little more space.
Conclusion
To summarize, if you just need a few boards (less than 50), you may be fine to have them individually routed. Check with your assembly house first to makes sure that they can handle individual boards because not all can. If you have a lot of boards, or if they are very small, you probably want them to be in a panel. If they’re rectangular boards and don’t have any overhanging parts, you can use V-score panelization. Odd shapes or overhanging parts will require tab routing. Perfs will help greatly if you’re separating them yourself without special tools. If you have overhanging parts, let your board fabrication house know where the overhang is so that they don’t put a tab in that spot. And, finally, if in doubt, call your assembly or fabrication house and ask for advice.
Duane Benson is marketing manager and CTO at Screaming Circuits.
More Columns from Powerful Prototypes
Powerful Prototypes: Small Computer ModulesPowerful Prototypes: A Trip Back to the Basics
Powerful Prototypes: The Work World in 2021
Powerful Prototypes: Why Datasheets Matter
Powerful Prototypes: Manufacturing in an Uncertain World
Powerful Prototypes: An Open-Source Adventure
Powerful Prototypes: Five Technological Shifts in the New Decade
Powerful Prototypes: Cost Reduction in Design