-
- News
- Books
Featured Books
- pcb007 Magazine
Latest Issues
Current IssueInventing the Future with SEL
Two years after launching its state-of-the-art PCB facility, SEL shares lessons in vision, execution, and innovation, plus insights from industry icons and technology leaders shaping the future of PCB fabrication.
Sales: From Pitch to PO
From the first cold call to finally receiving that first purchase order, the July PCB007 Magazine breaks down some critical parts of the sales stack. To up your sales game, read on!
The Hole Truth: Via Integrity in an HDI World
From the drilled hole to registration across multiple sequential lamination cycles, to the quality of your copper plating, via reliability in an HDI world is becoming an ever-greater challenge. This month we look at “The Hole Truth,” from creating the “perfect” via to how you can assure via quality and reliability, the first time, every time.
- Articles
- Columns
- Links
- Media kit
||| MENU - pcb007 Magazine
Plasmatreat Releases Surface Cleaning for a Reliable Wire Bonding Process
October 28, 2020 | PlasmatreatEstimated reading time: 3 minutes
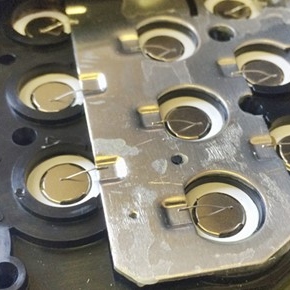
Openair-Plasma from Plasmatreat GmbH is one of the leading technologies worldwide to activate and clean surfaces. It is used in numerous applications to pretreat different substrates. It can also be used to clean metal surfaces for solid wire bonding. The Openair-Plasma technology is a cost-efficient process and can be integrated inline, allowing the bonding process to take place directly after the cleaning is completed.
"Metal can be cleaned using three processes which have different effects and have different treatment goals," says Nico Coenen, Global Business Development Manager Electronics Market of Plasmatreat GmbH, explaining the basic possibilities of plasma treatment. The first process, neutralization, involves the removal of both surface charge and statically bound dirt such as dust particles. This is done by the charge carriers of the Openair-Plasma treatment. In the second process, the volatile components such as moisture and VOCs (volatile organic compounds) are eliminated by evaporation through the thermal effect of the Openair-Plasma treatment. The final cleaning process is removing organic contaminants. The reactive nature of Openair-Plasma causes hydrocarbon chains to be broken down and split into smaller, volatile molecules (up to H2O and CO2).
The successful treatment can be verified, for example, by using an atomic force microscope, which provides visual evidence of the change in the surface. This is a special scanning probe microscope which is used in surface chemistry for mechanical scanning of surfaces and for measuring atomic forces on the nanometer scale. Furthermore, the contact angle method can be used to prove the modified surface tension e.g. by a drop of water. The water drop on the plasma-treated surface changes its wetting properties in such a way that the contact angle and height are reduced and the surface is becoming more hydrophilic.
This is the result of surface cleaning with Openair-Plasma. Especially oxide surfaces, but also contamination caused by bleed out, interfere with the bonding process and prevent reliable connections. Openair-Plasma removes both surface contamination and the oxide layer and the clean surface of the metal alloy is revealed. This is beneficial, in semiconductor applications as particularly clean surfaces are required here in order to reliably bond the ultra-fine wires. The plasma-treated surface allows bonded materials to form a more stable and larger-area connection.
A similar process is used to remove copper oxides, especially in semiconductor and LED applications. By using X-ray photoelectron spectroscopy, the chemical composition of solids and their surface can be determined without causing damage. After treating copper, it can therefore be determined that the surface proportion of copper increases from 3% to 38%, with a concomitant reduction in the carbon content from 43% to 18%. "These changes clearly show that the copper oxide has been reduced and the copper surface area increased," says Coenen. The contact angle analysis also shows a comparable result. Bond wires therefore also form reliable connections here.
In addition to aluminum and copper substrates, nickel surfaces show similarly good properties after being treated with Openair-Plasma. This is particularly important in battery production. Since nickel oxide acts like a barrier layer, which massively complicates the connection with other materials, the cleaning of the nickel surface from oxides is essential. Plasmatreat has therefore developed a special jet for this application that matches the general requirements and at the same time meets the temperature requirements of the process step, for example does not exceed the limit of 50° Celsius.
"The degree to which the individual substrates allow stable wire bonding depends on the material in use. However, the upstream plasma surface treatment improves the application window of the wire bonding process in any case. Both wettability and adhesion are optimized," says Coenen.
Testimonial
"We’re proud to call I-Connect007 a trusted partner. Their innovative approach and industry insight made our podcast collaboration a success by connecting us with the right audience and delivering real results."
Julia McCaffrey - NCAB GroupSuggested Items
Trouble in Your Tank: Minimizing Small-via Defects for High-reliability PCBs
08/27/2025 | Michael Carano -- Column: Trouble in Your TankTo quote the comedian Stephen Wright, “If at first you don’t succeed, then skydiving is not for you.” That can be the battle cry when you find that only small-diameter vias are exhibiting voids. Why are small holes more prone to voids than larger vias when processed through electroless copper? There are several reasons.
The Government Circuit: Navigating New Trade Headwinds and New Partnerships
08/25/2025 | Chris Mitchell -- Column: The Government CircuitAs global trade winds continue to howl, the electronics manufacturing industry finds itself at a critical juncture. After months of warnings, the U.S. Government has implemented a broad array of tariff increases, with fresh duties hitting copper-based products, semiconductors, and imports from many nations. On the positive side, tentative trade agreements with Europe, China, Japan, and other nations are providing at least some clarity and counterbalance.
How Good Design Enables Sustainable PCBs
08/21/2025 | Gerry Partida, Summit InterconnectSustainability has become a key focus for PCB companies seeking to reduce waste, conserve energy, and optimize resources. While many discussions on sustainability center around materials or energy-efficient processes, PCB design is an often overlooked factor that lies at the heart of manufacturing. Good design practices, especially those based on established IPC standards, play a central role in enabling sustainable PCB production. By ensuring designs are manufacturable and reliable, engineers can significantly reduce the environmental impact of their products.
50% Copper Tariffs, 100% Chip Uncertainty, and a Truce
08/19/2025 | Andy Shaughnessy, I-Connect007If you’re like me, tariffs were not on your radar screen until a few months ago, but now political rhetoric has turned to presidential action. Tariffs are front-page news with major developments coming directly from the Oval Office. These are not typical times. President Donald Trump campaigned on tariff reform, and he’s now busy revamping America’s tariff policy.
Global PCB Connections: Understanding the General Fabrication Process—A Designer’s Hidden Advantage
08/14/2025 | Markus Voeltz -- Column: Global PCB ConnectionsDesigners don’t need to become fabricators, but understanding the basics of PCB fabrication can save you time, money, and frustration. The more you understand what’s happening on the shop floor, the better you’ll be able to prevent downstream issues. As you move into more advanced designs like HDI, flex circuits, stacked vias, and embedded components, this foundational knowledge becomes even more critical. Remember: the fabricator is your partner.