-
- News
- Books
Featured Books
- design007 Magazine
Latest Issues
Current IssueProper Floor Planning
Floor planning decisions can make or break performance, manufacturability, and timelines. This month’s contributors weigh in with their best practices for proper floor planning and specific strategies to get it right.
Showing Some Constraint
A strong design constraint strategy carefully balances a wide range of electrical and manufacturing trade-offs. This month, we explore the key requirements, common challenges, and best practices behind building an effective constraint strategy.
All About That Route
Most designers favor manual routing, but today's interactive autorouters may be changing designers' minds by allowing users more direct control. In this issue, our expert contributors discuss a variety of manual and autorouting strategies.
- Articles
- Columns
- Links
- Media kit
||| MENU - design007 Magazine
Estimated reading time: 3 minutes
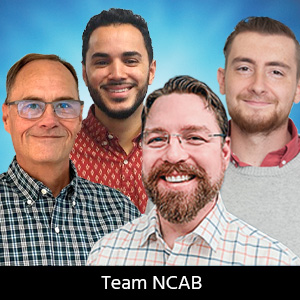
Fresh PCB Concepts: Advantages of Application-Engineered PCBs
When working with your PCB supplier, do you have a dedicated engineering resource to help with the design of your PCB before fabrication? How about a resource that has experience and knowledge about the different applications for PCBs? This is one of the most important and valuable factors when producing high-reliability PCBs.
First, let’s discuss how field application engineers (FAEs) could be this resource. An experienced FAE will have experience with many PCBs for a variety of applications and have the capability and knowledge to recommend the best design practices, materials, etc. It’s best to have your PCB supplier involved as early as possible in the design phase. Approximately 50–60% of the cost is built in the design before we even see it.
Each time we receive a new PCB design, one of our FAEs will thoroughly inspect the design and all fabrication notes. During the engineering process, we apply specific demands to benefit the application. Maybe it’s a down-hole PCB, and the customer asks for FR-4 material. Typically, we expect to see a rigid polyimide material compliant to IPC-4101/41, which is intended for the high heat and harsh environment seen in this application. We first check if the material is correct. If it’s not, then we would ask our customer for confirmation the material requested is not intended for the application.
The same goes for other applications as well. Maybe it’s a high-speed application, and the customer chose ENIG for a surface finish when we would usually recommend immersion silver. For example, we recently had a customer design a PCB to go into a thermometer, and the customer asked for low-temperature FR-4. We recommended a higher-grade material so that it can withstand a higher temperature. The customer was unaware of this, and it really saved them in producing the final product reliably and for volume production.
Even if it’s a new application for you, a knowledgeable FAE will have familiarity and experience with various applications and be able to share this knowledge with you. There are unique demands for each application, such as:
- Telecommunications
- Automotive
- IoT
- Optical
- Industrial
- Medical
- High-speed
- Aerospace
Did you know that when producing PCBs for automotive applications, you must follow the IATF-13949 standard? Or with medical applications, ISO 13485 requirements must be implemented? This is knowledge your PCB producer should be able to share with you.
There are many other factors to consider, too. When we receive a PCB design, consider the following data:
- 30% are not optimized for volume
- 30% will have a mechanical problem
- 50% do not know which factory to use
- 70% do not know the unit cost of the PCB in volume
- 30% have design errors
FAEs will implement a variety of steps to ensure seamless production by utilizing design for excellence (DFX) techniques. DFX goes beyond the traditional design for manufacturing (DFM) review and looks at all the factors from DFM through design for assembly (DFA). The value of DFX is reflected in the design phase to anticipate and solve future production problems. The later we find it, then the larger problems, the greater the cost to solve, and the longer the production cycle. The benefits of working with an FAE early on include a faster time to market, responsibility from design to volume production, and early identification of cost drivers and project risk. Sustainability is also a factor, as there will be less product waste.
My advice to any PCB designer is always to involve your PCB supplier, and the earlier, the better. And if your PCB supplier isn’t providing this type of support, I would be cautious about continuing to work with them. Application experts not only have in-depth knowledge of these applications but also an established record of success in supporting multiple types of technology in each application. Whether it’s your first flex-rigid design for a telecom application or an IMS for a power supply, consider having an FAE assist with your next project.
Jeffrey Beauchamp is a field application engineer at NCAB Group.
More Columns from Fresh PCB Concepts
Fresh PCB Concepts: Designing for Success at the Rigid-flex Transition AreaFresh PCB Concepts: More Than Compliance—A Human-centered Sustainability Approach
Fresh PCB Concepts: Assembly Challenges with Micro Components and Standard Solder Mask Practices
Fresh PCB Concepts: The Power of a Lunch & Learn for PCB Professionals
Fresh PCB Concepts: Key Considerations for Reliability, Performance, and Compliance in PCBs
Fresh PCB Concepts: Traceability in PCB Design
Fresh PCB Concepts: Tariffs and the Importance of a Diverse Supply Chain
Fresh PCB Concepts: PCB Stackup Strategies—Minimizing Crosstalk and EMI for Signal Integrity