-
- News
- Books
Featured Books
- smt007 Magazine
Latest Issues
Current IssueSupply Chain Strategies
A successful brand is built on strong customer relationships—anchored by a well-orchestrated supply chain at its core. This month, we look at how managing your supply chain directly influences customer perception.
What's Your Sweet Spot?
Are you in a niche that’s growing or shrinking? Is it time to reassess and refocus? We spotlight companies thriving by redefining or reinforcing their niche. What are their insights?
Moving Forward With Confidence
In this issue, we focus on sales and quoting, workforce training, new IPC leadership in the U.S. and Canada, the effects of tariffs, CFX standards, and much more—all designed to provide perspective as you move through the cloud bank of today's shifting economic market.
- Articles
- Columns
- Links
- Media kit
||| MENU - smt007 Magazine
Custom Interconnect Ltd Installs Nordson SONOSCAN Gen7 C-SAM Acoustic Microscope
February 23, 2021 | Custom Interconnect LtdEstimated reading time: 5 minutes
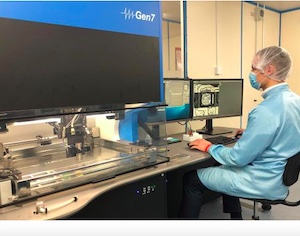
Custom Interconnect Ltd has further invested in Nordson SONOSCAN Gen7 C-SAM Acoustic Microscope from Cupio Ltd to compliment the Nordson DAGE QUADRA 5 X-Ray/CT Scan that they installed in late 2018. This equipment is to be used on its Automotive based SiC power modules on work derived from projects APC15 @FutureBEV and GaNSiC.
Custom Interconnect Ltd, (CIL), based in Andover, Hampshire, is a long-established electronics manufacturer engaged in producing some of the most technically challenging electronic assemblies in the UK. Their capability allows them to meet the functional, environmental, and dimensional demands of high-reliability, mission-critical applications in sectors like medical, aerospace, oil & gas, and others.
However, challenges can arise for other reasons as well. For example, CIL is strongly involved in technology for electric vehicles (EVs) of all types, including battery electric vehicles (BEVs). These vehicles have needed innovation in the design of their power delivery networks because of the very high power levels associated with their batteries.
Two Major EV Projects
These issues are being addressed within two major projects currently running at CIL. In the first, the company is engaged with BMW on APC15@FutureBEV to maximise potential for future BEV systems. @FutureBEV is one of 10 projects funded by the Advanced Propulsion Centre (APC) in its latest round of Government and industry funding for low-carbon emissions research. These collaborative projects between automotive manufacturers, suppliers and academia are working to achieve around 60 million tonnes of CO2 reduction.
In the second project, CIL is the project lead on GaNSIC - a project that stems from the UK Research and Innovation’s (UKRI) ‘Driving the Electric Revolution’ challenge and brings together CIL and Compound Semiconductor Applications Catapult (CSA Catapult). It is set to develop novel ways of applying Silver Sinter pastes to Wide Band Gap (WBG) semiconductors such as Silicon Carbide (SiC) and Gallium Nitride (GaN) devices to optimise their thermal coupling and solve complex power module assembly.
WBG semiconductors are being adopted into EV battery switching systems because of the very high power densities involved. The 800V EV batteries can deliver hundreds of amps, which means that hundreds of kilowatts of power must be switched in spaces often sized no larger than a mobile phone. Up until very recently these devices were bonded to a substrate using conductive epoxies or solders, but there has been a shift away from this traditional method of die attach to Silver Sinter die attach methods to handle the high power density requirements. Silver sintered joints are capable of operating at near 1000°C temperatures.
CIL is involved in designing and manufacturing both SiC and GaN assemblies. These assemblies comprise devices mounted on substrates and interconnected through copper conductors that must be very heavy gauge bonded to manage the required power levels. The associated die bonding process can produce voids; these can compromise thermal properties and result in early failures.
However, inspection for voids, which may previously have been performed using X-ray technology, has become challenging due to the copper’s thickness; X-rays cannot penetrate to the required depth within these conductors.
C-SAM Acoustic Inspection – An Innovative Inspection Technology
The solution is to use c-mode scanning acoustic microscope (C-SAM) technology, as acoustic imaging can reach the required depths within the copper conductors. In fact, C-SAM is the final piece of the jigsaw. The silver sintering method used is a very exacting process, requiring precision at every stage. It can only be properly controlled using three complementary inspection methods – X-ray, C-SAM and CT-Scan and CIL has all three.
For example, acoustic imaging works by collecting reflected sound waves. Air gaps and voids reveal themselves clearly by reflecting the signal strongly. By contrast, X-ray images are created by shadow imaging instead of reflection. All material features are shown at once. Rounded objects that would scatter acoustic waves can be imaged in detail.
CIL is implementing this three-part inspection strategy using Nordson technology supplied by UK inspection and test specialist Cupio. This comprises a Nordson Dage Quadra 5 X-ray and CT-scan machine supplied a couple of years ago, and a Nordson SONOSCAN Gen7 C-SAM acoustic microscope that Cupio has just installed.
Nordson SONOSCAN’s acoustic micro-imaging (AMI) technology collects the highest resolution data from all three dimensions of a sample, creating a virtual sample from which minute defects and features can be detected. The transducers used are specifically developed for AMI analysis, and deliver maximum resolution and maximum penetration at each frequency.
The Gen7 is the seventh generation of the Nordson SONOSCAN technology, and accordingly has many advanced features. Dual 28” 4k monitors provide high-resolution, detailed images, while the machine runs Sonolytics 2 under Windows 10. This is an advanced software package which provides highly intuitive operator interface menus. These maximise results and save operator time.
With five individual motors, the machine offers faster acquisition times, with an up to six times increase in acquisition rates compared with earlier products.
Support for CIL’s Capital Investment Programme
CIL’s decision to buy the Gen7 as their C-SAM solution was based on Cupio’s advice. CIL’s confidence in Cupio comes from their long experience of Nordson technology and Cupio training and support. This spans several years and now includes four major items of capital equipment – an Ink Jet/Auger dispensing system, a NOVO 460 PD selective soldering system, the Nordson DAGE Quadra 5 X-ray inspection system, and the new Gen7.
All the equipment has been reliable, and Cupio’s response to any questions has always been fast and effective.
Projects like these are supported not only by CIL’s investment in their inspection systems and other equipment – which ran to £1.5m in 2020 alone – but also by their quality management system, which covers both their manufacturing sites. The company is accredited to ISO9001:2015, AS9100 Rev D for Aerospace & Defence and ISO 13485:2016 for the manufacture of Medical Devices. It is also working towards the ISO/TS16949 Automotive Qualification.
“The new C-SAM acoustic inspection technology is exciting, because not many manufacturers have it, yet it can be used across many industries, and for applications other than electronics” commented John Boston, Managing Director of CIL, “There are many other manufacturing situations and materials with potential flaws that could only be revealed by this technology, and voiding is a major issue that spans all applications sectors.
“In any case, we will continue with our capital investment programme which is designed to ensure we maintain the most advanced manufacturing capability in the UK. As part of this, we look forward to our continued relationship with Cupio, because we know we can trust them to provide the right inspection solutions to meet any new challenges we may face.”
Testimonial
"The I-Connect007 team is outstanding—kind, responsive, and a true marketing partner. Their design team created fresh, eye-catching ads, and their editorial support polished our content to let our brand shine. Thank you all! "
Sweeney Ng - CEE PCBSuggested Items
How Good Design Enables Sustainable PCBs
08/21/2025 | Gerry Partida, Summit InterconnectSustainability has become a key focus for PCB companies seeking to reduce waste, conserve energy, and optimize resources. While many discussions on sustainability center around materials or energy-efficient processes, PCB design is an often overlooked factor that lies at the heart of manufacturing. Good design practices, especially those based on established IPC standards, play a central role in enabling sustainable PCB production. By ensuring designs are manufacturable and reliable, engineers can significantly reduce the environmental impact of their products.
50% Copper Tariffs, 100% Chip Uncertainty, and a Truce
08/19/2025 | Andy Shaughnessy, I-Connect007If you’re like me, tariffs were not on your radar screen until a few months ago, but now political rhetoric has turned to presidential action. Tariffs are front-page news with major developments coming directly from the Oval Office. These are not typical times. President Donald Trump campaigned on tariff reform, and he’s now busy revamping America’s tariff policy.
Global PCB Connections: Understanding the General Fabrication Process—A Designer’s Hidden Advantage
08/14/2025 | Markus Voeltz -- Column: Global PCB ConnectionsDesigners don’t need to become fabricators, but understanding the basics of PCB fabrication can save you time, money, and frustration. The more you understand what’s happening on the shop floor, the better you’ll be able to prevent downstream issues. As you move into more advanced designs like HDI, flex circuits, stacked vias, and embedded components, this foundational knowledge becomes even more critical. Remember: the fabricator is your partner.
MKS’ Atotech to Participate in IPCA Electronics Expo 2025
08/11/2025 | AtotechMKS Inc., a global provider of enabling technologies that transform our world, announced that its strategic brands ESI® (laser systems) and Atotech® (process chemicals, equipment, software, and services) will showcase their latest range of leading manufacturing solutions for printed circuit board (PCB) and package substrate manufacturing at the upcoming 17th IPCA Show to be held at Pragati Maidan, New Delhi from August 21-23, 2025.
MKS Showcases Next-generation PCB Manufacturing Solutions at the Thailand Electronics Circuit Asia 2025
08/06/2025 | MKS Instruments, Inc.MKS Inc, a global provider of enabling technologies that transform our world, today announced its participation in Thailand Electronics Circuit Asia 2025 (THECA 2025), taking place August 20–22 at BITEC in Bangkok.