-
- News
- Books
Featured Books
- smt007 Magazine
Latest Issues
Current IssueWhat's Your Sweet Spot?
Are you in a niche that’s growing or shrinking? Is it time to reassess and refocus? We spotlight companies thriving by redefining or reinforcing their niche. What are their insights?
Moving Forward With Confidence
In this issue, we focus on sales and quoting, workforce training, new IPC leadership in the U.S. and Canada, the effects of tariffs, CFX standards, and much more—all designed to provide perspective as you move through the cloud bank of today's shifting economic market.
Intelligent Test and Inspection
Are you ready to explore the cutting-edge advancements shaping the electronics manufacturing industry? The May 2025 issue of SMT007 Magazine is packed with insights, innovations, and expert perspectives that you won’t want to miss.
- Articles
- Columns
- Links
- Media kit
||| MENU - smt007 Magazine
Stencils: Not As Simple As They Seem
February 26, 2020 | I-Connect007 Editorial TeamEstimated reading time: 20 minutes
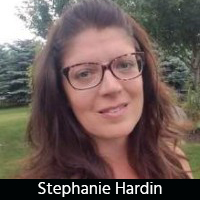
Stephanie Hardin of Integrated Ideas and Technologies Inc. discusses her role in the supply chain as a stencil manufacturer, improvements she sees from micromachined step stencils, and why she believes trying to have standardized stencil layouts is wishful thinking due to the many fluctuating variables.
Nolan Johnson: Stephanie, can you start by introducing yourself?
Stephanie Hardin: I have been with IIT, a manufacturer of stencils, for 19 years. I started as a stencil design technician, and I’m currently vice president and part-owner. From the stencil design standpoint, I’ve seen a lot of changes in components, and they’ve done nothing but shrink the entire time. We utilize an industry-leading fiber laser cutting system that has a complete operator lockout, which is important because the operator can’t make any adjustments to the beam or focal points. The ability of less-equipped machines to adjust those variables creates the potential to produce a less than perfect cut. With small devices, a clean aperture wall that meets the ±0.00015” tolerance requirement is essential.
I work with clients on a regular basis with high-density, high-mix, low-volume builds where there are micro components in the same area as components that require a much more robust solder joint. It’s always about balancing the aperture design and the stencil thickness to print the volume required to create a good solder joint for all devices.
Johnson: It appears there is a tendency to put insufficient solder paste down in these smaller spaces, and then the joints don’t work. There’s also the issue of having to use a thicker stencil, which means more possibility to have issues around the edge of the stencil cutout. How do you balance those things?
Hardin: If you use a thicker stencil and get the paste to release, then you’re also potentially dealing with the issues that arise due to excess solder volume, such as mid-chip solder balls, tombstoning, and bridging, to name a few. Primarily, when we look at these stencil designs, we design with the smallest device on the board as the focus. We then expand the criteria to create a design and stencil thickness combination that’s going to work for everything else on the board.
Before the introduction of step stencils, inevitably, you were doing touch up somewhere. You were making your stencil thick enough to deal with the majority of the components and hand placing the smaller things, or you were doing the opposite and having to touch up the joints on the bigger stuff. It required a lot of extra handling to get it done, but with the step stencils, you can achieve all of it in a single stencil. You are now able to have recessed areas in a three-mil thickness to print a 02001 component, and then you can have a six mil build up on the same stencil for a large connector.
Johnson: I’m not that familiar with a step stencil. How does that get put together?
Hardin: There are a couple of ways to manufacture them. They used to be chemically etched or electroformed, both of which were rather expensive options. Laser-welded stencils are a newer technology, where they take thicker pieces of material, build it up, and weld it to a thinner piece. The latest technology is micro-machining. The micromachining process leaves a much smoother transition in the steps where the laser-welded stencils left a hard 90° angle. Imagine your squeegee trying to move across that surface, and when it hits that 90° angle, it might as well hit a brick wall. It would cause the squeegee to skip up over and potentially cause misprint in that step-up area, at least for part of it.
With the micromachined smooth transitions, the squeegee moves more freely over the stepped area. Two things happen there: less squeegee damage, so your squeegee lasts longer, and the stencil also lasts longer. You don’t have multiple layers that can delaminate in production.
Johnson: It was recently pointed out by somebody working on stencil technology that the features are becoming fine enough that they're even starting to worry about the metal grain and its effect on the application. Is this is something that you find yourselves working with regularly to that almost-microscopic level of detail?
Hardin: Definitely. Some of the aperture openings that we’re dealing with are eight-thousandths of an inch. As far as looking at the physical component goes, it would look like a fleck of pepper on your finger if the component happened to be black in color. That’s the only way you’re going to see it, if at all. This presents issues with paste release. The fine grain stencil materials available now improve paste release before any other coatings are applied, such as a nanocoating. Nanocoatings have also assisted a great deal with enhancing paste release. Nanocoatings also allow for more prints to be completed before the stencil needs to be cleaned.
Johnson: Are you getting stencil patterns delivered to you by the customer that are workable right off the bat, or do you have to do a lot of stencil pattern prep?
Hardin: Typically, there’s quite a bit of prep, unless it’s an OEM that has a set product and has had the time to go through and develop their process and their design library, to achieve the best results in production. Often, OEMs supply their data already modified by in-house designers, that are able to utilize a set design library. Their process is controlled each time; it’s their product, and they build it. They are not dealing with the variations created by customer-specified solder paste, three different types of 0402 capacitors, or a variation in board finish that is inherent when obtaining boards from multiple sources.
The other side of that is the contract manufacturers who, oftentimes, see these new components for the first time and ask us, “What do we do here? How are we going to print this?” They look for recommendations from us on the best design to net a first-time pass. Their client may have supplied the boards, the parts, and specified a stencil thickness. The contract manufacturer may also not have the authority to make any changes to the stencil design, stencil thickness, or solder paste that the client calls out. The complications can compound quickly.
Oftentimes, the footprint that is generated from a generic design library might not work in all instances. The often-overlooked factor when considering aperture design is the actual production environment. When devices are this small, any change in humidity, printer setup, or solder paste management could throw a standardized aperture design layout out the window. You have to be able to design for who’s building it and how their line is set up.
Johnson: In other words, following the guidelines in the datasheet for setting up your pads and your stencil patterns is risky.
Hardin: It gets you in the neighborhood. It usually comes down to starting with the manufacturer-recommended layout for the first build. Then, if issues arise during the build, get back with your stencil manufacturer on what problems you were having and start to modify the design to alleviate the issues. Each manufacturer will recommend a stencil thickness for their device. The trick is taking into consideration the recommended thickness on all devices and creating a stencil that will work.
Johnson: From your perspective, how possible is it to look at the data and know that there's a problem with the stencil upfront? Can you be proactive about modifying that stencil file, or do you have to wait for a person to first article to figure that out?
Hardin: I can be proactive about it to a point. I can look at the design versus the stencil thickness that the client’s asking for. If a 5-mil stencil thickness is requested, I can identify the components that might have problems with that thickness. Even if the device is new to me, I’ll be able to tell if there’s not enough space between the lands, which might create a solder ball issue under the device or not enough of a gap between leads on a multi-lead device that may create a bridging issue. I will also be able to identify concerns with ground pads under leadless devices and recommend a design to mitigate part movement during reflow.
Johnson: Since designers can't trust the datasheet, what else do they need to do?
Hardin: That’s a tough question because there are so many other variables in the production line that contribute to the success or failure of creating that joint. If there’s a different paste being used? Or is the paste is sitting out too long, and the flux is evaporating out? Is there sufficient under board support with the proper combination of squeegee pressure and speed? Are you printing on contact or off contact? It would be difficult for the designer to say it should look like this under optimal conditions where the condition is different in each facility. I’m not sure how they would do that.
Johnson: It sounds like this is highly dependent on the situation.
Hardin: From my experience, based on client feedback with printing issues, it’s difficult to pin that down. On some of the older multi-lead devices, it was a pretty easy thing to look at the specification and say, “They’re calling out a pad that’s awfully long. I’m going to have either a bridge between leads or solder balling out on the toe or heel of my device if I print this entire pad the way it’s designed.” You would have to shorten up the pad a little bit. It is much more difficult to determine ahead of time for the micro-devices. There’s not as much leeway in the manufacturing process to compensate for any other issue because, along with the device size, your process window keeps shrinking and shrinking.
Again, if you were talking about an OEM that had a 100% controlled process and environment where nothing ever changed, it would be easy to work with that OEM and ask, “Where does this pad layout need to be to be successful?” Make the change and go on. But when you get into contract manufacturing, it’s a completely different environment.
Johnson: As a stencil supplier, imagine you’re working with a customer, and all of a sudden, something changes in their process. Things aren't working. They need to make modifications to the stencils. Are we talking about relocating cutouts in the X, Y axes, and changing to different stencil materials or sizes? What are some of the ways you can handle some of those problems?
Hardin: All the things you mentioned. I’d look for specific defect information from them. And from that point, it could be shrinking the pad or changing the pad geometry into a home plate or a reverse home plate. It could also be changing the stencil thickness in that location—anything to affect the volume to net the desired result.
Johnson: Is it commonplace to have this happen at a production customer?
Hardin: It can be initially. Stencils houses do quite a bit of design work for clients to try to get around these things. Again, when you’re dealing with contract manufacturing, it could be that the client’s going to build that board once, and they might not ever see it again. It could be that they’re building that board once, and then there are plans for big production, so they’ll spend the time to go back through and work on any defect data that they had to improve their yield the next time.
Johnson: Do you design work specific to the design of the stencil, or are you going back into the board design itself and suggest changes?
Page 1 of 2
Suggested Items
Driving Innovation: Direct Imaging vs. Conventional Exposure
07/01/2025 | Simon Khesin -- Column: Driving InnovationMy first camera used Kodak film. I even experimented with developing photos in the bathroom, though I usually dropped the film off at a Kodak center and received the prints two weeks later, only to discover that some images were out of focus or poorly framed. Today, every smartphone contains a high-quality camera capable of producing stunning images instantly.
Hands-On Demos Now Available for Apollo Seiko’s EF and AF Selective Soldering Lines
06/30/2025 | Apollo SeikoApollo Seiko, a leading innovator in soldering technology, is excited to spotlight its expanded lineup of EF and AF Series Selective Soldering Systems, now available for live demonstrations in its newly dedicated demo room.
Indium Corporation Expert to Present on Automotive and Industrial Solder Bonding Solutions at Global Electronics Association Workshop
06/26/2025 | IndiumIndium Corporation Principal Engineer, Advanced Materials, Andy Mackie, Ph.D., MSc, will deliver a technical presentation on innovative solder bonding solutions for automotive and industrial applications at the Global Electronics A
Fresh PCB Concepts: Assembly Challenges with Micro Components and Standard Solder Mask Practices
06/26/2025 | Team NCAB -- Column: Fresh PCB ConceptsMicro components have redefined what is possible in PCB design. With package sizes like 01005 and 0201 becoming more common in high-density layouts, designers are now expected to pack more performance into smaller spaces than ever before. While these advancements support miniaturization and functionality, they introduce new assembly challenges, particularly with traditional solder mask and legend application processes.
Knocking Down the Bone Pile: Tin Whisker Mitigation in Aerospace Applications, Part 3
06/25/2025 | Nash Bell -- Column: Knocking Down the Bone PileTin whiskers are slender, hair-like metallic growths that can develop on the surface of tin-plated electronic components. Typically measuring a few micrometers in diameter and growing several millimeters in length, they form through an electrochemical process influenced by environmental factors such as temperature variations, mechanical or compressive stress, and the aging of solder alloys.