-
- News
- Books
Featured Books
- smt007 Magazine
Latest Issues
Current IssueWhat's Your Sweet Spot?
Are you in a niche that’s growing or shrinking? Is it time to reassess and refocus? We spotlight companies thriving by redefining or reinforcing their niche. What are their insights?
Moving Forward With Confidence
In this issue, we focus on sales and quoting, workforce training, new IPC leadership in the U.S. and Canada, the effects of tariffs, CFX standards, and much more—all designed to provide perspective as you move through the cloud bank of today's shifting economic market.
Intelligent Test and Inspection
Are you ready to explore the cutting-edge advancements shaping the electronics manufacturing industry? The May 2025 issue of SMT007 Magazine is packed with insights, innovations, and expert perspectives that you won’t want to miss.
- Articles
- Columns
- Links
- Media kit
||| MENU - smt007 Magazine
This Month in SMT007 Magazine: How Engineers Can Use SPI Tools for Verification
May 6, 2020 | Nolan Johnson, I-Connect007Estimated reading time: 6 minutes
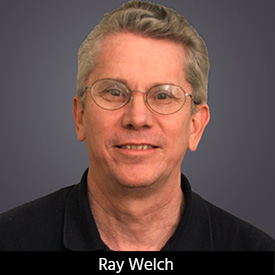
Koh Young’s Ray Welch and Brent Fischthal detail how engineers can work with SPI tools to verify how small they can go in component size with their solder paste application, and how the company’s SPI equipment is helping not only to verify but also to help drive the development collaboration between solder paste and stencil printer manufacturers, and inspection tools and software.
Nolan Johnson: What trends and advancements do you see right now in solder and solder application in the manufacturing process?
Ray Welch: You may be familiar with Chrys Shea’s new SMTA miniaturization test vehicle (MTV). I’ve worked with her and Indium recently, using this new test vehicle; she’s trying to give people a tool to be able to challenge themselves to print smaller and smaller. That test vehicle goes down to 008004 chip components. I don’t know of any customers that we have that are printing that small yet, in terms of chip components, but we have people who are printing near wafer-level prints for RF devices and cellphones. I was working with Indium because they were trying to verify their new pastes and how well they perform for the smaller parts. We’ve been working with our industry partners to help them understand how to use our SPI to be able to get accurate measurements for the smaller and smaller parts.
Johnson: This sounds like a bit of back and forth, building operator skillsets while also verifying that the machines can do that kind of feature size.
Welch: Yes, Chrys and I went to MPM in Hopkinton, Massachusetts. Indium was there, and they wanted to verify several of their new pastes for printing the smallest part at this time. The challenge for us was to make sure that we could measure such small parts, and we can. We performed a DOE, and everything worked out quite well, both in terms of solder paste performance and the Koh Young SPI system. Since then, I helped Indium remotely to use the Koh Young SPI system they have at their shop to verify their pastes. Again, I don’t have any end-users that I know of using the 008004 parts yet, but we’re giving them a system via the aSPIre3 and 10-micron lens resolution to be able to inspect those smaller parts.
Johnson: The equipment and material suppliers have proven that they can deliver the functionality needed for the current smallest parts of the market, even if people may not be using them yet.
Welch: Yes, but the caveat to that is that when-ever we do something in the lab with a bunch of engineers involved, you can oftentimes get very good results. You don’t always get those results when you put it into manufacturing.
Since joining Koh Young in April 2016, I’ve visited about 50 customers delivering our two- to three-day SPI and print process characterization training program. People can’t print those small parts until they improve the discipline of their process. For a number of customers, it seems the operators have hijacked the SPI process. The engineers aren’t there or don’t like to go out to the line except when there are serious issues. Many times, the process engineers aren’t watching over the process like they should or don’t know the process as well as they should, so there will be a reality check when they move to smaller and smaller parts. Johnson: Is it fair to say that the control of the inspection processes on the manufacturing floor with the manufacturing operators who are under one set of incentives for part of their job that may be at odds with being accurate and getting good yields, and not having field failures later
Welch: That’s correct. A lot of engineers don’t want to be called to the line if they don’t have to be, so they leave it to the operators or process technicians. If they don’t visit often enough, then the operators are going to hijack the process and do whatever they think is right. I’ve stood there many times watching an operator pass boards that should have been failed. I call those “wall of shame” examples, where they’ve opened up the inspection tolerances, or the operators are doing whatever they want to do, and then products are escaping SPI. They have a great tool in SPI, but they’re not using the tool as best they can. That will definitely be a challenge when they get to the smaller parts.
Johnson: Let’s paint a possible scenario then. Right now, maybe it’s working, they’re getting by, and they’re doing okay purely by accident. As they move to smaller and smaller parts, that’s going to break at some point. What should they be looking for, and how do you fix it?
Welch: SPI reveals the sins of the process. I’m trying to teach people how to use the tool as best they can, as well as tools and techniques for analyzing the data. It’s also important not to be driven by just defects but by the para-metric data that shows them how well the process is performing in terms of process capability. Then, it’s about improving the process and not just trying to turn off SPI defects.
Johnson: This must be a challenge. You’re providing products that could help customers see fewer field failures and better yield, but by default, it’s exposing the dirty laundry in the process. That can be potentially embarrassing or even job threatening. How do you change that from a threat to a benefit
Brent Fischthal: When Ray delivers these engagements to our customers, he helps them understand how to use SPI. SPI has been around for a while, but not everyone uses it the right way. Sometimes, bad habits form. This specific class resets those bad habits. We’re educating them on how to implement the best practices. Ray does find that wrong processes have been implemented, or that operators are using it incorrectly or sub-optimally. Everybody who has experienced Ray’s class has come away appreciative of the insight they’ve gained. More importantly, most change the way they’ve been doing things right away.
Johnson: If you don’t have support from the C-level executives, then you may encounter managers who have a very different set of objectives.
Fischthal: Most people want to build the best products they can and not have to worry about rework or field failures because an operator was incorrectly using the SPI.
Welch: Yes, but as Nolan was saying, some people have a different objective or performance goals to meet, so even though the engineers might want to make improvements, sometimes they’re held back because the line production doesn’t give them the time. The engineers need to be given the time and line availability to identify issues and opportunities for improvement and then implement the necessary actions. Right now, the biggest thing I see is management often wants to get down to one operator per line and no engineers on the line. That’s not going to work very well when your process isn’t robust—a hands-off process—and none of them are there right now.
To read this entire interview, which appeared in the May 2020 issue of SMT007 Magazine, click here.
Suggested Items
Driving Innovation: Direct Imaging vs. Conventional Exposure
07/01/2025 | Simon Khesin -- Column: Driving InnovationMy first camera used Kodak film. I even experimented with developing photos in the bathroom, though I usually dropped the film off at a Kodak center and received the prints two weeks later, only to discover that some images were out of focus or poorly framed. Today, every smartphone contains a high-quality camera capable of producing stunning images instantly.
Hands-On Demos Now Available for Apollo Seiko’s EF and AF Selective Soldering Lines
06/30/2025 | Apollo SeikoApollo Seiko, a leading innovator in soldering technology, is excited to spotlight its expanded lineup of EF and AF Series Selective Soldering Systems, now available for live demonstrations in its newly dedicated demo room.
Indium Corporation Expert to Present on Automotive and Industrial Solder Bonding Solutions at Global Electronics Association Workshop
06/26/2025 | IndiumIndium Corporation Principal Engineer, Advanced Materials, Andy Mackie, Ph.D., MSc, will deliver a technical presentation on innovative solder bonding solutions for automotive and industrial applications at the Global Electronics A
Fresh PCB Concepts: Assembly Challenges with Micro Components and Standard Solder Mask Practices
06/26/2025 | Team NCAB -- Column: Fresh PCB ConceptsMicro components have redefined what is possible in PCB design. With package sizes like 01005 and 0201 becoming more common in high-density layouts, designers are now expected to pack more performance into smaller spaces than ever before. While these advancements support miniaturization and functionality, they introduce new assembly challenges, particularly with traditional solder mask and legend application processes.
Knocking Down the Bone Pile: Tin Whisker Mitigation in Aerospace Applications, Part 3
06/25/2025 | Nash Bell -- Column: Knocking Down the Bone PileTin whiskers are slender, hair-like metallic growths that can develop on the surface of tin-plated electronic components. Typically measuring a few micrometers in diameter and growing several millimeters in length, they form through an electrochemical process influenced by environmental factors such as temperature variations, mechanical or compressive stress, and the aging of solder alloys.