-
- News
- Books
Featured Books
- smt007 Magazine
Latest Issues
Current IssueSupply Chain Strategies
A successful brand is built on strong customer relationships—anchored by a well-orchestrated supply chain at its core. This month, we look at how managing your supply chain directly influences customer perception.
What's Your Sweet Spot?
Are you in a niche that’s growing or shrinking? Is it time to reassess and refocus? We spotlight companies thriving by redefining or reinforcing their niche. What are their insights?
Moving Forward With Confidence
In this issue, we focus on sales and quoting, workforce training, new IPC leadership in the U.S. and Canada, the effects of tariffs, CFX standards, and much more—all designed to provide perspective as you move through the cloud bank of today's shifting economic market.
- Articles
- Columns
- Links
- Media kit
||| MENU - smt007 Magazine
Estimated reading time: 4 minutes
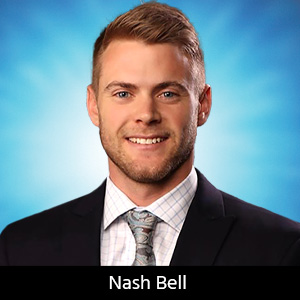
Knocking Down the Bonepile: Fixing Vertical Hole Fill in Plated Holes
For PCBs with larger thermal mass—such as found in high layer count boards or boards with higher weight copper layers—proper and consistent hole fill can be a challenge. It is critical to make sure that these non-visible defects do not become quality escapes while also making sure the proper rework techniques are applied; to get these plated holes properly filled is important.
There are some common board layout or design challenges which can lead to improper or inconsistent hole fill for those PCBs with high thermal mass. When plated through-holes are connected to ground planes or higher-weight innerlayer copper, the thermal mass of that component lead is higher than surrounding ones. This means that to get the board up to the correct reflow temperature requires a longer period of time. If the lead/hole is not brought up to the proper temperature, the wettability of the solder in the hole is lower, thereby not allowing the solder to flow all the way up the barrel.
In other layouts there may be an uneven distribution of thermal mass to each of the component leads which may then have the same impact on hole fill. Another design challenge comes into play when more temperature-sensitive devices are in close proximity to the through-hole devices thereby causing the process engineer to “dial back” the temperature during wave soldering preheat in order to not damage the component. This lower temperature can cause the same insufficient lower hole fill. These are just some of the implications of the design and layout challenges on the hole fill.
Not only can board layout and design challenges cause inconsistent or poor hole fill but assembly processing problems may result in the same deficiency. A recent work [1] indicated that choosing the proper flux was one of the biggest influences on hole fill during wave soldering. A second large influence of improper hole fill is poor penetration of the flux into the through-hole. Another source of improper hole fill is improper board preheating and a lack of dwell time in the wave soldering source. Too long a dwell time can lead to copper dissolution of the plated holes (Figure 1). If pin-in-paste solder printing is used in lieu of wave or selective soldering, insufficient solder paste volume or the location of the print may be cause for improper hole fill. These and other process problems are some of the more common causes of process-related hole fill deficiencies.
Discovering improper hole fill requires that the proper inspection protocols are in place in order to detect a defect. Per the IPC A-610 standards, there are a couple of ways to inspect for proper hole fill. Visual inspection can infer hole fill, but only if substantiated by other means through a process capability analysis. For example, if there is circumferential wetting on both source and destination sides of the plated hole, it can be inferred that the hole is filled. The process for assembly can be optimized and hole fill measured by cross-sectioning the plated through-hole. The process can be confirmed to be in control by linking this hole fill cross-section amount to the visual inspection of both source and destination leads and lands along with the appropriate confidence interval.
Otherwise, x-ray inspection (Figure 2) can confirm hole fill percentage by using built-in algorithms. While AOI systems can detect the presence of both source and destination fillets they cannot determine positively that there is solder in the barrel.
Once the defect is discovered and it has been decided that the component should be reworked as part of the boards’ disposition, there are several rework processes which can be employed. Adding additional solder to the plated through-hole can take on several different forms. A solder fountain with the proper preheater along with the proper flux application can, in some cases, fill the remainder of the barrel. Care must be taken to ensure that the dwell time above the soldering source is kept to a minimum, especially as copper dissolution may result in thinning of barrel walls or incomplete knees in the barrel. Heating of the board in an oven prior to being subjected to the wave temperatures reduces thermal shock to the assembly while limiting dwell time. In the simplest of cases a soldering technician along with the proper flux and board preheater can solve the insufficient hole fill problem via flux and a soldering iron. In cases where the boards have a large thermal mass, the board may first have to be preheated in a controlled oven. Immediately upon removal from the oven the flux and solder can be added to the hole to fill the hole and meet the specification.
Through careful process troubleshooting along with an understanding how board layout can result in insufficient hole fill, the proper rework process can be chosen in order bring the barrel fill into compliance.
Resources
Thomas Shoaf, Joseph Clure, Denis Jean, “Achieving excellent vertical hole fill on thermally challenging boards using selective soldering,” SMTAI Proceedings 2009.
- IPC-A-610 Rev H 7.3.5.1 Supported Hole Solder Fill (a).
- C Hamilton “A Study of Copper Dissolution During Lead-Free PTH Rework,” Circuits Assembly, May 2006.
- Brian Czaplicki, “Advanced Through-Hole Rework of Thermally Challenging Components/Assemblies: An Evolutionary Process,” IPC APEX 2009.
This column originally appeared in the January 2021 issue of SMT007 Magazine.
More Columns from Knocking Down the Bone Pile
Knocking Down the Bone Pile: Addressing End-of-life Component Solderability Issues, Part 4Knocking Down the Bone Pile: Tin Whisker Mitigation in Aerospace Applications, Part 3
Knocking Down the Bone Pile: Gold Mitigation for Class 2 Electronics
Knocking Down the Bone Pile: Basics of Component Lead Tinning
Knocking Down the Bone Pile: Package on Package Rework—Skill Required
Knocking Down the Bone Pile: 2023’s Top Challenges in BGA Rework
Knocking Down the Bone Pile: Eliminating Solder Balls in Hand Soldering
Knocking Down the Bone Pile: Opening a Trace on the Surface of a PCB