-
- News
- Books
Featured Books
- smt007 Magazine
Latest Issues
Current IssueSupply Chain Strategies
A successful brand is built on strong customer relationships—anchored by a well-orchestrated supply chain at its core. This month, we look at how managing your supply chain directly influences customer perception.
What's Your Sweet Spot?
Are you in a niche that’s growing or shrinking? Is it time to reassess and refocus? We spotlight companies thriving by redefining or reinforcing their niche. What are their insights?
Moving Forward With Confidence
In this issue, we focus on sales and quoting, workforce training, new IPC leadership in the U.S. and Canada, the effects of tariffs, CFX standards, and much more—all designed to provide perspective as you move through the cloud bank of today's shifting economic market.
- Articles
- Columns
- Links
- Media kit
||| MENU - smt007 Magazine
Rehm Announces Development of New Production Technologies for Solid State Batteries
April 9, 2020 | Rehm Thermal SystemsEstimated reading time: 3 minutes
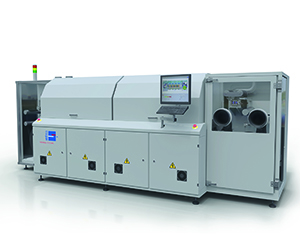
Rehm is working on the development of new production technologies for solid state batteries as part of a research cooperation.
Electric mobility is both an opportunity and a challenge for plant and mechanical engineering, for research and development, for the electronics industry, and for many other sectors. Rehm Thermal Systems is taking on this challenge: With the ARTEMYS research project, Rehm is working together with research institutes and industrial partners to develop materials and production technologies for solid state batteries—the promising next generation of lithium-ion batteries. This technology and innovation leader from Blaubeuren-Seißen in Germany also has extensive expertise in the drying and coating systems used, for example, in manufacturing conventional battery packs.
Higher energy density, shorter charging time, longer service life, improved safety characteristics as well as environmentally friendly and resource-saving production are all required for the next generation of batteries for electric mobility. Solid state batteries are a promising concept for achieving these goals. The flammable liquid electrolyte is replaced by a solid body, which ensures safe operation even without cooling. This also prevents leakage of safety-critical and toxic substances from the outset, thereby reducing the safety measures which are required for conventional Li-ion batteries. Another advantage is the high energy density. In terms of electric mobility, this means that a higher range can be achieved with the same installation space, or that less installation space is required for the same range, thereby saving even more weight. In addition to use in the field of electric mobility, the improved safety properties and increased energy density also offer advantages for any applications in which conventional Li-ion batteries can be replaced by solid state batteries.
As part of the ARTEMYS research project funded by the Federal Ministry of Education and Research (BMBF), Rehm is working together with various research institutes and industrial partners, including the BMW Group, BASF SE and Thyssen Krupp System Engineering GmbH, to develop these next generation batteries. Suitable process technologies are being developed to produce, among other things, fully ceramic solid state batteries. With this
technology, both the cathodes and the electrolyte consist of oxidic or sulfidic materials, which are developed by the project partners. These batteries not only function without any liquid components but also without any polymer content. Rehm is working on the cooperative project to develop scalable production solutions for the drying and sintering of oxide composite cathodes and solid electrolyte separators.
Technology for conventional Lithium-Ion battery packs
Rehm has many years of experience with drying processes for various industrial applications. This also includes film drying. Drying the electrodes is an important step in the production process for manufacturing lithium-ion batteries. With its reel-to-reel drying system RDS Battery, Rehm provides a concept that can be used to achieve the drying temperature via infrared radiation, convection, or a combination of both heat-transfer mechanisms. The system is primarily designed for research facilities. With the ProtectoXP and ProtectoXC coating systems, Rehm also offers systems that provide solutions for bonding and coating processes for battery system construction and for power electronics.
Furthermore, the Rehm Thermal Systems product portfolio offers additional solutions for the field of power electronics. There is a strong focus on thermal management for the components required for this in order to prevent overheating and any premature failure that may occur as a result of this, even with the heat loss created by the high level of performance. Voids (pores in the soldered joints), in particular, may lead to hot spots. The vacuum option in the soldering process for Rehm systems is increasingly being used here to prevent the negative effects of pore formation. The vacuum option is available with the Vision series convection soldering systems, the Condenso series condensation soldering systems, and the Nexus contact soldering system.
About Rehm Thermal Systems
Rehm is a technology and innovation leader in the state-of-the-art, cost-effective manufacturing of electronic assembly groups. It specialises in thermal system solutions for the electronics and photovoltaics industry. Rehm is a globally active manufacturer of reflow soldering systems using convection, condensation or vacuum, drying and coating systems, functional test systems, equipment for the metallisation of solar cells and numerous customised systems. We have a presence in all key growth markets and, as a partner with 30 years of industry experience, we are able to implement innovative production solutions that set new standards.
Testimonial
"We’re proud to call I-Connect007 a trusted partner. Their innovative approach and industry insight made our podcast collaboration a success by connecting us with the right audience and delivering real results."
Julia McCaffrey - NCAB GroupSuggested Items
KOKI to Showcase Analytical Services and New HF1200 Solder Paste at SMTA Guadalajara 2025
07/31/2025 | KOKIKOKI, a global leader in advanced soldering materials and process optimization services, will exhibit at the SMTA Guadalajara Expo & Tech Forum, taking place September 17 & 18, 2025 at Expo Guadalajara, Salón Jalisco Halls D & E in Guadalajara, Mexico.
Weller Tools Supports Future Talent with Exclusive Donation to SMTA Michigan Student Soldering Competition
07/23/2025 | Weller ToolsWeller Tools, the industry leader in hand soldering solutions, is proud to announce its support of the upcoming SMTA Michigan Expo & Tech Forum by donating a limited-edition 80th Anniversary Black Soldering Set to the event’s student soldering competition.
Silicon Mountain Contract Services Enhances SMT Capabilities with New HELLER Reflow Oven
07/17/2025 | Silicon Mountain Contract ServicesSilicon Mountain Contract Services, a leading provider of custom electronics manufacturing solutions, is proud to announce a significant upgrade to its SMT production capability with the addition of a HELLER 2043 MK5 10‑zone reflow oven to its Nampa facility.
SHENMAO Strengthens Semiconductor Capabilities with Acquisition of PMTC
07/10/2025 | SHENMAOSHENMAO America, Inc. has announced the acquisition of Profound Material Technology Co., Ltd. (PMTC), a premier Taiwan-based manufacturer of high-performance solder balls for semiconductor packaging.
Hands-On Demos Now Available for Apollo Seiko’s EF and AF Selective Soldering Lines
06/30/2025 | Apollo SeikoApollo Seiko, a leading innovator in soldering technology, is excited to spotlight its expanded lineup of EF and AF Series Selective Soldering Systems, now available for live demonstrations in its newly dedicated demo room.