-
- News
- Books
Featured Books
- smt007 Magazine
Latest Issues
Current IssueSupply Chain Strategies
A successful brand is built on strong customer relationships—anchored by a well-orchestrated supply chain at its core. This month, we look at how managing your supply chain directly influences customer perception.
What's Your Sweet Spot?
Are you in a niche that’s growing or shrinking? Is it time to reassess and refocus? We spotlight companies thriving by redefining or reinforcing their niche. What are their insights?
Moving Forward With Confidence
In this issue, we focus on sales and quoting, workforce training, new IPC leadership in the U.S. and Canada, the effects of tariffs, CFX standards, and much more—all designed to provide perspective as you move through the cloud bank of today's shifting economic market.
- Articles
- Columns
- Links
- Media kit
||| MENU - smt007 Magazine
Eutect and Inmatec Agree on Cooperation
July 9, 2020 | Eutect GmbHEstimated reading time: 3 minutes
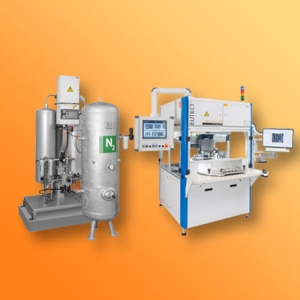
The selective soldering specialist Eutect GmbH and the international market leader in the production of nitrogen and oxygen generators Inmatec GmbH are expanding their cooperation. In recent years, Eutect had already integrated Inmatec’s products into customer projects. Now Inmatec has become the official technology partner of Eutect GmbH.
“Not in every project our customers require soldering under nitrogen. It always depends on the production and the specifications, but in cases where this solution is requested, we have and will integrate the systems for self-producing nitrogen of Inmatec GmbH,” explains Matthias Fehrenbach, Managing Director of Eutect GmbH. As part of the many different soldering processes, inert gas is used to avoid oxides and to ensure high-quality soldered joints. This reduces complex and cost-intensive reworking and repairs. Furthermore, dross formation is avoided. “These measures not only produce improved soldered joints, increased cleanliness of the assemblies and a higher wetting speed, but also reduce the costs that can arise in connection with possible reworking,” Fehrenbach continues. In addition, the consumption of solder and flux can be reduced, thus enabling additional, significant savings.
Inmatec is the international market leader in the production of nitrogen and oxygen generators. Based in Herrsching am Ammersee near Munich, the company has been known for innovative technology “Made in Germany” for over 25 years. With the experience and know-how gained from more than 8,000 installed systems all over the world, the company develops and produces modern, energy-efficient and future-oriented solutions for the in-house production of nitrogen directly on site. Based on many years of experience in the electronics industry, Inmatec has also developed various products especially for the electronics manufacturing industry, which supply nitrogen in high purity at extremely low cost even for small quantities, including an easy-to-use, low-maintenance plug & play solution.
The nitrogen produced by generators meets the requirements for various soldering processes such as selective, wave or reflow soldering. An innovative and extremely efficient technology for extracting nitrogen from the ambient air helps to save costs for uninterrupted N2 supply to a considerable extent. The generators work by using the pressure load change technology. To do this, ambient air is fed at the required pressure into a valve block via an air compressor. This automatically ensures that the compressed air is alternately fed into two adsorption containers filled with a carbon molecular sieve. These alternately switch from filter mode to regeneration mode. Thus, in one container, oxygen as well as carbon dioxide molecules from the ambient air are adsorbed in the sieve, while the sieve regenerates in the second container under compressed air relief. The nitrogen thus obtained is fed into a product container.
By using a special hydrogen catalyst from Inmatec, the efficiency of on-site nitrogen generation can be drastically increased once again. The NKat ensures that generated nitrogen with a quality of 2.5 to 3.0 is enriched with small amounts of hydrogen, which react with the residual oxygen. Thus, the nitrogen is purified to a quality of 5.0 or even 6.0. The technical innovation makes it possible to produce a larger quantity of high-purity nitrogen, especially for THT production, with smaller, more energy-efficient air compressors with an air factor of 2.9 or higher.
When Inmatec systems are integrated into the Eutect plants, the process is controlled via an interface from the Eutect system controller EMI. “This allows the operator to control and monitor the nitrogen production process as well as the selective soldering processes via a single monitor and software. The training for this takes place during initial operation and handover to the customer. The complete system for nitrogen production will be developed together with Inmatec’s specialists and presented to the customer. This means that the customer receives the complete service from two partners from one source,” Fehrenbach emphasises. Furthermore, national and international customers are also supported by Inmatec around the clock in the event of maintenance and service.
Testimonial
"In a year when every marketing dollar mattered, I chose to keep I-Connect007 in our 2025 plan. Their commitment to high-quality, insightful content aligns with Koh Young’s values and helps readers navigate a changing industry. "
Brent Fischthal - Koh YoungSuggested Items
Indium Corporation Promotes Two Leaders in EMEA (Europe, Middle East, and Africa) Markets
08/05/2025 | Indium CorporationWith its commitment to innovation and growth through employee development, Indium Corporation today announced the promotions of Andy Seager to Associate Director, Continental Sales (EMEA), and Karthik Vijay to Senior Technical Manager (EMEA). These advancements reflect their contributions to the company’s continued innovative efforts with customers across Europe, the Middle East, and Africa (EMEA).
MacDermid Alpha Electronics Solutions Unveils Unified Global Website to Deepen Customer, Talent, and Stakeholder Engagement
07/31/2025 | MacDermid Alpha Electronics SolutionsMacDermid Alpha Electronics Solutions, the electronics business of Elements Solutions Inc, today launched macdermidalpha.com - a unified global website built to deepen digital engagement. The launch marks a significant milestone in the business’ ongoing commitment to delivering more meaningful, interactive, and impactful experiences for its customers, talent, and stakeholders worldwide.
KOKI to Showcase Analytical Services and New HF1200 Solder Paste at SMTA Guadalajara 2025
07/31/2025 | KOKIKOKI, a global leader in advanced soldering materials and process optimization services, will exhibit at the SMTA Guadalajara Expo & Tech Forum, taking place September 17 & 18, 2025 at Expo Guadalajara, Salón Jalisco Halls D & E in Guadalajara, Mexico.
Weller Tools Supports Future Talent with Exclusive Donation to SMTA Michigan Student Soldering Competition
07/23/2025 | Weller ToolsWeller Tools, the industry leader in hand soldering solutions, is proud to announce its support of the upcoming SMTA Michigan Expo & Tech Forum by donating a limited-edition 80th Anniversary Black Soldering Set to the event’s student soldering competition.
Koh Young Appoints Tom Hattori as President of Koh Young Japan
07/21/2025 | Koh YoungKoh Young Technology, the global leader in True 3D measurement-based inspection solutions, announced the appointment of Tom Hattori as President of Koh Young Japan (JKY).