-
- News
- Books
Featured Books
- pcb007 Magazine
Latest Issues
Current IssueVoices of the Industry
We take the pulse of the PCB industry by sharing insights from leading fabricators and suppliers in this month's issue. We've gathered their thoughts on the new U.S. administration, spending, the war in Ukraine, and their most pressing needs. It’s an eye-opening and enlightening look behind the curtain.
The Essential Guide to Surface Finishes
We go back to basics this month with a recount of a little history, and look forward to addressing the many challenges that high density, high frequency, adhesion, SI, and corrosion concerns for harsh environments bring to the fore. We compare and contrast surface finishes by type and application, take a hard look at the many iterations of gold plating, and address palladium as a surface finish.
It's Show Time!
In this month’s issue of PCB007 Magazine we reimagine the possibilities featuring stories all about IPC APEX EXPO 2025—covering what to look forward to, and what you don’t want to miss.
- Articles
- Columns
Search Console
- Links
- Media kit
||| MENU - pcb007 Magazine
Insulectro Leverages One Source Distribution for Printed Electronic Materials at IDTechEx
November 18, 2019 | InsulectroEstimated reading time: 2 minutes
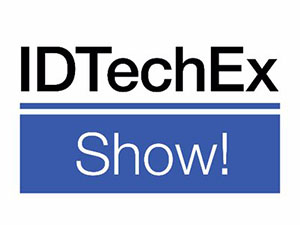
Insulectro, the largest distributor of PCB and printed electronics materials, will exhibit in booth V37 at IDTECHEX’s Printed Electronics World 2019 conference held this week, November 20-22, in Santa Clara, CA at the Convention Center.
Insulectro Printed Electronics offers advanced materials from such leading suppliers such as DuPont, Coveme, FLEXcon, Saint-Gobain, Chromaline, 3M and Kodak to sell conductive inks, substrates, and consumables.
Insulectro distributes key DuPont polymer thick film paste products to U.S. customers in the thin film photovoltaic, wearables, capacitive switch, touch screen, RFID smart card, heating and membrane touch switch markets. In addition, Insulectro Printed Electronics distributes carbon conductors, UV dielectrics, fired-on inks and in-mold systems on behalf of DuPont.
Kevin Miller, vice president of sales for Insulectro Printed Electronics, commented, “We are excited to showcase our products at Printed Electronics World. We are a one-source supplier for PE manufacturers with our complete offerings of essential and cutting edge materials. With 11 stocking locations throughout North America, we are where our customers are. We developed a strong sales and service model on Insulectro’s PCB-side of our business over a long period of years. That wealth of knowledge transfers readily to printed electronics. Now, Insulectro’s Printed Electronics Division is making a difference in that industry.”
Recently, Insulectro was named distributor for DuPont’s innovative In-Mold electronic inks.
Miller continued, “In-Mold conductive inks are a perfect union of form and function. The technology combines an innovative, more stretchable material with dramatic advancements in electronic ink to give interface designers new creative freedom, without any compromise in meeting functional switching needs. And because these new electronic inks work with existing in-mold decorative processes, there’s no need for costly re-tooling. Fabricators can create products with greater eye appeal, simplicity, and performance—all at the same time.”
In addition to the inks, Insulectro will be exhibiting some exceptional substrates from Italian manufacturer Coveme. Coveme’s technology introduces in the market a new solution based on a high deep thermoforming bi-oriented polyester film with special coating on both sides that enhances printability, scratch resistance and formability.
“Coveme’s Kemafoil® KTF HC and HCH is clear Bi-oriented thermoformable polyester film, treated one or two sides. KTF HC is treated outside with a dual cure coating with abrasion and scratch resistance after UV curing,” Miller stated.
Insulectro Printed Electronics’ Product Specialist David Schneider is excited about the array of conductive inks offered, “DuPont is the predominant manufacturer of silver, copper, carbon, and dielectric inks. Insulectro’s got them all. Whether your application is membrane touch switches or printable heaters, there is an advanced material for your needs. And, in the wearables market, stretchable inks are rewriting the electronics gamebook. In our booth, you’ll see real examples of cutting-edge technologies available today.”
Miller added, “There’s lots of excitement this year for Insulectro Printed Electronics. Stop by our booth, V37, at IDTECHEX’s Printed Electronics World 2019 and let’s get acquainted. Wherever you are manufacturing printed electronics – Minneapolis, Chicago, Dallas, Silicon Valley, Southern California, Denver, Phoenix, Salt Lake City, Northwest, Northeast or Mid-Atlantic and Toronto, Ontario – we are there to service you.”
About Insulectro
Insulectro is the largest supplier of PCB and PE materials. Insulectro combines its premier product offering with local inventory in strategic stocking locations across the country, fabrication capabilities and backed up by expert customer and technical support services.
Insulectro supplies advanced engineered materials manufactured by DuPont Advanced Materials, Kodak, Chromaline, 3M, Coveme, DuPont Circuit & Packaging Materials, Isola, LCOA®, CAC, Inc., Integral Technology, Pacothane, Oak Mitsui, Shikoku, Saint Gobain, and Focus Tech Chemicals.
Suggested Items
RF PCB Design Tips and Tricks
05/08/2025 | Cherie Litson, EPTAC MIT CID/CID+There are many great books, videos, and information online about designing PCBs for RF circuits. A few of my favorite RF sources are Hans Rosenberg, Stephen Chavez, and Rick Hartley, but there are many more. These PCB design engineers have a very good perspective on what it takes to take an RF design from schematic concept to PCB layout.
Trouble in Your Tank: Causes of Plating Voids, Pre-electroless Copper
05/09/2025 | Michael Carano -- Column: Trouble in Your TankIn the business of printed circuit fabrication, yield-reducing and costly defects can easily catch even the most seasoned engineers and production personnel off guard. In this month’s column, I’ll investigate copper plating voids with their genesis in the pre-plating process steps.
Elephantech: For a Greener Tomorrow
04/16/2025 | Marcy LaRont, PCB007 MagazineNobuhiko Okamoto is the global sales and marketing manager for Elephantech Inc., a Japanese startup with a vision to make electronics more sustainable. The company is developing a metal inkjet technology that can print directly on the substrate and then give it a copper thickness by plating. In this interview, he discusses this novel technology's environmental advantages, as well as its potential benefits for the PCB manufacturing and semiconductor packaging segments.
Trouble in Your Tank: Organic Addition Agents in Electrolytic Copper Plating
04/15/2025 | Michael Carano -- Column: Trouble in Your TankThere are numerous factors at play in the science of electroplating or, as most often called, electrolytic plating. One critical element is the use of organic addition agents and their role in copper plating. The function and use of these chemical compounds will be explored in more detail.
IDTechEx Highlights Recyclable Materials for PCBs
04/10/2025 | IDTechExConventional printed circuit board (PCB) manufacturing is wasteful, harmful to the environment and energy intensive. This can be mitigated by the implementation of new recyclable materials and technologies, which have the potential to revolutionize electronics manufacturing.