Toray Creates Revolutionary PPS Film for 5G Circuit Boards
December 23, 2019 | Toray IndustriesEstimated reading time: 2 minutes
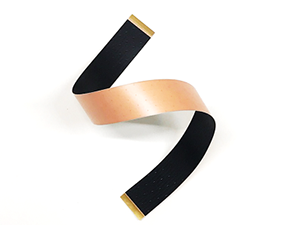
Toray Industries, Inc., announced that it has created a polyphenylene sulfide (PPS) film that maintains the outstanding dielectric characteristics—or low dielectric losses of electrical energy—flame retardancy, and chemical robustness of that polymer while remaining thermally resistant at 40°C higher than conventional counterparts. The new film resists deformation and is dimensionally stable near its melting point. PPS is a super engineering plastic that also offers excellent electrical insulation. It is crystalline, with a melting point of 280°C.
Employing the new film in flexible printed circuits offering 5G and other fast data rates would offer two key benefits. First, the film would cut the transmission losses of communication devices at high frequencies. Second, it would help stabilize high-speed communication across the temperature and humidity spectrums. Flexible printed circuits are film-like wiring boards in which electrical circuits are formed on base materials from bonding thin, soft insulating base films with copper foil or other conductive metals.
Toray has already completed the technology for the new film on a pilot basis, and looks to have a mass production setup in place during fiscal 2020 that would help swiftly popularize devices in the fast-expanding 5G arena. 5G is commanding attention as an advanced platform for delivering outstanding speed capacity, multi-connectivity, and low latency. It harnesses frequency bands below 6 GHz and above 20 GHz.
Development efforts have seen the emergence of practical liquid crystal polymer (LCP) films as flexible printed circuit substrate materials needed for 5G. The dielectric properties of such films reduce transmission losses in high-frequency bands. These films also offer thermal resistance when soldering circuit boards. The expense and processing issues of LCP films fueled the exploration of other materials that could overcome those shortcomings.
Generally PPS film offers superior flame retardancy and chemical resistance while matching or exceeding the dielectric properties of LCP film, and is far less vulnerable to temperature and humidity extremes. On the downside, PPS film deforms easily at high temperatures and provides insufficient resistance to heat when soldering circuit boards.
These considerations drove Toray to blaze a new trail in film design. It was in the course of that effort that it developed a proprietary technology that controls the crystal structure of PPS films. It thereby maintained the outstanding properties of PPS polymer while dramatically increasing thermal resistance.
Testing to 250°C confirmed that Toray’s new PPS film does not deform. Increasing thermal resistance should make it possible to employ existing processing facilities of circuit boards. Toray attained a low coefficient of thermal expansion in the thickness direction of 98 ppm/°C by employing technology it has amassed over many years to control the orientation of film molecular chains. The diverse applications that leveraging those features, including 5G transmission cables and antennas, should enable the design of smaller, multi-layered circuit boards.
By taking advantage of the high thermal dimensional stability and cost-competitiveness of TORELINA, its biaxially-oriented PPS film, Toray looks to secure the adoption of its new film in the FPC market, particularly for smartphones, and thereafter cultivate diverse applications, including for vehicular usage and base stations. In so doing, the company will create new value in keeping with its corporate philosophy of contributing to society through innovative ideas, technologies, and products.
Suggested Items
Designers Notebook: Basic PCB Planning Criteria—Establishing Design Constraints
07/22/2025 | Vern Solberg -- Column: Designer's NotebookPrinted circuit board development flows more smoothly when all critical issues are predefined and understood from the start. As a basic planning strategy, the designer must first consider the product performance criteria, then determine the specific industry standards or specifications that the product must meet. Planning also includes a review of all significant issues that may affect the product’s manufacture, performance, reliability, overall quality, and safety.
I-Connect007 Editor’s Choice: Five Must-Reads for the Week
07/18/2025 | Nolan Johnson, I-Connect007It may be the middle of the summer, but the news doesn’t quit, and there’s plenty to talk about this week, whether you’re talking technical or on a global scale. When I have to choose six items instead of my regular five, you know it’s good. I start by highlighting my interview with Martyn Gaudion on his latest book, share some concerning tariff news, follow that up with some promising (and not-so-promising) investments, and feature a paper from last January’s inaugural Pan-European Design Conference.
Elephantech Launches World’s Smallest-Class Copper Nanofiller
07/17/2025 | ElephantechJapanese deep-tech startup Elephantech has launched its cutting-edge 15 nm class copper nanofiller – the smallest class available globally. This breakthrough makes Elephantech one of the first companies in the world to provide such advanced material for commercial use.
Copper Price Surge Raises Alarms for Electronics
07/15/2025 | Global Electronics Association Advocacy and Government Relations TeamThe copper market is experiencing major turbulence in the wake of U.S. President Donald Trump’s announcement of a 50% tariff on imported copper effective Aug. 1. Recent news reports, including from the New York Times, sent U.S. copper futures soaring to record highs, climbing nearly 13% in a single day as manufacturers braced for supply shocks and surging costs.
I-Connect007 Editor’s Choice: Five Must-Reads for the Week
07/11/2025 | Andy Shaughnessy, Design007 MagazineThis week, we have quite a variety of news items and articles for you. News continues to stream out of Washington, D.C., with tariffs rearing their controversial head again. Because these tariffs are targeted at overseas copper manufacturers, this news has a direct effect on our industry.I-Connect007 Editor’s Choice: Five Must-Reads for the Week