-
- News
- Books
Featured Books
- smt007 Magazine
Latest Issues
Current IssueSupply Chain Strategies
A successful brand is built on strong customer relationships—anchored by a well-orchestrated supply chain at its core. This month, we look at how managing your supply chain directly influences customer perception.
What's Your Sweet Spot?
Are you in a niche that’s growing or shrinking? Is it time to reassess and refocus? We spotlight companies thriving by redefining or reinforcing their niche. What are their insights?
Moving Forward With Confidence
In this issue, we focus on sales and quoting, workforce training, new IPC leadership in the U.S. and Canada, the effects of tariffs, CFX standards, and much more—all designed to provide perspective as you move through the cloud bank of today's shifting economic market.
- Articles
- Columns
- Links
- Media kit
||| MENU - smt007 Magazine
Estimated reading time: 4 minutes
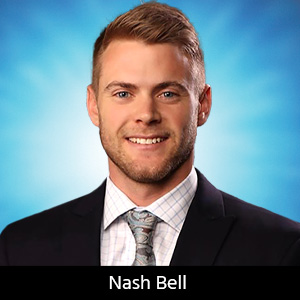
Knocking Down the Bone Pile: Removing Conformal Coatings for PCB Rework
Conformal coatings provide protection for electronic assemblies against moisture, dust, chemicals, and heat in a variety of end-use operating environments. When the removal and replacement of components due to field failures or manufacturing defects need to occur, this overlying coating layer first must be removed before being able to remove and replace a component. The choice of the correct removal method for a specific coating is necessary so as to not damage the PCB or neighboring components.
Incomplete coating removal, such as on the underside of components, can result in pads being ripped off of the board when attempting to remove the component during the rework process. Incomplete removal of the coating may mean that solder can “squirt out” from encapsulated reflowed solder during the rework process, thereby causing bridging. These problems, as well as others, can result from improper conformal coating removal.
There are numerous methods for the removal of conformal coatings from an electronics assembly. The methods and materials used to remove coatings are determined by the coating type, the hardness of the coating, as well as the size of the area requiring removal. The types of removal methods most often employed include chemical stripping, peeling, heating, mechanical abrasion, and laser ablation.
For some coatings, chemical solvents are used to soften up or partially dissolve the coating. The removal agent is either recommended or formulated by the coating manufacturer. Following the manufacturer’s guidance will limit potential board and component damage, though it is always a good idea to test the removal agent on scrap boards. In many cases, the solvent can be selectively applied using a swab, with the surrounding area being masked off. Once the material is softened, the coating can be gently removed using a brush or wooden stick.
In many cases, a neutralizer then needs to be added around the removal area to stop the continuing effects of the solvent. Ionic residues can be left behind on the board if the removal chemistry is not cleaned off thoroughly, thereby affecting the reliability of the assembly. Acrylic conformal coatings are the most sensitive to solvents, hence their easy removal using this technique. Silicone and urethane coatings are the least sensitive to removal solvents. In general, solvent removal techniques for epoxies, as well as parylene, are ineffective.
Some conformal coatings can be removed by simply peeling or scraping them from the PCB and component surfaces. A dental pick, wooden stick, or sharp knife can be used to remove these soft coatings. This mechanical removal method may be used in conjunction with thermal or solvent removal techniques. Care needs to be exercised to make sure components, and the laminate are not damaged during the removal process. This removal technique is often employed when removing soft silicone-based or other flexible conformal coatings.
Another coating removal technique involves using a heat source to soften up or break down the coating. A hot air gun or soldering iron is usually employed as the heat source. After softening the coating, it can be removed by the application of gentle pressure with a dental tool or wooden stick. This removal method can work well with most types of conformal coating. Applying heat requires extreme care not to damage the underlying laminate or neighboring components. Acrylic, epoxy, and silicone coatings can be removed using this technique.
Microabraision coating removal uses a variety of soft abrasives accelerated through a small inert gas-propelled nozzle to break down the conformal coating. Walnut shells, glass, plastic beads, and various powder mixtures are propelled to the surface to chip away at the coating. The air pressure, hardness of the removal media, and nozzle diameter all have an impact on the efficacy of this removal process. An ionized air source is typically used to neutralize the static charge generated during this process. Proper masking of the board around the coating removal area protects the board and components. Typical conformal coatings where this process is used as a removal method include parylene, urethane, and epoxy-based coatings.
Laser sources are used in cases where precision conformal coating removal is required. The pulsed energy density of the laser gradually removes or ablates the coating material. A laser source with the correct energy level, frequency, and number of laser source passes needs to be established so that it only ablates the coating and does not damage the underlying or surrounding materials. Laser areas as small as a few microns can be selectively ablated. Parylene coatings can be removed in this manner.
Visual inspection determines if the conformal coating has been removed in the proper area. While there are analytical methods for determining whether the coating has been entirely removed, the UV tracer material as part of the coating formulation allows the coating to show up visibly under “black” lighting.
The removal of conformal coating in preparation for rework and repair on a PCB requires care as incidental damage to the laminate and components can occur during the process. The choice of method requires careful consideration, experience, and operator skill.
Further Reading
- IPC-HDBK-830: Conformal Coating Handbook Guidelines for Design, Selection, and Application of Conformal Coatings.
- IPC-7711/IPC-7721: Rework, Modification, and Repair of Electronic Assemblies.
- G. Caswell, “Coatings and Pottings: Issues and Challenges,” IMAPS, May 2014.
This column originally appeared in the July 2020 issue of SMT007 Magazine.
More Columns from Knocking Down the Bone Pile
Knocking Down the Bone Pile: Addressing End-of-life Component Solderability Issues, Part 4Knocking Down the Bone Pile: Tin Whisker Mitigation in Aerospace Applications, Part 3
Knocking Down the Bone Pile: Gold Mitigation for Class 2 Electronics
Knocking Down the Bone Pile: Basics of Component Lead Tinning
Knocking Down the Bone Pile: Package on Package Rework—Skill Required
Knocking Down the Bone Pile: 2023’s Top Challenges in BGA Rework
Knocking Down the Bone Pile: Eliminating Solder Balls in Hand Soldering
Knocking Down the Bone Pile: Opening a Trace on the Surface of a PCB