-
-
News
News Highlights
- Books
Featured Books
- smt007 Magazine
Latest Issues
Current IssueSpotlight on India
We invite you on a virtual tour of India’s thriving ecosystem, guided by the Global Electronics Association’s India office staff, who share their insights into the region’s growth and opportunities.
Supply Chain Strategies
A successful brand is built on strong customer relationships—anchored by a well-orchestrated supply chain at its core. This month, we look at how managing your supply chain directly influences customer perception.
What's Your Sweet Spot?
Are you in a niche that’s growing or shrinking? Is it time to reassess and refocus? We spotlight companies thriving by redefining or reinforcing their niche. What are their insights?
- Articles
- Columns
- Links
- Media kit
||| MENU - smt007 Magazine
Estimated reading time: 4 minutes
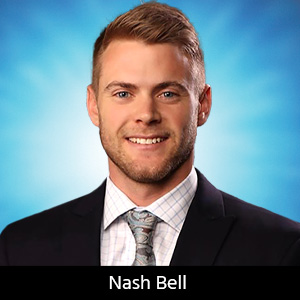
Knocking Down the Bone Pile: Underfill Rework and Solder ‘Squirt Out’
One of the toughest rework challenges is removing and replacing components on PCBs with underfilled components. Many times, underfill is used to provide a shock barrier to component solder joints of handheld electronics, such as notebooks, tablets, and phones. This underfill is added post-test in the assembly process and is dispensed underneath components, such as BGAs, QFNs, and LGAs.
There are several aspects of reworking PCBs that have underfilled components that make them a real challenge when it comes to rework. The underfills’ softening or liquidus temperature is less than that of the reflow temperature of the solder on the PCB. This means that under the BGA, as well as any other underfilled devices, the material softens and expands (Figure 1) before the solder reaching a liquidus state. The pressure this creates then forces out the solder in neighboring solder joints, thereby pushing out the solder when it reaches reflow temperature (Figure 2). The result is a mess of open solder joints, solder balls, and excessive solder in and around the rework area.
The second large challenge in reworking a PCB containing underfilled components lies in the removal of the underfill itself. Due to mechanical forces, either through prying with a removal tool or via a specialty vacuum nozzle removing the underfill, the board may end up with extensive pad and/or laminate damage. In addition, the prying of the component from the board during the removal process may damage pads and laminate underneath the underfilled component. The final challenge is in the tack adhesive strength of the underfill, as this may be of such a high value that the pads are pulled off of the board. This phenomenon may be most pronounced for pads that are no-connects underneath the device.
There are a couple of approaches that hold promise in preventing this solder “squirt out” during the BGA rework process. One of the methods is through the use of a mechanical mill to completely ablate the component from the PCB. No direct heat is applied, but the ensuing debris, mechanical stresses on the joint, and precision required does not make this rework method an option in every case. Another rework method being resurrected is the use of a highly focused laser as the heat source [1]. This method relies on bringing the temperature above liquidus on the solder joint very quickly, thereby not giving the opportunity to reflow neighboring devices while also not allowing the underfill to squirt out.
The challenges of reworking these underfills can be mitigated to a great extent through:
- More thorough training of the operators
- Having the right tool for the right job
- Having the right process and site preparation process
- Controlling collateral heat damage
- Proper reflow profile development
1. Operator Training
BGA rework technicians must be fully trained and must have their skills practiced and developed. These technicians need to be conversant in material selection, including underfill softening agents, fluxes, and solders. They also need to understand the inter-relationship of underfill softening and solder reflow temperatures. In addition, knowledge of how the softening agents may/may not interact with the materials on the PCB would prove helpful. Since X-ray analysis is many times the process debugging tool, the BGA rework technician needs to be schooled in reading X-ray images.
2. The Right Tool for the Right Job
In order for the process to have a chance of success, the right tools—including the type
of rework heat source, a profiling tool, X-ray equipment, and solder excavating tools—need to be used. This will help to have a controlled rework process with repeatable and predictable results.
3. Proper Site and Process Preparation
There are several processes, as well as site preparation steps, to consider once the component on a PCB with underfill has been removed. Proper moisture sensitivity control (per IPC/JEDEC?J-STD-033) methods will help prevent both the board and the component from moisture-induced damage during the rework process. Proper bake-out heat cycles will drive out the moisture from both the component and the board to prevent component “popcorning” and board delamination. An accurate assessment of solder ball size, solder mask condition, and a search for missing or contaminated pads at the component rework as well as neighboring sites will help determine the effectiveness of the rework process.
4. Collateral Heat Damage
There are numerous problems that can arise from the reflow of neighboring underfilled component solder connections; for example, oxidation, de-wetting, pad and lead damage, solder ball formation, wicking, starved solder joints, and component damage are the biggest anomalies post-rework. Depending on the rework heating source, there can be a variety of heat shielding methods employed [2].
5. Proper Profile Development
The rework profile for underfilled PCBs mostly duplicates the original reflow profile. To protect neighboring underfilled components due to the below solder liquidus softening temperature of the underfill means that there will be a slight deviation for this rework profile.
Summary
By concentrating on these five factors, a more repeatable rework process for underfilled PCBs can be developed.
References
1. J. Burke and A.D. Chunsheng, “Laser Rework Process for BGA: A New Method for PCBA Rework Instead of Hot Air/Infrared Heating,” October 2018, SMTAI.
2. A. Gaynor and B. Wettermann, “Shielding Effectiveness of Polyimide Tape During Rework,” October 2014,
Circuits Assembly.
More Columns from Knocking Down the Bone Pile
Knocking Down the Bone Pile: Addressing End-of-life Component Solderability Issues, Part 4Knocking Down the Bone Pile: Tin Whisker Mitigation in Aerospace Applications, Part 3
Knocking Down the Bone Pile: Gold Mitigation for Class 2 Electronics
Knocking Down the Bone Pile: Basics of Component Lead Tinning
Knocking Down the Bone Pile: Package on Package Rework—Skill Required
Knocking Down the Bone Pile: 2023’s Top Challenges in BGA Rework
Knocking Down the Bone Pile: Eliminating Solder Balls in Hand Soldering
Knocking Down the Bone Pile: Opening a Trace on the Surface of a PCB