-
- News
- Books
Featured Books
- design007 Magazine
Latest Issues
Current IssueProper Floor Planning
Floor planning decisions can make or break performance, manufacturability, and timelines. This month’s contributors weigh in with their best practices for proper floor planning and specific strategies to get it right.
Showing Some Constraint
A strong design constraint strategy carefully balances a wide range of electrical and manufacturing trade-offs. This month, we explore the key requirements, common challenges, and best practices behind building an effective constraint strategy.
All About That Route
Most designers favor manual routing, but today's interactive autorouters may be changing designers' minds by allowing users more direct control. In this issue, our expert contributors discuss a variety of manual and autorouting strategies.
- Articles
- Columns
- Links
- Media kit
||| MENU - design007 Magazine
Estimated reading time: 3 minutes
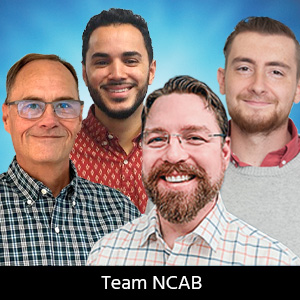
Fresh PCB Concepts: Automotive Standard Elevates the Excellence of Electronics
Soon, we will be heading to sunny San Diego and IPC APEX EXPO again to meet old friends, make new connections, indulge in interesting discussions, and, of course, talk for hours and hours about the importance and development of IPC standards, especially those related to automotive.
IPC-6012DA-WAM1, Automotive Applications Addendum to IPC-6012D, was the first document in IPC’s Automotive Initiative. Further standards are in the pipeline and, more or less, challenge each other to be the next in line, such as the joint document IPC-A-610/IPC J-STD-001 Automotive Addendum that will cover both requirements and acceptability of electronic assemblies. Then, we have IPC-9797, which is a brand-new cold joining press-fit standard for harsh environments. Finally, and also running the race to reach a release within IPC APEX EXPO 2020, we have IPC-1782A—the traceability standard, that, if you ask me, links all other standards seamlessly together.
IPC-6012DA (currently in WAM1) was the first automotive standard for printed boards; it also needs to expand to cover all types of rigid printed boards. To meet the PCB needs in the automotive industry of today and tomorrow, we have started to collect information and identify the types of printed boards not covered by the existing standard. One finding in the research is printed boards used for LED headlights and taillights, which have two requirements not covered; these are described as metal-core printed boards and high-power printed boards.
Metal-core Printed Boards
IPC started to develop a standard 4–5 years ago, but the work to develop this standard was stopped halfway. The result is that it’s a jungle out there, especially the specification and standardization of aluminum used as a base material and heat distributor. The situation today is that the major players in the market develop their own materials without a material standard. That does not mean the materials are of low quality. The challenge comes when you try to compare materials from two competitive vendors.
You can sort on thermal conductivity and other parameters for the insulation material, but if you try to specify the aluminum carrier, you soon get stuck. If you ask the big vendors, you surely get figures, but how to compare if you don’t have a standard for reference? A good example is to know how to select the correct material if you have a long, slim printed board and want to avoid bow and twist.
High-voltage Printed Boards
Along with the metal-core printed boards comes the requirements for high voltage for LED headlights and taillights. We see voltage of 1000 volts or more with all the requirements that follow this level. For printed boards used in such applications, test and qualification will be discussed along with material and electrical requirements.
Traceability
IPC-1782A is currently in the ballot stage, and we have finally managed to include traceability for printed boards in addition to the electronic production. Traceability is a critical tool to limit the cost when a problem occurs, and with the volumes of automotive applications, it is vital to keep the cost down. The new revision of Automotive Applications Addendum to IPC-6012 will be linked to IPC-1782A with a requirement to traceability levels related to reliability requirements.
Press-fit Technology
IPC-6012DA WAM1 already has requirements related to press-fit, but with the new cold-joining press-fit standard IPC-9797, we will have a much better tool to set requirements using a well-defined standard. These are some of the issues that will be discussed when we start developing the new revision of the Automotive Applications Addendum to IPC-6012. Again, some of the issues have up to now not been sufficiently discussed. I think we are overdue but, hopefully, not too late.
Join the Group and Raise Your Voice
The first open discussion will be at IPC APEX EXPO on February 4. The task group is open for new members, and with this agenda, I expect an increased interest in this standard. We need members from the whole supply chain to join the discussion, from automotive application designers to all parts of electronics production and carmakers. Printed boards for electric vehicles will also be a part of the whole discussion.
Be a Cheerleader
Since six PCB manufacturers came together to create the Institute of Printed Circuits (IPC) in the fall of 1957, hundreds of standards have been developed, obstacles removed, and the advancement of the PCB industry has been cheered forward. I am looking forward and hoping to see lots of cheering and enthusiasm at this year’s grand event in San Diego as well. We all need the standards and to be involved in making them function optimally.
This column originally appeared in the January 2020 issue of PCB007 Magazine.
More Columns from Fresh PCB Concepts
Fresh PCB Concepts: Designing for Success at the Rigid-flex Transition AreaFresh PCB Concepts: More Than Compliance—A Human-centered Sustainability Approach
Fresh PCB Concepts: Assembly Challenges with Micro Components and Standard Solder Mask Practices
Fresh PCB Concepts: The Power of a Lunch & Learn for PCB Professionals
Fresh PCB Concepts: Key Considerations for Reliability, Performance, and Compliance in PCBs
Fresh PCB Concepts: Traceability in PCB Design
Fresh PCB Concepts: Tariffs and the Importance of a Diverse Supply Chain
Fresh PCB Concepts: PCB Stackup Strategies—Minimizing Crosstalk and EMI for Signal Integrity