-
- News
- Books
Featured Books
- smt007 Magazine
Latest Issues
Current IssueSupply Chain Strategies
A successful brand is built on strong customer relationships—anchored by a well-orchestrated supply chain at its core. This month, we look at how managing your supply chain directly influences customer perception.
What's Your Sweet Spot?
Are you in a niche that’s growing or shrinking? Is it time to reassess and refocus? We spotlight companies thriving by redefining or reinforcing their niche. What are their insights?
Moving Forward With Confidence
In this issue, we focus on sales and quoting, workforce training, new IPC leadership in the U.S. and Canada, the effects of tariffs, CFX standards, and much more—all designed to provide perspective as you move through the cloud bank of today's shifting economic market.
- Articles
- Columns
- Links
- Media kit
||| MENU - smt007 Magazine
New Mini-Wave Solder Nozzle Optimizes the Selective Soldering Process
May 28, 2020 | SEHO Systems GmbHEstimated reading time: 2 minutes
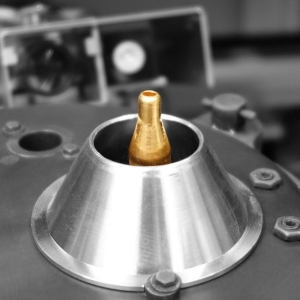
SEHO Systems GmbH, a worldwide leading manufacturer of complete solutions for soldering processes and automated production lines, has registered the patent for a new mini-wave solder nozzle that remarkably improves the selective soldering process in many ways. The patent-pending LongLife solder nozzle is compatible with both SEHO selective soldering systems and different brands.
SEHO’s LongLife solder nozzle is manufactured in a special process without damaging the cubic metal matrix. Contrary to the manufacturing process of a conventional cut surface, this new process does not change the arrangement of atoms at the surface of the nozzle material. Additionally, the mini-wave solder nozzle is coated with a special gold alloy. This combination gives the new solder nozzle some outstanding characteristics.
A particular benefit of the LongLife solder nozzle is its lifetime. Its lifetime is more than three times longer than that of conventional solder nozzles under the same conditions. Therefore, the annual savings potential is remarkable.
Maintenance requirements for the new nozzle are remarkably reduced. The LongLife solder nozzle does not need to be cleaned or re-activated throughout a complete production shift. In addition, there is no activation needed prior to production start: Simply insert the nozzle, turn on the pump and start production. The LongLife nozzle is ready to solder within a few seconds. The advantages are obvious: The LongLife solder nozzle ensures a remarkably increased machine availability since production does not need to be interrupted for manual cleaning or re-activation of the nozzle. Additionally, the costs for typical consumables and chemical activation materials are reduced.
The LongLife solder nozzle also provides benefits from the process-specific point of view. The consistent nozzle wall allows an improved heat energy transfer to the solder joint and the wave height is constantly kept stable, ensuring higher overall process stability. Moreover, the LongLife solder nozzle improves soldering quality. In the case of poorly activated solder nozzles, the nozzle center may shift resulting in solder bridges or washed away SMD components. The LongLife solder nozzle, however, permanently features perfect activation. Therefore, soldering defect rates are remarkably reduced as these failures are a thing of the past.
Also, the ecological footprint of the new solder nozzle speaks for itself. The LongLife nozzle is particularly resource-conserving, compared to conventional solder nozzles. Materials usage is remarkably lower, and due to reduced wear and elimination of chemical activation materials, oxides and dross are reduced as well.
In combination with the ultrasonic solder nozzle cleaner from SEHO, another very special advantage arises: Maintenance staff members and the environment are protected as solvents, chemical activation materials and acids are eliminated from the process.
Testimonial
"In a year when every marketing dollar mattered, I chose to keep I-Connect007 in our 2025 plan. Their commitment to high-quality, insightful content aligns with Koh Young’s values and helps readers navigate a changing industry. "
Brent Fischthal - Koh YoungSuggested Items
Indium Corporation Promotes Two Leaders in EMEA (Europe, Middle East, and Africa) Markets
08/05/2025 | Indium CorporationWith its commitment to innovation and growth through employee development, Indium Corporation today announced the promotions of Andy Seager to Associate Director, Continental Sales (EMEA), and Karthik Vijay to Senior Technical Manager (EMEA). These advancements reflect their contributions to the company’s continued innovative efforts with customers across Europe, the Middle East, and Africa (EMEA).
MacDermid Alpha Electronics Solutions Unveils Unified Global Website to Deepen Customer, Talent, and Stakeholder Engagement
07/31/2025 | MacDermid Alpha Electronics SolutionsMacDermid Alpha Electronics Solutions, the electronics business of Elements Solutions Inc, today launched macdermidalpha.com - a unified global website built to deepen digital engagement. The launch marks a significant milestone in the business’ ongoing commitment to delivering more meaningful, interactive, and impactful experiences for its customers, talent, and stakeholders worldwide.
KOKI to Showcase Analytical Services and New HF1200 Solder Paste at SMTA Guadalajara 2025
07/31/2025 | KOKIKOKI, a global leader in advanced soldering materials and process optimization services, will exhibit at the SMTA Guadalajara Expo & Tech Forum, taking place September 17 & 18, 2025 at Expo Guadalajara, Salón Jalisco Halls D & E in Guadalajara, Mexico.
Weller Tools Supports Future Talent with Exclusive Donation to SMTA Michigan Student Soldering Competition
07/23/2025 | Weller ToolsWeller Tools, the industry leader in hand soldering solutions, is proud to announce its support of the upcoming SMTA Michigan Expo & Tech Forum by donating a limited-edition 80th Anniversary Black Soldering Set to the event’s student soldering competition.
Koh Young Appoints Tom Hattori as President of Koh Young Japan
07/21/2025 | Koh YoungKoh Young Technology, the global leader in True 3D measurement-based inspection solutions, announced the appointment of Tom Hattori as President of Koh Young Japan (JKY).