-
- News
- Books
Featured Books
- smt007 Magazine
Latest Issues
Current IssueSupply Chain Strategies
A successful brand is built on strong customer relationships—anchored by a well-orchestrated supply chain at its core. This month, we look at how managing your supply chain directly influences customer perception.
What's Your Sweet Spot?
Are you in a niche that’s growing or shrinking? Is it time to reassess and refocus? We spotlight companies thriving by redefining or reinforcing their niche. What are their insights?
Moving Forward With Confidence
In this issue, we focus on sales and quoting, workforce training, new IPC leadership in the U.S. and Canada, the effects of tariffs, CFX standards, and much more—all designed to provide perspective as you move through the cloud bank of today's shifting economic market.
- Articles
- Columns
- Links
- Media kit
||| MENU - smt007 Magazine
Estimated reading time: 4 minutes
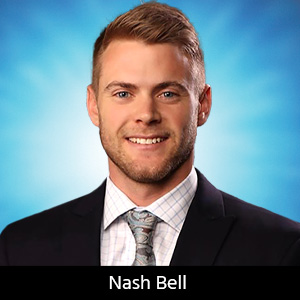
Knocking Down the Bone Pile: Getting to the Root Cause of BGA Assembly Problems
When potential process defects begin showing up underneath BGAs in electronic assemblies, there are numerous failure analysis tests that can be used to troubleshoot process problems. These investigative methods begin with non-destructive test methods and progress to destructive methods as some of the possible root causes are eliminated.
After electrical testing has been performed, there are numerous inspection methodologies spelled out in the IPC-A-610 [1] to use in determining potential assembly defects at BGA locations. These inspection methodologies include visual inspection via a microscope and borescope, as well as X-ray analysis. The first level of BGA failure analysis is visual inspection with the aid of a microscope or borescope. Visual inspection criteria per the IPC A-610 can be found in the SMT portion of the IPC-A-610.
In most cases, BGAs are inspected to see the uniformity of collapse along the outer row of the package, with special attention being paid to the corner locations. This can be done when the view is unobstructed via a microscope. The magnification and lighting will be crucial to seeing the outside row of the BGAs. As long as the flux residue has been cleaned and the conformal coating is not obstructing the viewing area, criteria—such as the uniformity of the ball collapse, the distance between balls, and the distance from balls to any neighboring ungrounded surface—can be seen using visual inspection.
The next level of visual inspection, which may, in some cases, allow for inspection into the third row of the area array device, will be via a borescope. A borescope, borrowed from the medical industry, allows for images to be captured a few rows into the package. This visual inspection tool is especially useful when neighboring components are only a few millimeters from the perimeter of the BGA. Both direct and indirect lighting methods can provide the necessary illumination to capture meaningful solder ball images. The quality of the images obtained depends on the quality of the light, the mirrors used on the end of the endoscope, the lenses, and the quality of the light going to the imaging area. In addition to these visual techniques, X-ray imaging will also help to diagnose and troubleshoot the process being investigated.
Transmissive X-ray imaging is a widely-used non-destructive imaging tool that allows for all of the solder and solder balls to be seen underneath the BGA package. There are numerous anomalies and defects that can be seen through the use of X-ray inspection. X-ray inspection of the entire device field using a wide field of view generally is the beginning point of the BGA X-ray inspection process. This is followed by closer, higher magnification inspection of “areas of interest.”
Shorts and violations of minimum electrical clearance are common problems which can be measured and found using X-ray inspection. More subtle defects also show up on X-ray inspection, such as incomplete or inadequate wetting or head-in-pillow non-coalescing solder joints. Furthermore, measurements of the solder ball diameters and collapse height as well as sphericity, void percentage, and other attributes can be determined via careful X-ray inspection using higher-end X-ray equipment. Destructive testing could augment both the visual and X-ray inspection methods for “no specific defects noted” conditions during either inspection process.
Dye and pry testing [2] is a relatively simple, cost-effective destructive method for testing the integrity of the solder joint on a BGA package. The method does not require any high-end capital equipment instead of relying on generally available investigative or production tools, such as a small vacuum chamber, a bake-out oven, a pry tool, and a microscope. Testing of this type can be outsourced to failure analysis test labs or be done by the user.
The first step is determining the test location. Dye penetrant is squirted underneath the package at the location of interest. Make sure the dye has made its way underneath the suspect device. Place the package in a vacuum chamber to make sure the penetrant flows into cracks in the solder joint or cracks in the pads. Cure the penetrant in a bake-out oven per the dye penetrant manufacturer’s recommendation so as to not smear the dye around the package for a false positive reading due to smearing.
Once the dye is dried and cleaned, the BGA is pried from the board. Areas in and around the ball interface are examined (Figure 1) to see where the dye may indicate an open connection.
Figure 1: Dye penetrant in corners of the BGA package indicating opens in the corner of the package.
The dye penetrant left behind at the solder interface will indicate failures such as pad cratering and solder joint fractures from thermal, mechanical, or drop shock. If no failures are indicated by the dye, then other test methods—such as cross-sectioning, acoustic microscopy, and EDX or SEM analysis—may be the next steps in finding a root cause in the BGA solder joint failure analysis.
References
- IPC-A-610 Acceptability of Electronic Assemblies, section 8.3.12.
- IPC-TM-650 Method 2.4.53 Dye and Pull Test Method.
This column originally appeared in the May issue of SMT007 Magazine.
More Columns from Knocking Down the Bone Pile
Knocking Down the Bone Pile: Addressing End-of-life Component Solderability Issues, Part 4Knocking Down the Bone Pile: Tin Whisker Mitigation in Aerospace Applications, Part 3
Knocking Down the Bone Pile: Gold Mitigation for Class 2 Electronics
Knocking Down the Bone Pile: Basics of Component Lead Tinning
Knocking Down the Bone Pile: Package on Package Rework—Skill Required
Knocking Down the Bone Pile: 2023’s Top Challenges in BGA Rework
Knocking Down the Bone Pile: Eliminating Solder Balls in Hand Soldering
Knocking Down the Bone Pile: Opening a Trace on the Surface of a PCB