-
- News
- Books
Featured Books
- design007 Magazine
Latest Issues
Current IssueProper Floor Planning
Floor planning decisions can make or break performance, manufacturability, and timelines. This month’s contributors weigh in with their best practices for proper floor planning and specific strategies to get it right.
Showing Some Constraint
A strong design constraint strategy carefully balances a wide range of electrical and manufacturing trade-offs. This month, we explore the key requirements, common challenges, and best practices behind building an effective constraint strategy.
All About That Route
Most designers favor manual routing, but today's interactive autorouters may be changing designers' minds by allowing users more direct control. In this issue, our expert contributors discuss a variety of manual and autorouting strategies.
- Articles
- Columns
- Links
- Media kit
||| MENU - design007 Magazine
Estimated reading time: 5 minutes
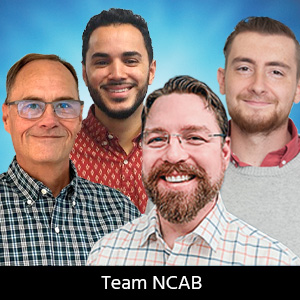
Fresh PCB Concepts: RF PCB Designs–Challenges, Solutions and Tips
Today, RF (radio frequency) circuitry is crammed into a large variety of commercial products. Most of these are handheld wireless devices for medical, industrial, and communications applications. There are also applications in a variety of fields that are migrating from desktop models to become portable communications units.
What Are RF PCBs?
The RF frequency range is usually from 300 KHz to 300GHz, and designs above 300 KHz are considered RF. The microwave frequency range is anything above 300MHz. There’s a considerable difference between RF and microwave circuits versus typical digital and analog circuits. In essence, RF signals are very high frequency analog signals. Therefore, unlike digital, at any point in time a RF signal can be at any voltage and current level between minimum and maximum limits. Moreover, a single band of signal can be very narrow or very wide and carried upon a very high frequency carrier wave.
In short, RF design is very much different and difficult, in terms of PCB design, comparing to that for high-speed digital signal boards.
The Challenges
There are many new challenges for PCB designers, when handling RF board. Among them, the top four factors are:
- RF is far more sensitive to noise, incurring ringing and reflections, which must be treated with great care.
- Impedance matching is extremely critical for RF. And, the higher the frequency, the smaller the tolerance becomes. Practically, only if the total length of the trace from the driver to the receiver is greater than 1/16th of the wavelength of the signal, then impedance control of that trace is required (1/16th of the wavelength is called the critical length of the signal). For example, if you are routing a 1GHz signal and its total length is greater than 425 mils, then that trace needs to be impedance controlled.
- The return loss must be minimized. At very high microwave frequencies, the return signal takes the path of least inductance. As a result, without good PCB design, the return signal will go through power planes, through a PCB’s multi-layers or through some other route, and it will no longer be an impedance-controlled signal.
- Crosstalk is a major issue in high frequency designs. This is because crosstalk is directly proportional to the edge rates of the active line. In this case, the coupled energy from the active line will be superimposed on the victim line. When the board densities increase, the problem of cross talk becomes more critical.
PCB Design Solutions
- Noise: properly terminated, the signal can solve the reflection or ringing issue. Optimized return path with proper ground is another method.
- Impedance matching: for example, the PCB designer must keep it at 50 ohms – 50 ohms out from the driver, 50 ohms during transmission, and 50 ohms into the receiver.
- Return Loss: ground planes underneath the signals are good at providing this path. Therefore, there should be no discontinuities in the plane underneath the signal all the way from the driver to the receiver. Ground planes help minimize not only ground loop currents but also RF leakage into circuit elements.
- Cross talk: always leave adequate space around the signal trace for smooth bends and isolation of the RF signal. Keep all the traces coming out of or going into the transmitter and receiver modules as small as possible. The high-speed signals should be routed as far apart as possible. The distance that the lines run parallel to each other should also be kept to a minimum. All the above measures will reduce the proximity of the two lines and the distance over which the two lines run parallel to each other to reduce cross talk. Other solutions include reducing the dielectric spacing between the line and its reference plane or introducing a co-planar structure, where a ground plane is inserted between the traces. Terminating the line on its characteristic impedance can also reduce the cross talk by as much as 50 percent.
Avoid Losses
Besides the factors above, there are other signal losses as well. The first one is the skin effect loss of a signal, specifically the skin effect loss on the trace of a signal. Dielectric loss is a companion to skin effect loss since both can be created at extremely high frequencies, which is created when electrons flow through a conductor. They bounce back and forth with the electrons on the FR4 PCB substrate, for example. During this interaction, some of the energy from the electrons flowing through a conductor is then transferred to the electrons on the FR4. Consequently, that energy is converted to heat and subsequently lost, and dielectric loss is created.
In such instances, for extremely high frequency microwave circuits it’s best to use polytetrafluoroethylene Teflon, known in the industry as PTFE material. These laminates have a dissipation factor of around 0.001 (compared to FR4’s dissipation factor of 0.02). Secondly, using gold body on RF circuits can greatly reduce the skin losses.
Laminate Properties
When using RF circuits, the designer needs to consider the laminate properties, such as the dissipation factor and dielectric constant (Dk) value and its variation. FR4 has a higher dissipation factor than high frequency laminates like Rogers and Nelco. This means that insertion losses are much higher when using FR4.
These losses are also a function of frequency and will increase as frequency rises. Secondly, the Dk value of FR4 can vary as much as 10%. This in turn varies the impedance. High frequency laminates have more stable frequency properties. Then there is the Dk value itself. When it comes to microwave circuits, the Dk value is tied to the size of the circuit elements, so the designer may be able to decrease the size of the circuit by choosing a laminate with a higher Dk value.
Tips for Designers
In order to achieve more reasonable design and better anti-interference ability for high frequency PCB (Microwave RF PCB), a design engineer should consider the following tips:
- Use inner layer as power ground layer, which will have the effect of shielding and even decreasing spurious inductance and shorten length of signal wire, reducing cross interference between signals.
- Circuit layout must be turn with 45 degree angle, which will help to reduce high frequency signal emission and coupling between each other.
- The shorter the better for length of circuit layout.
- The less the better for through holes.
- Layout between layers should be in vertical direction, top layer as horizontal direction and bottom layer as vertical direction, because this will help to reduce the signal interference.
- Increasing copper on ground layer to reduce the signal interference.
- Do package for important signal traces can obviously improve signals anti-interference ability. Of course, we can also do package for interference sources to avoid interference on other signals.
- Signal traces layout should avoid loop, but should layout according to chrysanthemum link.
- In the power section of integrated circuit, bridging decoupling capacitor.
- Make RF signal 50 ohms.
- Lay out RF first – ALWAYS.
- Isolation is important.
Harry Kennedy is a field application engineer at NCAB Group.
More Columns from Fresh PCB Concepts
Fresh PCB Concepts: Designing for Success at the Rigid-flex Transition AreaFresh PCB Concepts: More Than Compliance—A Human-centered Sustainability Approach
Fresh PCB Concepts: Assembly Challenges with Micro Components and Standard Solder Mask Practices
Fresh PCB Concepts: The Power of a Lunch & Learn for PCB Professionals
Fresh PCB Concepts: Key Considerations for Reliability, Performance, and Compliance in PCBs
Fresh PCB Concepts: Traceability in PCB Design
Fresh PCB Concepts: Tariffs and the Importance of a Diverse Supply Chain
Fresh PCB Concepts: PCB Stackup Strategies—Minimizing Crosstalk and EMI for Signal Integrity