-
- News
- Books
Featured Books
- design007 Magazine
Latest Issues
Current IssueAll About That Route
Most designers favor manual routing, but today's interactive autorouters may be changing designers' minds by allowing users more direct control. In this issue, our expert contributors discuss a variety of manual and autorouting strategies.
Creating the Ideal Data Package
Why is it so difficult to create the ideal data package? Many of these simple errors can be alleviated by paying attention to detail—and knowing what issues to look out for. So, this month, our experts weigh in on the best practices for creating the ideal design data package for your design.
Designing Through the Noise
Our experts discuss the constantly evolving world of RF design, including the many tradeoffs, material considerations, and design tips and techniques that designers and design engineers need to know to succeed in this high-frequency realm.
- Articles
- Columns
- Links
- Media kit
||| MENU - design007 Magazine
Siemens and Valor: Two Complementary DFM Technologies
April 1, 2020 | Andy Shaughnessy, I-Connect007Estimated reading time: 4 minutes
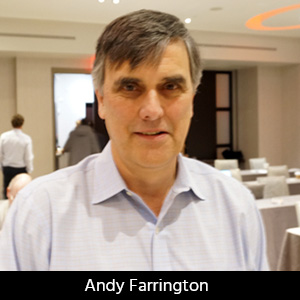
Before IPC APEX EXPO kicked off, I attended a Siemens seminar in San Diego on smart manufacturing for electronics and the integration of technologies from Siemens’ digital industry software and Valor. Afterward, I spoke with Andy Farrington, director of portfolio development for the Americas, about the event, as well as some of the hot topics and solutions that the speakers addressed.
Andy Shaughnessy: Andy, this has been a pretty interesting seminar that focused on smart manufacturing for electronics, among other things. Tell us about it.
Andy Farrington: It was a seminar for the smart factory for electronics, which is a big focus for us. At IPC APEX EXPO 2020, we invited several people to learn and get more knowledge about what we have to offer. It was a whole-day event. Approximately 20 people attended all of the sessions, and we covered a lot of topics—from the engineering kickoff, focused on the industry itself, to trends we see in terms of marketplace challenges. Then, we talked a little more about what we have for solutions to address that from an engineering process standpoint, material management, manufacturing execution, etc. I thought it was good that we got a chance to expose people to that. The last presentation was fantastic, by Computrol’s Farid Anani. It was an outstanding example of what happens when people implement this technology and what kind of value you get from it.
Shaughnessy: It looks like a front-to-back smart manufacturing solution that you have.
Farrington: Yes. We talked about using the digital twin, which is our way of talking about how to have a virtual version of the product. If you can do that, then you can understand it better, and it doesn’t cost as much money to make changes in the virtual world versus doing it in the real world. That can be from creating plant simulation of a factory to doing what-if scenarios and trying different layouts. Our customers get tremendous value from that. Today, we had mixed attendance of people familiar with our product, or it was new to them. There were a lot of good questions during the breaks. It’s always nice to share personal experiences; sometimes, making those connections is more important than the seminar.
Shaughnessy: It seems Valor was a key part of the Mentor merger for Siemens.
Farrington: That was one thing that we talked about this morning: Why did Siemens buy Mentor? There were a lot of reasons, but was with the value of the electronics solutions, in particular, Siemens traditionally focused on the mechanical side of manufacturing. Now, with the integration of the Valor solutions, that gives us a full portfolio to do electronic design all the way through manufacturing. Valor tools integrated into Opcenter Execution, which provides a complete solution all the way through to box build.
Shaughnessy: The discussion about addressing the gap between the ERP system and the shop floor where the people are sometimes the weakest link was interesting.
Farrington: Sometimes. That whole integration of the ERP is becoming more important to customers. It’s a way for them to see fast cost savings. It’s always surprising when I visit customers’ sites that haven’t implemented our tools, yet I can see all the material on the shop floor. There’s all this cost sitting on the shop floor. If you can find a way to reduce the amount of material on the shop floor, keep it in inventory, and delivery as needed. All ERP can do for you is tell you it’s in the warehouse; it can’t tell you whether it’s on the line or in a kitting station. I’ve seen operators on the shop floor work over a line, steal a reel off the line, and move it over to theirs. They have no traceability at all.
Shaughnessy: Everybody talks about the smart factory and is all for it, but when we talk to fabricators and assemblers in America, many say they don’t know how to do it. Do you see resistance? Are they curious about the smart factory?
Farrington: There are always situations where people are resistant to change if they use a solution now that they believe works well. If they give us an opportunity to look at their factory and do an assessment, we can find areas where they can make improvements, and that’s what they want to hear. Sometimes, a smart factory approach is a little overwhelming to them because it feels like they have to change everything. We can get them there. Farid talked about his journey at Computrol. He started it in 2007, and you can’t solve it immediately; you have to focus on the long term.
I see companies that are interested in the smart factory, but they want a return on investment relatively fast. That’s why we try to lead them down this path of having a conversation on material management because we think you can get the biggest bang for your buck, and we can show some quick ROI, which is what management wants to see.
Shaughnessy: In some of these places, it’s better to start from scratch than to try to retrofit.
Farrington: We have a few places that are bringing brand new and lines in, and that’s definitely easier.
Shaughnessy: Thanks for having me here today, Andy.
Farrington: No problem. Thank you.
Editor’s note: Download your free copy of Siemens’ book, The Printed Circuit Assembler's Guide to… Advanced Manufacturing in the Digital Age, and view other educational titles in our full library.
Suggested Items
Electronics Industry Wrestles with Cost Pressures and Weaker Profitability
07/07/2025 | Global Electronics AssociationElectronics manufacturers are facing rising material and labor costs according to the Global Electronics Association’s June Sentiment of the Global Electronics Manufacturing Supply Chain Report.
Naprotek Appoints James Eisenhaure as Chief Financial Officer
07/07/2025 | Naprotek LLCNaprotek, LLC, a leading provider of mission-critical electronics technology solutions, today announced that James Eisenhaure has been appointed Chief Financial Officer, effective June 30. Eisenhaure has been serving as interim CFO since earlier this year and now formally steps into the role.
Yannick Green Joins Technica USA as Business Development/Account Manager for Northern California and Northern Nevada
07/07/2025 | Technica USATechnica USA is proud to announce that industry veteran Yannick Green has rejoined Team Technica as Business Development/Account Manager, supporting both supply partners and PCBA customers across Northern California and Northern Nevada.
Hon Hai Education Foundation Continues to Promote Quantum Education
07/04/2025 | FoxconnHon Hai Education Foundation has long been committed to promoting forward-looking technology education in Taiwan's high schools, and held the "High School Quantum Teacher Training Camp" in Tainan City on July 1.
Incap UK Achieves JOSCAR Zero Accreditation
07/04/2025 | IncapIncap Electronics UK has been accredited under JOSCAR Zero, a new sustainability-focused extension of the defence and aerospace sector’s supplier assurance system.