-
- News
- Books
Featured Books
- design007 Magazine
Latest Issues
Current IssueProper Floor Planning
Floor planning decisions can make or break performance, manufacturability, and timelines. This month’s contributors weigh in with their best practices for proper floor planning and specific strategies to get it right.
Showing Some Constraint
A strong design constraint strategy carefully balances a wide range of electrical and manufacturing trade-offs. This month, we explore the key requirements, common challenges, and best practices behind building an effective constraint strategy.
All About That Route
Most designers favor manual routing, but today's interactive autorouters may be changing designers' minds by allowing users more direct control. In this issue, our expert contributors discuss a variety of manual and autorouting strategies.
- Articles
- Columns
- Links
- Media kit
||| MENU - design007 Magazine
Ventec's Chicago (USA) Facility Receives ISO 9001:2015 Certification
April 15, 2020 | Ventec International GroupEstimated reading time: 1 minute
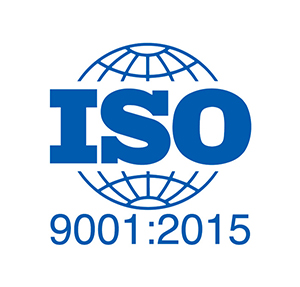
Ventec International Group Co., Ltd. has achieved ISO 9001:2015 certification for its Quality Management System at its US-facility in Chicago, following an audit by certifying body Intertek.
ISO 9001:2015 sets out the criteria for a quality management system and is based on a number of quality management principles including a strong customer focus, the motivation and implication of top management, the process approach and continual improvement. The excellent professional support from Steve Williams from TracQMS and the hard work put in by Ventec's Operations Manager Israel Cadenas and the entire Ventec Chicago staff was rewarded with a perfect certification audit. Ventec's Fullerton facility is next up on the ISO certification agenda.
"I am very proud to receive this certification at the Chicago facility without any instances of non-conformity," said Jack Pattie, President Ventec (USA). "It recognizes the hard work of Steve, Israel and our entire team and confirms the success of our quality strategy for the benefit of all our customers."
"Ventec maintains robust quality management systems in all its facilities around the world including AS9100 Rev D and IATF 16949:2016, ensuring that all our customers receive reliable, consistent, good quality products and services from us through our fully controlled global supply chain," said Mark Goodwin, COO Europe & Americas.
Ventec International is a world leader in the production of polyimide and high reliability epoxy laminates and prepregs and specialist provider of thermal management and IMS solutions.
For more information about Ventec's solutions and the company's wide variety of products, please visit www.venteclaminates.com.
About Ventec International Group
Ventec International Group Co., Ltd. (6672 TT) is a premier supplier to the Global PCB industry. With volume manufacturing facilities in Taiwan and China and distribution locations and manufacturing sites in both the US and Europe, Ventec specializes in advanced copper clad glass reinforced and metal backed substrates. Ventec materials, which include high-quality enhanced FR-4, high-speed/low-loss- and high-performance IMS material technology and an advanced range of thermal management solutions, are manufactured by Ventec using strict quality-controlled processes that are certified to AS9100 Revision D, IATF 16949:2016 and ISO 9001:2015, and are backed by a fully controlled and managed global supply chain, sales- and technical support-network. For more information, visit www.venteclaminates.com.
Testimonial
"The I-Connect007 team is outstanding—kind, responsive, and a true marketing partner. Their design team created fresh, eye-catching ads, and their editorial support polished our content to let our brand shine. Thank you all! "
Sweeney Ng - CEE PCBSuggested Items
50% Copper Tariffs, 100% Chip Uncertainty, and a Truce
08/19/2025 | Andy Shaughnessy, I-Connect007If you’re like me, tariffs were not on your radar screen until a few months ago, but now political rhetoric has turned to presidential action. Tariffs are front-page news with major developments coming directly from the Oval Office. These are not typical times. President Donald Trump campaigned on tariff reform, and he’s now busy revamping America’s tariff policy.
Global PCB Connections: Understanding the General Fabrication Process—A Designer’s Hidden Advantage
08/14/2025 | Markus Voeltz -- Column: Global PCB ConnectionsDesigners don’t need to become fabricators, but understanding the basics of PCB fabrication can save you time, money, and frustration. The more you understand what’s happening on the shop floor, the better you’ll be able to prevent downstream issues. As you move into more advanced designs like HDI, flex circuits, stacked vias, and embedded components, this foundational knowledge becomes even more critical. Remember: the fabricator is your partner.
MKS’ Atotech to Participate in IPCA Electronics Expo 2025
08/11/2025 | AtotechMKS Inc., a global provider of enabling technologies that transform our world, announced that its strategic brands ESI® (laser systems) and Atotech® (process chemicals, equipment, software, and services) will showcase their latest range of leading manufacturing solutions for printed circuit board (PCB) and package substrate manufacturing at the upcoming 17th IPCA Show to be held at Pragati Maidan, New Delhi from August 21-23, 2025.
MKS Showcases Next-generation PCB Manufacturing Solutions at the Thailand Electronics Circuit Asia 2025
08/06/2025 | MKS Instruments, Inc.MKS Inc, a global provider of enabling technologies that transform our world, today announced its participation in Thailand Electronics Circuit Asia 2025 (THECA 2025), taking place August 20–22 at BITEC in Bangkok.
Point2 Technology, Foxconn Interconnect Technology Partner to Revolutionize AI Cluster Scalability with Terabit-Speed Interconnect
08/06/2025 | BUSINESS WIREPoint2 Technology, a leading provider of ultra-low-power, low-latency mixed-signal SoC solutions for multi-terabit interconnect, and Foxconn Interconnect Technology (FIT), a global leader in precision interconnect solutions, have signed a Memorandum of Understanding (MOU) to accelerate the commercialization of next-generation Active RF Cable (ARC) and Near Pluggable e-Tube (NPE) solutions.