-
- News
- Books
Featured Books
- smt007 Magazine
Latest Issues
Current IssueWhat's Your Sweet Spot?
Are you in a niche that’s growing or shrinking? Is it time to reassess and refocus? We spotlight companies thriving by redefining or reinforcing their niche. What are their insights?
Moving Forward With Confidence
In this issue, we focus on sales and quoting, workforce training, new IPC leadership in the U.S. and Canada, the effects of tariffs, CFX standards, and much more—all designed to provide perspective as you move through the cloud bank of today's shifting economic market.
Intelligent Test and Inspection
Are you ready to explore the cutting-edge advancements shaping the electronics manufacturing industry? The May 2025 issue of SMT007 Magazine is packed with insights, innovations, and expert perspectives that you won’t want to miss.
- Articles
- Columns
- Links
- Media kit
||| MENU - smt007 Magazine
Real Time with… Altium Live Europe 2020: Rick Hartley’s Secrets of PCB Optimization
October 29, 2020 | Pete Starkey, I-Connect007Estimated reading time: 4 minutes
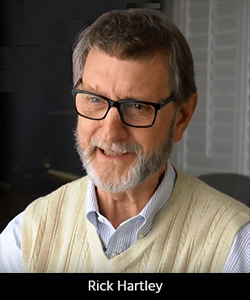
As Lawrence Romine said in his introduction, “There’s that moment when you sit in the crowd and hear Mr. Rick Hartley speak that you know you’ve arrived in PCB design.” With 50 years in the industry focused on circuit and PCB design—and as a specialist in EMI, noise, and signal integrity issues—Rick Hartley was invited to talk about PCB optimisation. But meaning what? There were a lot of things that could be optimised on a PCB.
In this particular case, Hartley was going to talk about designing boards to optimise manufacturability, with particular regard to cost-effective fabrication. I was eager to hear what he had to say, particularly having been for many years a fabricator myself, with much of my time spent talking to designers. The ones I liked best asked all the what-if questions before they began a new design. The ones who caused the most annoyance belonged to the “over-the-wall” category. It gave me enormous satisfaction to arrange for them to visit our factory then surprise them with an invitation to help manufacture what they had designed. They would say, “I never knew it was that complicated.”
Hartley made it clear that although he could easily make a really long presentation on the subject—eight hours at least—he would cover as much as he could in his conference time slot. His overarching message, which he repeated many times, was “Talk to the fabricator,” commenting, “Fabricators know their processes and know them well. If we ship them designs that make sense, that are well-thought-out, they won’t have scrap. When they have high levels of scrap, it’s because we as designers have not done our job right.” The question to ponder was, “When there’s scrap at a fab house, who do you think pays?”
He discussed some of the key items of information that a fabricator would check once a design was received for manufacture, the first of which was board size in the context of economic material utilisation. Next came the material choice, number of layers, and layers per given board thickness. There was still a common presumption that all circuit boards must be one-sixteenth of an inch (62 mils) thick, like the early single and double-sided designs and the card-guides they fitted into. He urged designers to think carefully about the consequences when nominating board thickness, commenting on the difficulty in manufacturing a 16-layer controlled impedance design to a finished thickness of 62 mils.
He recalled an early experience of working with a fabricator to optimise the finished thickness of a series of 12-layer designs, taking into account the issues of performance, ease-of-manufacture, and cost-effectiveness, arriving at a figure of 75 ±5 mils. Drilling cost obviously increased with the number of holes, but probably more significant factors were minimum hole size and aspect ratio, pad-to-hole size ratio, and power and ground plane clearance from the hole wall. IPC standards were a useful reference for clearances and tolerances.
Continuing down his list of critical parameters, he discussed minimum conductor widths and spaces, particularly in relation to copper foil thickness and copper balance layer-to-layer. Explaining at each stage the reasons for preferred and non-preferred options, he covered the topics of solder masks and component legends, final finishes, and metallisations, as well as edge connectors, controlled impedance, and design-specific features.
For guidance on actual fabrication cost, he referred to the “fabrication report card” described by Happy Holden, where each line-item was associated with a weighting factor, and low numbers were to be preferred when establishing cost per panel. Mention of cost per panel led to a discussion on preferred panel sizes and material utilisation, reminding designers that the panel also had to accommodate test coupons, tooling holes and copper-thieving in the perimeter, and room for profile-machining between individual circuits.
Again, the advice was, “Talk to the fabricators and make sure your design fits their panels and their processes.” Not forgetting the assembler, Hartley reminded designers to be aware of the keep-out areas necessary for supporting and transporting the board through the assembly process and not to fill them with components. Alternatively, put multiple small boards into a sub-panel. “Talk to the assembler as well.”Page 1 of 2
Suggested Items
Driving Innovation: Direct Imaging vs. Conventional Exposure
07/01/2025 | Simon Khesin -- Column: Driving InnovationMy first camera used Kodak film. I even experimented with developing photos in the bathroom, though I usually dropped the film off at a Kodak center and received the prints two weeks later, only to discover that some images were out of focus or poorly framed. Today, every smartphone contains a high-quality camera capable of producing stunning images instantly.
Hands-On Demos Now Available for Apollo Seiko’s EF and AF Selective Soldering Lines
06/30/2025 | Apollo SeikoApollo Seiko, a leading innovator in soldering technology, is excited to spotlight its expanded lineup of EF and AF Series Selective Soldering Systems, now available for live demonstrations in its newly dedicated demo room.
Indium Corporation Expert to Present on Automotive and Industrial Solder Bonding Solutions at Global Electronics Association Workshop
06/26/2025 | IndiumIndium Corporation Principal Engineer, Advanced Materials, Andy Mackie, Ph.D., MSc, will deliver a technical presentation on innovative solder bonding solutions for automotive and industrial applications at the Global Electronics A
Fresh PCB Concepts: Assembly Challenges with Micro Components and Standard Solder Mask Practices
06/26/2025 | Team NCAB -- Column: Fresh PCB ConceptsMicro components have redefined what is possible in PCB design. With package sizes like 01005 and 0201 becoming more common in high-density layouts, designers are now expected to pack more performance into smaller spaces than ever before. While these advancements support miniaturization and functionality, they introduce new assembly challenges, particularly with traditional solder mask and legend application processes.
Knocking Down the Bone Pile: Tin Whisker Mitigation in Aerospace Applications, Part 3
06/25/2025 | Nash Bell -- Column: Knocking Down the Bone PileTin whiskers are slender, hair-like metallic growths that can develop on the surface of tin-plated electronic components. Typically measuring a few micrometers in diameter and growing several millimeters in length, they form through an electrochemical process influenced by environmental factors such as temperature variations, mechanical or compressive stress, and the aging of solder alloys.