-
- News
- Books
Featured Books
- smt007 Magazine
Latest Issues
Current IssueWhat's Your Sweet Spot?
Are you in a niche that’s growing or shrinking? Is it time to reassess and refocus? We spotlight companies thriving by redefining or reinforcing their niche. What are their insights?
Moving Forward With Confidence
In this issue, we focus on sales and quoting, workforce training, new IPC leadership in the U.S. and Canada, the effects of tariffs, CFX standards, and much more—all designed to provide perspective as you move through the cloud bank of today's shifting economic market.
Intelligent Test and Inspection
Are you ready to explore the cutting-edge advancements shaping the electronics manufacturing industry? The May 2025 issue of SMT007 Magazine is packed with insights, innovations, and expert perspectives that you won’t want to miss.
- Articles
- Columns
- Links
- Media kit
||| MENU - smt007 Magazine
Real Time with… AltiumLive 2020: Vince Mazur Previews New Design Rule Features
November 3, 2020 | I-Connect007 Editorial TeamEstimated reading time: 7 minutes
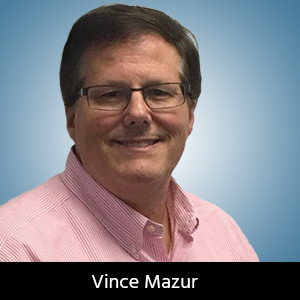
Altium Technical Marketing Manager Vince Mazur discusses his presentation at the recent AltiumLive, which focused on updates to Altium Designer's approach to creating design rules and constraints. Vince explains that these features will be more intuitive for the user, and the update, which is currently in beta, will be released in the future. The company is shifting from “rule-centric” design rules features to capabilities that are more “design-centric,” with applicable rules for each object available at one click.
Andy Shaughnessy: How are you doing, Vince?
Vince Mazur: I’m doing well. Thank you.
Shaughnessy: You did a presentation at the recent virtual AltiumLive about some design rule features that are not quite available yet in Altium tools but may be in the future. Can you tell us about that?
Mazur: Yes. I gave a talk on our rules and constraints capability. We talked about the importance of rules and constraints. At the end of the day, that helps to ensure that you're going to have reliable products that function properly in the field. You don't want something going over-current and burning the board and subjecting your company to liability. Rules and constraints today are strategic intellectual property for a company.
I talked about the company’s products, where we have what I would call a rule-centric view, with rules that are applied to nets and design objects. I contrasted that with more of a design-centric view, where you have nets, components, and other design objects that have rules attached to them as almost a characteristic of that design object. Then, I introduced what we call the Rules 2.0 capability. Altium is trying to improve and really round out our rules and constraints capability.
Basically, we have a very comprehensive query language that really gives you the ability to dig deep and do all types of design rule checking. We’ve taken that forward; it’s improved, and we’ve also created this design-oriented view of rules and constraints in a spreadsheet environment. We now have a document view. You have document tabs, and the tabs are the various design objects that would be, say, PCB nets. We certainly might have components.
What's really nice is that as you click on each one of those tabs, you’ll get the rules that are relevant to that object curated to you automatically. For instance, the idea of a trace with a component-related rule is not relevant. I gave a sneak peek into this capability. Again, it’s the ability to not only develop the rules in a design context and in a spreadsheet environment and get a lot of reuse from those. It’s a completely comprehensive capability that's very easy to use for new users, but it also has the power that users have enjoyed in the past.
Shaughnessy: We published an issue on design rules about a year and a half ago, and it was one of our most popular. Everybody seems to have challenges with design rules.
Mazur: It is possible to create a design rule that doesn't run or doesn't check as you intended it to do. We gave a sneak peek of some really nice capabilities for rule validation. Now, this is not validating your board; this is validating the rules that the scope is valid and that you're going to get the type of verification of your PCB design that you expect. You're actually testing the tests before you apply them because it doesn't seem that long ago that a trace connection was just a trace connection.
Before, it was all about getting the proper size wiring between pins with the proper width for current, etc. Now, when we place a wire, we have all types of requirements. There could be high-speed definitions or impedance-controlled routing aspects; the list goes on and on. As design complexity is increasing, so are the rules required to make sure that you have the ability to target multiple assembly houses or fabrication facilities so that you can have a higher degree of certainty that you're going to get the yield and the performance that you're expecting.
And one of the things that I mentioned was this true story. I was in sales at the time, and I was calling a very widely known company about 10 years ago. They had a really high-end video conferencing system. It had been in production and in the field, and they had some RAM in this device that went through what's called a die shrink, where the semiconductor vendor shrinks the die to improve the margins.
They were assured by the vendor and by the datasheet that there wouldn't be any meaningful change in timing. Well, it turned out that this company was having the weirdest problems with their product out in the field, and it would always happen intermittently. There was just no easy correlation.
It turned out that they had designed their board so close to the timing edge. There was enough difference in that die shrunk device that with environmental factors like humidity and heat, you had this set of circumstances that really created an expensive customer service nightmare.
That's the backdrop that I used to discuss the importance of rules. It's a totally different domain. In some ways, it's more complex than boards, and in some ways, it's easier. But you can get almost anything from a semiconductor company except their rule stack or their rule deck. Rules are very important to realizing silicon, and they’re becoming increasingly important for realizing high-speed PCBs as well.
Shaughnessy: Instead of just having manufacturing design rules, now you have rules for signal integrity and all these different things. It doesn’t seem like design rules are going to get any easier.
Mazur: It's going to get more complex. The good news is that the tool companies are delivering capabilities to meet that challenge. I don't know if it's getting easier. You have to be mindful of many more things today than you had to worry about in the past. Then, there’s this idea of manufacturing yield and having maybe 50% of your boards work perfectly, but there's enough of a process variation somewhere along the line—whether it's the board itself, the etching, the quality of the solder, or variations in the component—that you start running into a yield issue. Again, as soon as you have to touch that board or rework it, you're burning up a lot of cash and time.
Rules are going to play a very important part. As within Altium Designer, we have a schematic editor and a PCB editor. We have ActiveBOM to do bill of materials optimization. The new rules 2.0 capability is an environment in and of itself. It's its own document. One of the capabilities that I really like about it, and many of the customers like about it is that you have an improved interaction between the PCB, the schematic, and the rules itself. For instance, I can look at that spreadsheet of rules, right-click, and cross-probe to that net.
I can define rules in the spreadsheet, but I can also define rules right from the PCB with the right-click. We're trying to bring those domains together. Parts were not a big deal. Now, you get an LCD display, and if it's used in the cellular market or something, two years from now, you might not be able to get that. The churn on parts is really important. When we talk about complexity or whether it's getting easier, you just have to be mindful of a lot of aspects. A couple of years ago, we had situations where companies couldn't manufacture their products because they couldn't get capacitors.
You get a bad batch of etchant in your fab process. The next thing you know, you have boards that don't work. Worse yet are boards that pass all the tests but intermittently fail, which is one of the most costly and embarrassing situations. Whenever you have a failure that happens at the end customer, that's just not good. Rules can help mitigate that along with the attentiveness to these other domains.
Shaughnessy: We'll look forward to seeing this. When do you think this is going to come out?
Mazur: We're not sure. We have this capability in beta, and customers can get access to it. You can also go to the AltiumLive site and see the presentation and see the demonstration. What we're doing is we're trying to collect additional customer feedback. We want to make sure that the quality and implementation are bulletproof and ready to go before we introduce it. But I'm not sure when that's going to be at this point.
Shaughnessy: It was a great event. You all had good graphics and sound, and the chat worked really well.
Mazur: In some regards, it was actually easier to interact; you could pop in and out of these chat rooms. I had some fascinating conversations with customers. It's just amazing. Given the circumstances, I thought that it was well done, but I certainly miss the face-to-face interaction and some of the other activities that we have when we do AltiumLive in person.
Shaughnessy: Thanks for taking the time to meet today.
Mazur: Thank you. Take care, Andy.
Visit Real Time with… AltiumLive 2020 to catch the latest video interviews and event-related content.
Suggested Items
Driving Innovation: Direct Imaging vs. Conventional Exposure
07/01/2025 | Simon Khesin -- Column: Driving InnovationMy first camera used Kodak film. I even experimented with developing photos in the bathroom, though I usually dropped the film off at a Kodak center and received the prints two weeks later, only to discover that some images were out of focus or poorly framed. Today, every smartphone contains a high-quality camera capable of producing stunning images instantly.
Hands-On Demos Now Available for Apollo Seiko’s EF and AF Selective Soldering Lines
06/30/2025 | Apollo SeikoApollo Seiko, a leading innovator in soldering technology, is excited to spotlight its expanded lineup of EF and AF Series Selective Soldering Systems, now available for live demonstrations in its newly dedicated demo room.
Indium Corporation Expert to Present on Automotive and Industrial Solder Bonding Solutions at Global Electronics Association Workshop
06/26/2025 | IndiumIndium Corporation Principal Engineer, Advanced Materials, Andy Mackie, Ph.D., MSc, will deliver a technical presentation on innovative solder bonding solutions for automotive and industrial applications at the Global Electronics A
Fresh PCB Concepts: Assembly Challenges with Micro Components and Standard Solder Mask Practices
06/26/2025 | Team NCAB -- Column: Fresh PCB ConceptsMicro components have redefined what is possible in PCB design. With package sizes like 01005 and 0201 becoming more common in high-density layouts, designers are now expected to pack more performance into smaller spaces than ever before. While these advancements support miniaturization and functionality, they introduce new assembly challenges, particularly with traditional solder mask and legend application processes.
Knocking Down the Bone Pile: Tin Whisker Mitigation in Aerospace Applications, Part 3
06/25/2025 | Nash Bell -- Column: Knocking Down the Bone PileTin whiskers are slender, hair-like metallic growths that can develop on the surface of tin-plated electronic components. Typically measuring a few micrometers in diameter and growing several millimeters in length, they form through an electrochemical process influenced by environmental factors such as temperature variations, mechanical or compressive stress, and the aging of solder alloys.