-
- News
- Books
Featured Books
- design007 Magazine
Latest Issues
Current IssueProper Floor Planning
Floor planning decisions can make or break performance, manufacturability, and timelines. This month’s contributors weigh in with their best practices for proper floor planning and specific strategies to get it right.
Showing Some Constraint
A strong design constraint strategy carefully balances a wide range of electrical and manufacturing trade-offs. This month, we explore the key requirements, common challenges, and best practices behind building an effective constraint strategy.
All About That Route
Most designers favor manual routing, but today's interactive autorouters may be changing designers' minds by allowing users more direct control. In this issue, our expert contributors discuss a variety of manual and autorouting strategies.
- Articles
- Columns
- Links
- Media kit
||| MENU - design007 Magazine
Estimated reading time: 9 minutes
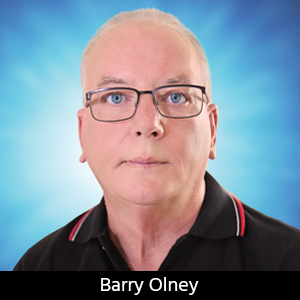
Beyond Design: Split Planes–Reprise
A high-speed digital signal crossing a split in the reference plane impacts at least three aspects of design integrity: signal quality, crosstalk, and EMI. The problem is the impedance discontinuity in the return signal path crossing the split. Any discontinuity in impedance reflects energy back toward the source, particularly the higher-frequency components of the signal. At high frequencies, the return current follows the path of least inductance, which is directly above and/or below the signal trace, but that path is broken by the split. In this case, the return current has to find an alternative path back to the source, creating a larger loop area. In this month’s column, I will review the two common solutions to this issue, plus introduce a third optimal solution for high-speed design.
The Pass-Through Gap
Low-frequency circuits in the audio range can often benefit from splitting the ground planes, whereas digital circuits cannot be effectively isolated from analog circuits using this method. Many years ago, wiring the ground connections to one common point was a great way to eliminate noise in a guitar amplifier, particularly value-based amplifiers. But as frequency increases, the parasitic capacitive and inductive components dominate, and distance or electromagnetic shielding is the only solution.
The key to a successful mixed analog/digital design is functional partitioning, understanding the current return path, and routing control and management—not carving up the ground planes. Analog and digital grounds should be connected together through a low impedance path. It is always better to have just one single reference (ground) plane for a system.
When both analog and digital devices are used on the same PCB, it is usually necessary to partition (not split) the ground plane. The components should be grouped by functionality and positioned such that no digital signals will cross over the analog ground, and no analog signals will cross over the digital ground. Precise partitioning will minimize the trace lengths, improve signal quality, minimize the coupling, and reduce radiated emissions and susceptibility. This is traditionally done by using keep-out zones, whereby no trace can cross through the keep-out area. But this also creates issues in that data and control signals need to go into and out of these sensitive areas.
Figure 1: Route fences used to control routing and isolation.
Particular care needs to be taken with oscillators and switch-mode power supplies that may generate high-frequency electromagnetic fields. If space permits, keep these circuits at least 250 mils from any critical signals to avoid parasitic coupling.
Route fences (a thin elongated keep-out), rather than regional keep-out areas, are a useful tool to control the routing. The ground plane should not be split; rather, a pass-through gap is left in the fences so that data and control signals can enter and leave that area, as seen in Figure 1. At high frequencies, return current follows directly under the signal trace on the reference plane, and as such, will follow the trace through the pass-through gap.
Bridging Planes of Different Potential
These days, it is quite common to have multiple power supplies on a board. Instead of allocating one or two power supplies per plane, it is best to use the dual-stripline layers to provide mixed-signal/power pours and reduce the layer count. This also prevents the overlapping of electromagnetic fields, which creates crosstalk.
This is particularly critical with dual asymmetric stripline configurations where one or two signal layers are sandwiched non-uniformly between two planes, as in Figure 2. It is important to have a clearly defined return current path and to know exactly where the return current will flow. The question is not, “Which plane does the return current flow on?” but, “How is the current distributed on each plane?” Also, if a return path discontinuity exists, then the current tends to divert increasing the loop area, inductance, and delay.
Figure 2: Return-path current density for a dual asymmetric stripline.
A via that provides the connection between signal layers, referenced to planes of different DC potential, creates return path discontinuities. In other words, the return current has to pass between the planes to close the current loop, which increases the inductance, affecting the signal quality. This return current can also excite the parallel plate resonance mode, causing significant electromagnetic radiation from the fringing fields.
If the reference planes are at the same DC potential, then they can be directly connected by stitching vias near the signal via transition to provide shorter paths for the return current. However, if the planes are at different DC potential, then a bypass capacitor can be connected across the planes at these points, as in Figure 3 (left). Unfortunately, this can pass AC noise between the power supplies. Two bypass capacitors, configured as in Figure 3 (right), is a much better solution, as this eliminates the transfer of power supply noise from one supply to another. Although this does add an additional loop area, it also provides additional decoupling to the planes, reducing power distribution network impedance.
Figure 3: Eliminating the transfer of noise in the return path of split power planes (right).
Planar Capacitance
The aforementioned solutions work for most designs, but are they the optimal solution for a high-speed signal to cross a split plane? A slot in the plane under two or more nearby signal traces will usually cause return currents to overlap (shared return path), resulting in some degree of crosstalk. And since dense designs can have 20 or more power regions, spanning just five or so plane pairs, then most complex designs can’t possibly be routed without crossing a split. This issue arises in nearly every intricate design. Adding 100 nF ceramic capacitors to span the split consumes real estate and creates a larger loop area, which, in turn, creates emissions to some extent.
The secret here is to design the stackup in such a way as to make use of planar capacitance, instead of bypass capacitors, by making sure each VDD/VCC region is closely coupled to a continuous ground plane. A plane pair is basically a large capacitor that becomes more efficient as the dielectric becomes thinner. Signal layers must also have an adjacent solid ground return plane to properly steer the electromagnetic wave. By using a combination of three plane layers as in Figure 4, the planar capacitance will provide an alternative return path to transverse the gap. This does not increase the plane count because the next signal layer in the stackup can also use the additional ground plane. Since the skin effect forces current to flow in the outer periphery of the plane at high frequencies, it virtually creates two independent ground planes on the top and bottom surfaces with no return path crosstalk, although it is actually one physical sheet of copper.
Figure 4: 3D view of the split plane stripline configuration.
However, this methodology is also frequency dependant and determined by geometry. As the frequency increases, more power is injected into the plane cavity propagating along the slot. Above 10 GHz, the slot mode radiation begins to couple excessive electromagnetic energy into the adjacent traces.
Properly designed power distribution networks have the power planes tightly coupled to their respective ground planes, as in Figure 5, to provide planar capacitance. Of course, none of this is valid if the two planes are far apart. Stackup data can be transferred to the iCD PDN Planner to demonstrate the impact of planar capacitance on plane resonance for different configurations.
If very thin dielectrics (2–3 mils) are used between the power and ground planes, split planes can have minimal impact on the quality of signal transmission if designed correctly. If the split plane is covered with solid ground planes both above and below in a stripline configuration, radiation will not be an issue. And keep in mind that this also applies to differential pairs traversing a split plane. The return current flows in the reference planes(s)—not the opposite signal trace, particularly if the pair is not very tightly coupled.
One would typically use a minimum gap of 20 mils to isolate planes of dissimilar potential. However, with today’s modern fabrication etching techniques, a 10-mil gap is quite acceptable for low voltage applications (but please check with your fab shop first).
Figure 5: Thin dielectric creates more planar capacitance (iCD Stackup Planner).
Ground planes should never be split with the exception of audio frequency circuits, special RF/microwave applications, and for high-voltage isolation. Functional partitioning and controlled routing is the key to a successful mixed-signal design, while utilizing planar capacitance is an excellent solution for high-speed digital designs up to 10 GHz.
Key Points
- A split in a ground plane creates an impedance discontinuity in the return signal path.
- Low-frequency circuits in the audio range can often benefit from splitting the ground planes.
- The key to a successful mixed analog/digital design is functional partitioning, understanding the current return path, and routing control and management.
- Route fences are a useful tool to control the routing.
- The ground plane should not be split; rather, a pass-through gap is left in the fences so that data and control signals can enter and leave that area.
- Dual-stripline layers can provide mixed-signal/power pours and reduce the layer count.
- If a return path discontinuity exists, then the current tends to divert increasing the loop area, inductance, and delay.
- A via that provides the connection between signal layers, referenced to planes of different DC potential, creates return path discontinuities.
- If the reference planes are at the same DC potential, then they can be directly connected by stitching vias near the signal via transition.
- If the planes are at different DC potential, then a bypass capacitor can be connected across the planes.
- Two bypass capacitors are a much better solution, as this eliminates the transfer of power supply noise from one supply to another.
- A slot in the plane under two or more nearby signal traces will cause return currents to overlap, resulting in some degree of crosstalk.
- The secret for high-speed design is to construct the stackup in such a way as to make use of planar capacitance by making sure each VDD/VCC region is closely coupled to a continuous ground plane.
- If thin dielectrics are used between the power and ground planes, split planes can have minimal impact on the quality of signal transmission.
Further Reading
- B. Olney, “Beyond Design: Stackup Planning, Part 5,” Design007 Magazine, July 2019.
- B. Olney, “Beyond Design: The Proximity Effect,” Design007 Magazine, March 2019.
- B. Olney, “Beyond Design: Split Planes in Multilayer PCBs,” The PCB Design Magazine, March 2015.
- B. Olney, “Beyond Design: The Plain Truth About Plane Jumpers,” The PCB Design Magazine, November 2012.
- H. W. Johnson & M. Graham, High-Speed Digital Design: A Handbook of Black Magic, Prentice Hall, 1993.
- Yuriy Shlepnev, et al. “Stripline With One Solid and One Split Reference Plane: SI List.”
Barry Olney is managing director of In-Circuit Design Pty Ltd (iCD), Australia, a PCB design service bureau that specializes in board-level simulation. The company developed the iCD Design Integrity software incorporating the iCD Stackup, PDN, and CPW Planner. The software can be downloaded at icd.com.au.
More Columns from Beyond Design
Beyond Design: Effective Floor Planning StrategiesBeyond Design: Refining Design Constraints
Beyond Design: The Metamorphosis of the PCB Router
Beyond Design: Radiation and Interference Coupling
Beyond Design: Key SI Considerations for High-speed PCB Design
Beyond Design: Electro-optical Circuit Boards
Beyond Design: AI-driven Inverse Stackup Optimization
Beyond Design: High-speed Rules of Thumb