-
- News
- Books
Featured Books
- smt007 Magazine
Latest Issues
Current IssueWhat's Your Sweet Spot?
Are you in a niche that’s growing or shrinking? Is it time to reassess and refocus? We spotlight companies thriving by redefining or reinforcing their niche. What are their insights?
Moving Forward With Confidence
In this issue, we focus on sales and quoting, workforce training, new IPC leadership in the U.S. and Canada, the effects of tariffs, CFX standards, and much more—all designed to provide perspective as you move through the cloud bank of today's shifting economic market.
Intelligent Test and Inspection
Are you ready to explore the cutting-edge advancements shaping the electronics manufacturing industry? The May 2025 issue of SMT007 Magazine is packed with insights, innovations, and expert perspectives that you won’t want to miss.
- Articles
- Columns
- Links
- Media kit
||| MENU - smt007 Magazine
Real Time with…SMTAI 2020: KYZEN on How Maximized Stencil Life Improves Yields
September 16, 2020 | Real Time with...SMTAIEstimated reading time: 7 minutes
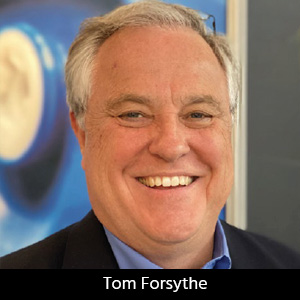
KYZEN Executive Vice President Tom Forsythe shares company updates on stencil cleaning with Nolan Johnson. KYZEN recently announced its newest stencil cleaning product—KYZEN E5631. Forsythe details how the product is best used, as well as the benefits it brings to maximizing stencil life and improving manufacturing yields.
View more videos and show-related content at Real Time with… SMTAI 2020 virtual.
I-Connect007 continues to deliver original reporting and coverage of the electronics design, electronics manufacturing, and contract manufacturing industries, including up-to-date information from the companies, associations, and supply chains globally. Find the latest news and information at I-Connect007.com.
Audio Transcript:
Nolan Johnson: Hi. Nolan Johnson here, virtually doing a video interview for Real Time with…SMTAI. And I’m talking virtually with Tom Forsythe from KYZEN. Tom, glad to have you here.
Tom Forsythe: Good to be here. Thank you so much.
Johnson: We’re here in the virtual ether sense, but we’re still talking about supporting a show. We’re talking about supporting SMTAI and some of the work that KYZEN has been doing and announcing during the show. What do you have on stage for everybody?
Forsythe: Of course, KYZEN is the cleaning people, cleaning materials for the electronics industry. And we have a broad range of materials. Last year, we introduced our Aquanox 4727. That’s going very well in the marketplace. This year, we’re talking about a new stencil cleaning product because stencil cleaning touches all the users in the industry. Everybody who’s doing assemblies, at some point, whether they’re doing it with a handkerchief or a more sophisticated process, has to clean up their stencils, so they get a good print. The old adage that I don’t know that anybody has ever proven, but no one has denied that well over 50% of the problems in assembly all go back to the printer, which comes back to the print and often lays at the foot of that whole print-stencil interface.
Johnson: That’s a pretty critical place to be then.
Forsythe: Absolutely. It’s not someplace that everyone focuses on. Stencil cleaning is whatever is worse than being a redheaded stepchild—I think maybe the cousin of a redheaded stepchild, or something like that. And that’s why a lot of the products that are used in that space are decades old. It’s not uncommon for that because there hasn’t been a lot of scrutiny. We’ve done a lot of research over the last number of years, digging into this, constantly moving the ball. And our new product, KYZEN E5631 really answers the mail on that from economics, health and safety, as well as utility, being able to be used under the screen on the printer and offline, and a stencil cleaner for that more periodic robust cleaning.
Johnson: For those who aren’t that familiar with stencil cleaning and the process, walk us through how you use the product and where it hits.
Forsythe: There are really two different ways that stencil cleaning happens. The easier way, or the least impactful way, is on the printer itself. Most of the medium- to high-end printers now come with a cleaning mechanism on it. That mechanism usually has three potential capabilities. There’s the under-screen roll, the little wiper thing that people are familiar with. There’s often a vacuum assist that sometimes is used, or not, to help kind of vacuum off the material. And there’s the solvent—some kind of solvent—that goes on there that actually does the cleaning part because we all know solder paste isn’t exactly like crumbs on the kitchen table.
Solder paste is gooey and has a lot of viscousness to it, and if you’re just pushing it around with a dry towel, that’s going to cause a problem downstream. You use that solvent material or aqueous material, in this case, to wipe that off—to get it off—and then you wipe it with the towel. That’s the one that many people are familiar with—that onscreen thing. And people do that every so many cycles or prints. The spaceship people do it after every print or darn near. And obviously, if they’re making consumer products, it’s after a whole lot of prints, and that’s more of kind of a local decision.
The other mode that stencil cleaning happens in is the periodic cleaning where that wiping and whatnot is all well and good. But after a while, you need to kind of do heavy-duty cleaning, get into the crevices and corners very effectively. Stencils get swapped out with little or no downtime doing that. And we take that stencil and put it into an offline stencil cleaning machine. A number of people make those. We’re not in the equipment business; we don’t do that.
Our material goes into the machine, and then you have a normal wash, rinse, and dry. Typically, it’s in a one chamber type of thing. It’s not conveyorized or anything like that. But they’re often designed and purpose-built for it. The stencils are roundabout three-foot squared—not quite—but only a couple inches thick. Stencil cleaners often look like toasters in that they have slots on the side or on top or skinny doors that the stencils just slide in, the door closes, and it runs its process.
One of the advantages of the E5631 is that it’s designed to be used in both of those applications. It can be used under the screen or in the offline stencil cleaning at economical concentrations—anywhere from 10 to 25%. It depends on the soil you’re cleaning, and—in some cases—how long it has been. If you’ve left it on the printer for 1,000 cycles, which is a vast overstatement, it might take a little longer to clean, and it might take a slightly higher concentrate.
Johnson: Is there an advantage to using one cleaning solution in both applications?
Forsythe: It’s just simplicity. If I’m cleaning stencils, I’m using product A, or in our case, product E5631, rather than having two different materials with two different stock numbers, two different things to run out of, and two different things that can—if somebody’s new—mix up and put the wrong one in the wrong machine. Most quality shops wouldn’t encounter any of those problems, but eliminating the potential for them is a fundamental positive.Page 1 of 2
Suggested Items
Driving Innovation: Direct Imaging vs. Conventional Exposure
07/01/2025 | Simon Khesin -- Column: Driving InnovationMy first camera used Kodak film. I even experimented with developing photos in the bathroom, though I usually dropped the film off at a Kodak center and received the prints two weeks later, only to discover that some images were out of focus or poorly framed. Today, every smartphone contains a high-quality camera capable of producing stunning images instantly.
Hands-On Demos Now Available for Apollo Seiko’s EF and AF Selective Soldering Lines
06/30/2025 | Apollo SeikoApollo Seiko, a leading innovator in soldering technology, is excited to spotlight its expanded lineup of EF and AF Series Selective Soldering Systems, now available for live demonstrations in its newly dedicated demo room.
Indium Corporation Expert to Present on Automotive and Industrial Solder Bonding Solutions at Global Electronics Association Workshop
06/26/2025 | IndiumIndium Corporation Principal Engineer, Advanced Materials, Andy Mackie, Ph.D., MSc, will deliver a technical presentation on innovative solder bonding solutions for automotive and industrial applications at the Global Electronics A
Fresh PCB Concepts: Assembly Challenges with Micro Components and Standard Solder Mask Practices
06/26/2025 | Team NCAB -- Column: Fresh PCB ConceptsMicro components have redefined what is possible in PCB design. With package sizes like 01005 and 0201 becoming more common in high-density layouts, designers are now expected to pack more performance into smaller spaces than ever before. While these advancements support miniaturization and functionality, they introduce new assembly challenges, particularly with traditional solder mask and legend application processes.
Knocking Down the Bone Pile: Tin Whisker Mitigation in Aerospace Applications, Part 3
06/25/2025 | Nash Bell -- Column: Knocking Down the Bone PileTin whiskers are slender, hair-like metallic growths that can develop on the surface of tin-plated electronic components. Typically measuring a few micrometers in diameter and growing several millimeters in length, they form through an electrochemical process influenced by environmental factors such as temperature variations, mechanical or compressive stress, and the aging of solder alloys.