-
- News
- Books
Featured Books
- design007 Magazine
Latest Issues
Current IssueProper Floor Planning
Floor planning decisions can make or break performance, manufacturability, and timelines. This month’s contributors weigh in with their best practices for proper floor planning and specific strategies to get it right.
Showing Some Constraint
A strong design constraint strategy carefully balances a wide range of electrical and manufacturing trade-offs. This month, we explore the key requirements, common challenges, and best practices behind building an effective constraint strategy.
All About That Route
Most designers favor manual routing, but today's interactive autorouters may be changing designers' minds by allowing users more direct control. In this issue, our expert contributors discuss a variety of manual and autorouting strategies.
- Articles
- Columns
- Links
- Media kit
||| MENU - design007 Magazine
Ventec Re-Certified to AS9100 Revision D in UK
March 10, 2020 | Ventec International GroupEstimated reading time: 2 minutes
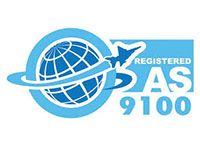
Ventec International Group Co., Ltd., a world leader in the production of polyimide and high reliability epoxy laminates and prepregs and specialist provider of thermal management and IMS solutions, is pleased to announce that the company’s European headquarters in Leamington Spa, UK has successfully been re-certified with AS9100 Revision D in accordance with the Aerospace Supplier Quality System Certification Scheme EN 9104-001:2103 by SGS.
Ventec’s UK and China facilities are certified to AS9100 Revision D quality standard, providing OEMs and PCB fabrication customers servicing the aviation, space and defense industries access to a fully accredited supply chain for high reliability laminates and prepregs. This standard includes ISO 9001:2015 quality management system requirements and specifies additional aviation, space and defense industry requirements, definitions and notes.
To qualify and meet the strict certification criteria of the certification, Ventec’s material manufacturing & supply processes undergo a thorough assessment for stringent aerospace requirements. Attaining and maintaining certification is critical to Ventec’s mission to consistently offer aerospace- and automotive-grade materials to the market.
Anthony Jackson, General Manager of the UK facility commented: “Achieving and maintaining highest quality standards is the key to our success and continued growth. I am delighted with our successful re-certification audit which reflects the hard work of the entire Ventec team in implementing and practicing the highest levels of process quality. Our commitment to managing delivered quality to the highest standards provides our customer with the reassurance of being their strategic partner of choice in their own safety critical supply chains.”
From manufacture through fabrication and global delivery, Ventec's high quality product portfolio of polyimides, high reliability FR-4, tec-speed range of high speed/low loss materials and tec thermal range of IMS materials are all covered by the accreditation.
For more information about Ventec's solutions and the company's wide variety of products, please visit www.venteclaminates.com.
About Ventec International Group
Ventec International Group Co., Ltd. (6672 TT) is a premier supplier to the Global PCB industry. With volume manufacturing facilities in Taiwan and China and distribution locations and manufacturing sites in both the US and Europe, Ventec specializes in advanced copper clad glass reinforced and metal backed substrates. Ventec materials, which include high-quality enhanced FR-4, high-speed/low-loss- and high-performance IMS material technology and an advanced range of thermal management solutions, are manufactured by Ventec using strict quality-controlled processes that are certified to AS9100 Revision D, IATF 16949:2016 and ISO 9001:2015, and are backed by a fully controlled and managed global supply chain, sales- and technical support-network. For more information, visit www.venteclaminates.com.
Testimonial
"We’re proud to call I-Connect007 a trusted partner. Their innovative approach and industry insight made our podcast collaboration a success by connecting us with the right audience and delivering real results."
Julia McCaffrey - NCAB GroupSuggested Items
50% Copper Tariffs, 100% Chip Uncertainty, and a Truce
08/19/2025 | Andy Shaughnessy, I-Connect007If you’re like me, tariffs were not on your radar screen until a few months ago, but now political rhetoric has turned to presidential action. Tariffs are front-page news with major developments coming directly from the Oval Office. These are not typical times. President Donald Trump campaigned on tariff reform, and he’s now busy revamping America’s tariff policy.
Global PCB Connections: Understanding the General Fabrication Process—A Designer’s Hidden Advantage
08/14/2025 | Markus Voeltz -- Column: Global PCB ConnectionsDesigners don’t need to become fabricators, but understanding the basics of PCB fabrication can save you time, money, and frustration. The more you understand what’s happening on the shop floor, the better you’ll be able to prevent downstream issues. As you move into more advanced designs like HDI, flex circuits, stacked vias, and embedded components, this foundational knowledge becomes even more critical. Remember: the fabricator is your partner.
MKS’ Atotech to Participate in IPCA Electronics Expo 2025
08/11/2025 | AtotechMKS Inc., a global provider of enabling technologies that transform our world, announced that its strategic brands ESI® (laser systems) and Atotech® (process chemicals, equipment, software, and services) will showcase their latest range of leading manufacturing solutions for printed circuit board (PCB) and package substrate manufacturing at the upcoming 17th IPCA Show to be held at Pragati Maidan, New Delhi from August 21-23, 2025.
MKS Showcases Next-generation PCB Manufacturing Solutions at the Thailand Electronics Circuit Asia 2025
08/06/2025 | MKS Instruments, Inc.MKS Inc, a global provider of enabling technologies that transform our world, today announced its participation in Thailand Electronics Circuit Asia 2025 (THECA 2025), taking place August 20–22 at BITEC in Bangkok.
Point2 Technology, Foxconn Interconnect Technology Partner to Revolutionize AI Cluster Scalability with Terabit-Speed Interconnect
08/06/2025 | BUSINESS WIREPoint2 Technology, a leading provider of ultra-low-power, low-latency mixed-signal SoC solutions for multi-terabit interconnect, and Foxconn Interconnect Technology (FIT), a global leader in precision interconnect solutions, have signed a Memorandum of Understanding (MOU) to accelerate the commercialization of next-generation Active RF Cable (ARC) and Near Pluggable e-Tube (NPE) solutions.