-
- News
- Books
Featured Books
- smt007 Magazine
Latest Issues
Current IssueSupply Chain Strategies
A successful brand is built on strong customer relationships—anchored by a well-orchestrated supply chain at its core. This month, we look at how managing your supply chain directly influences customer perception.
What's Your Sweet Spot?
Are you in a niche that’s growing or shrinking? Is it time to reassess and refocus? We spotlight companies thriving by redefining or reinforcing their niche. What are their insights?
Moving Forward With Confidence
In this issue, we focus on sales and quoting, workforce training, new IPC leadership in the U.S. and Canada, the effects of tariffs, CFX standards, and much more—all designed to provide perspective as you move through the cloud bank of today's shifting economic market.
- Articles
- Columns
- Links
- Media kit
||| MENU - smt007 Magazine
PDR’s New Affordable PCB X-ray Inspection Systems Offer Quality Image Clarity
June 3, 2020 | PDR X-ray SolutionsEstimated reading time: 1 minute
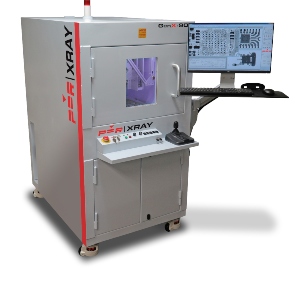
PDR X-ray Solutions is pleased to announce that its 2D and 2D+ X-ray systems have set a new industry standard for high-quality X-ray images at an affordable price. Choosing the correct system for your requirements such as X-ray for quality control or X-ray for process control is vital for the success of both X-ray circuit board inspection programs as well as X-ray semiconductor inspection programs.
PDR’s 90kV X-ray and 130kV X-ray systems are engineered with high-quality materials and craftsmanship and X-ray safety standards exceeding the most stringent requirements for industrial safety. All X-ray non-destructive inspection systems built by PDR are equipped with a suite of X-ray image processing tools and features that incorporate cutting-edge technologies to ensure that your X-ray system delivers quality X-ray images and the power of analytic tools required for a successful X-ray program.
Surface mount and assembly inspection is vital for providing quality product. PDR’s BGA X-ray defect detection and BGA X-ray inspection starts with high quality X-ray images with outstanding image clarity. This makes possible the highest level of analytical tool outcomes utilizing PDR’s proprietary software to perform a high level analysis of BGA packages, X-ray for solder ball sphere void percentage calculations, solder ball area and roundness (spherocity), as well as analytical tools to address X-ray for QFN package inspection, X-ray for CSP package inspection, and X-ray for flip chip inspection as well as X-ray for QFP package inspection and more…
PDR X-ray systems oblique view capability (up to 70°) offers the ability to rotate your sample (PCB, component, SMT device, etc.) to allow X-ray inspection of bond wire quality and perform X-ray bond wire sweep analytics, X-ray of solder fill for PTH – X-ray barrel fill analysis and more.
Whether your X-ray needs are failure analysis to detect and measure die attach voiding, bond wire Attach, etc.) only, or to resolve production issues such as X-ray solder bridging, shorts, opens, insufficient solder, solder paste inspection, head-in-pillow (HiP) issues or solder wetting issues, or simply to validate processes for X-ray inspection of array packages such as BGAs, QFNs, CSP and flip chips, PDR X-ray systems provide the tools to successfully manage your X-ray program with affordability in mind.
PDR systems are made in the USA with worldwide service and support, and one-year or multi-year warranties. PDR can help to determine the best X-ray source and detector depending on the application.
Testimonial
"Our marketing partnership with I-Connect007 is already delivering. Just a day after our press release went live, we received a direct inquiry about our updated products!"
Rachael Temple - AlltematedSuggested Items
Indium Corporation Promotes Two Leaders in EMEA (Europe, Middle East, and Africa) Markets
08/05/2025 | Indium CorporationWith its commitment to innovation and growth through employee development, Indium Corporation today announced the promotions of Andy Seager to Associate Director, Continental Sales (EMEA), and Karthik Vijay to Senior Technical Manager (EMEA). These advancements reflect their contributions to the company’s continued innovative efforts with customers across Europe, the Middle East, and Africa (EMEA).
MacDermid Alpha Electronics Solutions Unveils Unified Global Website to Deepen Customer, Talent, and Stakeholder Engagement
07/31/2025 | MacDermid Alpha Electronics SolutionsMacDermid Alpha Electronics Solutions, the electronics business of Elements Solutions Inc, today launched macdermidalpha.com - a unified global website built to deepen digital engagement. The launch marks a significant milestone in the business’ ongoing commitment to delivering more meaningful, interactive, and impactful experiences for its customers, talent, and stakeholders worldwide.
KOKI to Showcase Analytical Services and New HF1200 Solder Paste at SMTA Guadalajara 2025
07/31/2025 | KOKIKOKI, a global leader in advanced soldering materials and process optimization services, will exhibit at the SMTA Guadalajara Expo & Tech Forum, taking place September 17 & 18, 2025 at Expo Guadalajara, Salón Jalisco Halls D & E in Guadalajara, Mexico.
Weller Tools Supports Future Talent with Exclusive Donation to SMTA Michigan Student Soldering Competition
07/23/2025 | Weller ToolsWeller Tools, the industry leader in hand soldering solutions, is proud to announce its support of the upcoming SMTA Michigan Expo & Tech Forum by donating a limited-edition 80th Anniversary Black Soldering Set to the event’s student soldering competition.
Koh Young Appoints Tom Hattori as President of Koh Young Japan
07/21/2025 | Koh YoungKoh Young Technology, the global leader in True 3D measurement-based inspection solutions, announced the appointment of Tom Hattori as President of Koh Young Japan (JKY).