-
- News
- Books
Featured Books
- smt007 Magazine
Latest Issues
Current IssueSupply Chain Strategies
A successful brand is built on strong customer relationships—anchored by a well-orchestrated supply chain at its core. This month, we look at how managing your supply chain directly influences customer perception.
What's Your Sweet Spot?
Are you in a niche that’s growing or shrinking? Is it time to reassess and refocus? We spotlight companies thriving by redefining or reinforcing their niche. What are their insights?
Moving Forward With Confidence
In this issue, we focus on sales and quoting, workforce training, new IPC leadership in the U.S. and Canada, the effects of tariffs, CFX standards, and much more—all designed to provide perspective as you move through the cloud bank of today's shifting economic market.
- Articles
- Columns
- Links
- Media kit
||| MENU - smt007 Magazine
ASYMTEK Elevates the Excellence of Electronics with Advanced Dispensing, Coating, and Software Solutions at IPC APEX EXPO
January 23, 2020 | Nordson ASYMTEKEstimated reading time: 3 minutes
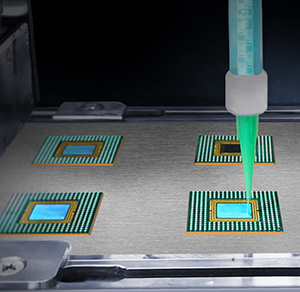
ASYMTEK, a part of Nordson ELECTRONICS SOLUTIONS—a global leader in electronics manufacturing technologies, brings its latest fluid dispensing and conformal coating solutions to IPC APEX EXPO, San Diego, CA, in booth 1611. New at IPC APEX EXPO is the ASYMTEK Vortik™ family of progressive cavity pumps (PCP), with the smallest depositions possible on the market today. The VPs, VPm, and VPg pumps rely on positive displacement to provide continuous needle dispensing of one- and two-component fluids with high-volumetric accuracy, increased reliability, and reduced cycle time. At 0.2 microliters per second, the Vortik VPs offers the lowest flowrate and smallest depositions possible across all PCP pumps available in the market today—delivering precise control of narrow lines and small shots for two-component mixed fluids.
Another ASYMTEK first at IPC APEX EXPO is Vortik's Advanced Calibration Assist with patent-pending ARC™ Technology that ensures high volumetric dispense accuracy for one- and two-component applications. Software-based ARC Technology takes the guesswork out of application setup. With ARC Technology, you can quickly determine optimal settings, such as mix ratios, without manual calculations or time-consuming test iterations.
Also shown for the first time in the USA is the ASYMTEK Qadence™ Closed-Loop Flow Control System in ASYMTEK EasyCoat® 6 software. The Qadence system maintains a stable flow rate by volume for high-quality conformal coating results by automatically compensating for viscosity changes related to temperature, humidity, and batch-to-batch variation. The Qadence system lets you quickly calculate a target flow rate and set process limits with an EasyCoat control routine called the Flow Calculator (patent pending). With the Flow Calculator, a typical 1-hour setup can be completed in 30 minutes and a 30-minute setup in less than 10 minutes.
On display will be the ASYMTEK Panorama™ C-Line for advanced process control in conformal coating. Panorama C-Line components fit seamlessly together to deliver a complete, turnkey solution for coating and curing, with closed-loop controls and data to fuel continuous process improvement. The C-Line will feature a fully integrated ASYMTEK Select Coat® SL-940 with a triple-valve configuration and an ASYMTEK FX-940 Automated Coating Inspection system. Visit the booth to experience a 360° virtual reality tour trip of the Panorama conformal coating line.
Additional products on display will include:
The ASYMTEK Forte™ Series dispensing platform with Forte MAX™ dual-head, real-time skew correction. The new precision dispensing platform includes a dual-simultaneous dispense head with two high-frequency ASYMTEK IntelliJet® Jetting Systems that dispense at the same time to further boost UPH and quality outcomes. The system reduces dispense time by half and automatically adjusts for workpiece and individual component rotational skew.
The ASYMTEK Quantum® in-line and batch system which delivers uncompromising quality, value, and productivity for demanding fluid dispensing applications. The system will feature the Vortik VPm progressive cavity pump for bonding, sealing, encapsulation, and potting applications.
The ASYMTEK Helios® SD-960 Series featuring a two-component thermal interface material application and a new dual-drawer configuration that's ideal for batch manufacturing. Dual drawers allow the first substrate to be dispensed while a second is loaded.
The DIMA C-Turn Flux automates flux dispensing in combination with automated hot bar reflow soldering. It is the ideal solution for LCD solder attach, wire solder attach, and connector and component solder attach applications.
"For 35+ years ASYMTEK has focused on possibilities, continually innovating as technology and electronics evolve," said Peter Bierhuis, president, Nordson ASYMTEK products. "By focusing on what's possible, we bring more to our customers through innovative solutions, customization, application expertise, and award-winning global support. We hope attendees will visit us at booth 1611 to discuss how our solutions can enable their innovations."
IPC APEX EXPO is being held at the San Diego Convention Center, San Diego, CA from February 4-6, 2020. For more information visit our website at www.nordsonasymtek.com.
About ASYMTEK
Headquartered in Carlsbad, CA, USA, ASYMTEK has taken the lead for 35+ years to advance fluid dispensing, conformal coating, and jetting technologies. As part of the Nordson ELECTRONICS SOLUTIONS brand, we focus on immediate and long-term possibilities, continuously innovating as technology and electronics applications evolve. By focusing on what's possible, we bring more to our customers through innovative solutions, customization, applications expertise, and award-winning global support. Visit us at www. nordsonasymtek.com or @nordsonasymtek on social media.
Testimonial
"We’re proud to call I-Connect007 a trusted partner. Their innovative approach and industry insight made our podcast collaboration a success by connecting us with the right audience and delivering real results."
Julia McCaffrey - NCAB GroupSuggested Items
Indium Corporation Promotes Two Leaders in EMEA (Europe, Middle East, and Africa) Markets
08/05/2025 | Indium CorporationWith its commitment to innovation and growth through employee development, Indium Corporation today announced the promotions of Andy Seager to Associate Director, Continental Sales (EMEA), and Karthik Vijay to Senior Technical Manager (EMEA). These advancements reflect their contributions to the company’s continued innovative efforts with customers across Europe, the Middle East, and Africa (EMEA).
MacDermid Alpha Electronics Solutions Unveils Unified Global Website to Deepen Customer, Talent, and Stakeholder Engagement
07/31/2025 | MacDermid Alpha Electronics SolutionsMacDermid Alpha Electronics Solutions, the electronics business of Elements Solutions Inc, today launched macdermidalpha.com - a unified global website built to deepen digital engagement. The launch marks a significant milestone in the business’ ongoing commitment to delivering more meaningful, interactive, and impactful experiences for its customers, talent, and stakeholders worldwide.
KOKI to Showcase Analytical Services and New HF1200 Solder Paste at SMTA Guadalajara 2025
07/31/2025 | KOKIKOKI, a global leader in advanced soldering materials and process optimization services, will exhibit at the SMTA Guadalajara Expo & Tech Forum, taking place September 17 & 18, 2025 at Expo Guadalajara, Salón Jalisco Halls D & E in Guadalajara, Mexico.
Weller Tools Supports Future Talent with Exclusive Donation to SMTA Michigan Student Soldering Competition
07/23/2025 | Weller ToolsWeller Tools, the industry leader in hand soldering solutions, is proud to announce its support of the upcoming SMTA Michigan Expo & Tech Forum by donating a limited-edition 80th Anniversary Black Soldering Set to the event’s student soldering competition.
Koh Young Appoints Tom Hattori as President of Koh Young Japan
07/21/2025 | Koh YoungKoh Young Technology, the global leader in True 3D measurement-based inspection solutions, announced the appointment of Tom Hattori as President of Koh Young Japan (JKY).