-
-
News
News Highlights
- Books
Featured Books
- design007 Magazine
Latest Issues
Current IssueAll About That Route
Most designers favor manual routing, but today's interactive autorouters may be changing designers' minds by allowing users more direct control. In this issue, our expert contributors discuss a variety of manual and autorouting strategies.
Creating the Ideal Data Package
Why is it so difficult to create the ideal data package? Many of these simple errors can be alleviated by paying attention to detail—and knowing what issues to look out for. So, this month, our experts weigh in on the best practices for creating the ideal design data package for your design.
Designing Through the Noise
Our experts discuss the constantly evolving world of RF design, including the many tradeoffs, material considerations, and design tips and techniques that designers and design engineers need to know to succeed in this high-frequency realm.
- Articles
- Columns
- Links
- Media kit
||| MENU - design007 Magazine
Real Time with… AltiumLive Europe 2020: Eric Bogatin’s ‘Unlearning’ Keynote
October 27, 2020 | Pete Starkey, I-Connect007Estimated reading time: 5 minutes
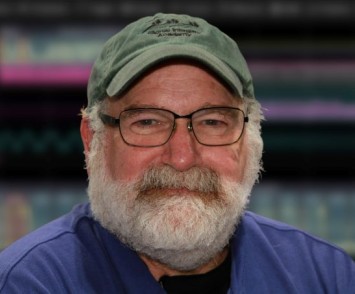
I admit to not being a Star Wars freak, but I am impressed by Yoda’s iconic wisdom and philosophy and intrigued by his advice that, “You must unlearn what you have learned.” Attending Dr. Eric Bogatin’s keynote at the AltiumLive Europe 2020 Virtual Summit was an enlightening experience and left me in no doubt of Dr. Bogatin’s iconic status in our industry. I was fascinated not only by his technical knowledge of signal integrity but also by his unique lateral-thinking approach both to managing it and teaching it.
Dr. Bogatin considered that Yoda’s advice applied just as well to some aspects of circuit board design as it did to mastering the Force. There were many myths and myth-conceptions about the best design practices for circuit board layout, which were “legacy code”—inherited practices based on older technologies that had been superseded by newer versions.
“It is time to rethink legacy code,” Dr. Bogatin declared. “The notions we have been carrying a round for many years may no longer be the best recommendations to follow,” as he listed a series of examples: the myth of three capacitor values, the myth of copper pour, the myth of split ground planes, the myth of power planes, the myth that stripline traces don’t radiate, the myth of ferrites on power rails, the myth of ninety-degree bends, and the myth of matched-length traces. He chose to discuss in detail the first two myth-conceptions on this list in the context of power integrity and signal integrity.
“Once connectivity is established, interconnects just screw things up!” The connectivity of a PCB was basically a netlist defined in the schematic and told nothing about the actual performance of the interconnects. The schematic portrayed them as ideal conductors. It was not until the schematic was turned into a physical layout that the effects of the interconnects became apparent; unfortunately, the only thing they could do was screw things up. They could never add performance to the system—only noise. One of his students had commented that “interconnects suck” and that the mission of the designer was to “make them suck less.”
He looked at two aspects of how interconnects could screw-up system performance and what could be done to “minimise how much they sucked.” His first example was power integrity, which encompassed at least 12 different problems. He chose one to explore: switching noise on the power rail, which occurred when the system changed state and illustrated the effect with a simple schematic of a voltage regulator module. When the schematic interconnects became physical conductors on a circuit board, those conductors added inductance as the inputs/outputs were switching, causing switching noise. The inductance could be reduced by using decoupling capacitors.
An alternative to simulation was to build a physical model and measure it. Dr. Bogatin showed a simple example to illustrate where to place the decoupling capacitor, demonstrate how it worked, and measure the effect of different values and positions, with the objective of minimising the residual loop inductance to the device and hence minimising the switching noise. How do you choose the decoupling capacitor? His advice was to select it on the basis of how much it could reduce inductance.
“If the goal is to provide low loop inductance, use small physical size capacitors because they have low loop inductance at high frequency.” Popular design guidelines recommended that when adding decoupling capacitors to the pads of an IC, three different values should be used in parallel: a 0.1-microfarad, a 1.0-microfarad, and a 10-microfarad, with the small one to give low loop inductance and the largest to give sufficient charge storage capacity.
But this concept belonged to the days of through-hole components and did not necessarily apply to SMT. The present reality was that high-frequency impedance was not about capacitance but about lead inductance and a high-frequency capacitor simply had low loop inductance. In the case of surface-mounted capacitors, his examples of 0.1-, 1.0-, and 10-microfarad components all had the same body size and no leads; therefore, they all had the same loop inductance.
The amount of capacitance was not about body size or loop inductance. The quality of a capacitor was solely about the loop inductance it contained when it was mounted into the board and not about the amount of capacitance. With surface-mount capacitors, it was absolutely not true that three different capacitors were needed because the 10-microfarad capacitor, if chosen correctly, could have just as low a loop inductance as the 0.1-microfarad capacitor. Low loop inductance was the key feature being designing for, with as much capacitance as possible within the chosen body size. Multiple capacitors could be used if necessary as long as they were large enough to damp-out parallel resonances, but there was absolutely no need to use three different values. That was legacy code, although he still saw many examples in current designs.
Dr. Bogatin’s second topic related to the common practice of copper-pouring on signal layers after routing all the signal lines and connecting the copper pour to the ground net in the belief that it would result in lower crosstalk or less electromagnetic interference. He demonstrated why it was not a good thing to do and gave simulated examples of the consequences by measuring the crosstalk between widely-spaced transmission lines. The first example had no copper pour between the lines. The second had a full copper pour, electrically floating, the third had a full copper pour tied to earth with a series of closely spaced via holes.
With no copper between the lines, there was very slight crosstalk. Floating copper between the lines made it slightly worse. Grounding the copper gave very slightly less crosstalk, but the differences were minimal. Changing to a signal with a shorter rise time, there came a point where it matched the resonant frequency of the floating copper and greatly increased the crosstalk compared with the no-copper example.
The grounded copper again gave a minimal reduction in crosstalk. And that was with a high density of grounding vias. If the number of vias was reduced, the crosstalk approached that of the floating-copper example. All this demonstrated that copper fill was not solving a crosstalk problem but potentially creating one. Legacy code again! “It’s never too late to rethink legacy code and unlearn what we have learned.”
Dr. Bogatin remains iconic in the electronics design community as a leading technical authority and a wise mentor. His teaching skill strikes a balance between over-simplification “signal integrity for tiny tots” and over-complication “blinding you with science.”
And, by the way, another famous quote from Yoda is, “Always pass on what you have learned.”
Suggested Items
The Evolution of Picosecond Laser Drilling
06/19/2025 | Marcy LaRont, PCB007 MagazineIs it hard to imagine a single laser pulse reduced not only from nanoseconds to picoseconds in its pulse duration, but even to femtoseconds? Well, buckle up because it seems we are there. In this interview, Dr. Stefan Rung, technical director of laser machines at Schmoll Maschinen GmbH, traces the technology trajectory of the laser drill from the CO2 laser to cutting-edge picosecond and hybrid laser drilling systems, highlighting the benefits and limitations of each method, and demonstrating how laser innovations are shaping the future of PCB fabrication.
Day 2: More Cutting-edge Insights at the EIPC Summer Conference
06/18/2025 | Pete Starkey, I-Connect007The European Institute for the PCB Community (EIPC) summer conference took place this year in Edinburgh, Scotland, June 3-4. This is the third of three articles on the conference. The other two cover Day 1’s sessions and the opening keynote speech. Below is a recap of the second day’s sessions.
Day 1: Cutting Edge Insights at the EIPC Summer Conference
06/17/2025 | Pete Starkey, I-Connect007The European Institute for the PCB Community (EIPC) Summer Conference took place this year in Edinburgh, Scotland, June 3-4. This is the second of three articles on the conference. The other two cover the keynote speeches and Day 2 of the technical conference. Below is a recap of the first day’s sessions.
Preventing Surface Prep Defects and Ensuring Reliability
06/10/2025 | Marcy LaRont, PCB007 MagazineIn printed circuit board (PCB) fabrication, surface preparation is a critical process that ensures strong adhesion, reliable plating, and long-term product performance. Without proper surface treatment, manufacturers may encounter defects such as delamination, poor solder mask adhesion, and plating failures. This article examines key surface preparation techniques, common defects resulting from improper processes, and real-world case studies that illustrate best practices.
RF PCB Design Tips and Tricks
05/08/2025 | Cherie Litson, EPTAC MIT CID/CID+There are many great books, videos, and information online about designing PCBs for RF circuits. A few of my favorite RF sources are Hans Rosenberg, Stephen Chavez, and Rick Hartley, but there are many more. These PCB design engineers have a very good perspective on what it takes to take an RF design from schematic concept to PCB layout.