-
- News
- Books
Featured Books
- smt007 Magazine
Latest Issues
Current IssueWhat's Your Sweet Spot?
Are you in a niche that’s growing or shrinking? Is it time to reassess and refocus? We spotlight companies thriving by redefining or reinforcing their niche. What are their insights?
Moving Forward With Confidence
In this issue, we focus on sales and quoting, workforce training, new IPC leadership in the U.S. and Canada, the effects of tariffs, CFX standards, and much more—all designed to provide perspective as you move through the cloud bank of today's shifting economic market.
Intelligent Test and Inspection
Are you ready to explore the cutting-edge advancements shaping the electronics manufacturing industry? The May 2025 issue of SMT007 Magazine is packed with insights, innovations, and expert perspectives that you won’t want to miss.
- Articles
- Columns
- Links
- Media kit
||| MENU - smt007 Magazine
2020: A Year of Learning, Innovation for Taiyo America
March 1, 2021 | Pete Starkey, I-Connect007Estimated reading time: 13 minutes
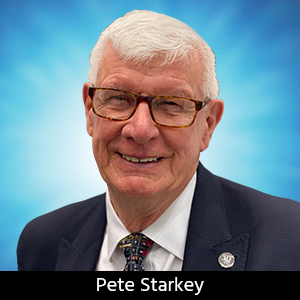
Pete Starkey has a virtual visit with John Fix, director of Sales and Marketing at Taiyo America, where they discuss the changes taking place because of COVID-19 restrictions, and some of the new products Taiyo will be presenting at this year’s IPC APEX EXPO.
Pete Starkey: I’m delighted to have the opportunity to meet, albeit virtually, with an old friend, John Fix. John is director of sales and marketing with Taiyo America, and he’s also a member of the Board of Directors of EIPC. Hello John, from lockdown England.
John Fix: Hi, Pete. Great to be here. I’m here in beautiful Carson City, Nevada, where we just had a huge snowstorm, and we’re digging ourselves out of it. It’s great to see your bright, sunny face, and that’s just going to melt some snow over here.
Starkey: You say kind things, John, thank you. It’s been too long since we met face to face. I think it was at last year’s EIPC winter conference in Rotterdam, Holland, which was mid-February 2020, a year ago now. Just prior to that, it was the IPC APEX EXPO in San Diego, at the beginning of February, and before that was productronica in Munich, Germany, in November 2019.
John, it’s good to have you as a member of the Board of Directors of EIPC, and always nice to see you at European events, especially the European conferences. It’s always an excellent opportunity for learning what’s going on in the technology, but even more than that in terms of meeting people and building networks. We missed the planned summer conference in Sweden, and about now we’d be getting ready to travel to this year’s winter conference, wherever it may have been. The series of online technical snapshots has kept us informed of technical developments and been very successful in maintaining the continuity for EIPC, but it’s not the same as live events. And IPC APEX EXPO will be virtual this year. John, how do you feel about the situation?
Fix: I agree with you, Pete. The EIPC technical snapshots are great, but we all miss the networking part. I look back at all the great times we’ve had, just sitting around after dinner, talking business. How can you not learn something by having a drink with Alex Stepinski, Pete Starkey, Paul Waldner, or Alun Morgan? Those are the kinds of things I miss. Over the years, you learn little things like some history, and some of the new technologies that some board shops are going with. So, it’s unfortunate that 2020 ended up being the way it was; hopefully we can all get back out there soon.
Starkey: I think we got off to a good start last year. We had a couple of very successful events before the lockdowns happened.
Fix: We were very fortunate. Looking back, it’s crazy to think that those were the last times I traveled. My last international flight was out to Rotterdam, and then my last domestic was the APEX show. But let’s hope that things get turned around quickly, and we can have a more productive 2021.
Starkey: We hope so, and we look forward to it. John, what’s new in Taiyo America? I hear you’ve engaged some new people.
Fix: Yes, we have added some new faces. When you think about 2020 and all the negative things in business, for Taiyo it was quite good for us. We had the opportunity to hire our first direct employee in Europe: Frank-Ralf Meyer was hired as our EU sales manager and he’s based out of Germany. He came on board in March, and then about two weeks later, everyone was shut down. He’s been our lone warrior out there, but it’s great. It finally gives Taiyo that direct contact in Europe and our first person to lead the force there. Here in the U.S., we added a technical sales engineer, Kate Han. She comes to us with a great inkjet background as she used to sell inkjet equipment. We really wanted to beef up our ability on that end with all our inkjet products.
Here in Carson City, we added two chemists. One chemist is strictly focused on inkjet, and another chemist is looking at all kinds of new thermal management materials. I have a new Marketing Assistant who’s going to take us to new levels when it comes to social media, and how to do business differently. 2020 was a good year for learning, and how to do business in a different manner. We won’t be face-to-face with customers as much as we’d like to be, so we’ve had to look at different avenues. I think we prepared ourselves really well in 2020 to move forward. Lastly, we acquired Circuit Automation in July, so we have some new faces there that are offering great equipment and service under their new name of Taiyo Circuit Automation.
Starkey: I bet your R&D people have been working hard. What new products have been coming out of your R&D department, John?
Fix: We’ve got a couple of things that we’re highlighting at the APEX virtual event. One product from Japan is a dry film solder mask for flexible circuit boards called FLEXFINER. We’re seeing a lot of interest here in North America, as well as parts of Europe. With so many people building flex, we’re hoping they’ll check out our virtual event where we’ll provide big details into flex. The product comes in amber and black, and some very thin thicknesses—as low as 15 microns and up to about 40 microns. It has different thicknesses and colors, and wonderful, flexible properties. With dry film, it just makes handling flex materials a lot easier.
Starkey: This is a product that I’m really intrigued by. This is the first time I’ve had any knowledge of it at all. I had some background in flexible circuits years ago, and I can remember struggling with flexible coverlays. I dreamed of the day when we could replace those coverlays with something like a solder mask. Is dry film a new venture for Taiyo?
Fix: Yes. Well, for Taiyo Japan we used to have this subcontracted. A couple of years ago, they built their own dry film manufacturing facility. We’ve brought all that in internally now, so we have a very large production facility that only does the dry film solder mask. We have our FLEXFINER brand, as well as the high-end IC packaging type, dry film products. But for the North American market, we have lots of people building flex, and I think this FLEXFINER product line is going to be very successful. We have some of the major customers here in North America looking at it, and we’re really excited about it.
Starkey: How does it differ fundamentally from a conventional coverlay?
Fix: With coverlays in the past, typically you had to punch them, and then you had a laminating process. But that causes accuracy issues, and you have bleed issues with the adhesive. Our product is a full dry film photoimageable product, so you just vacuum-laminate the whole circuit board, and then you go through your standard imaging process. This allows you to get extremely fine features; it’s a DI-type exposing dry film, so you can get that great registration capabilities and that fine resolution. It meets a lot of the requirements of North America and Europe, just to start with. That’s the driving force—quick turn high-end boards.
Starkey: Great. You mentioned vacuum lamination, John. Is this the same sort of vacuum lamination we used to do with previous generation dry film solder masks on rigid PCBs?Page 1 of 2
Suggested Items
Driving Innovation: Direct Imaging vs. Conventional Exposure
07/01/2025 | Simon Khesin -- Column: Driving InnovationMy first camera used Kodak film. I even experimented with developing photos in the bathroom, though I usually dropped the film off at a Kodak center and received the prints two weeks later, only to discover that some images were out of focus or poorly framed. Today, every smartphone contains a high-quality camera capable of producing stunning images instantly.
Hands-On Demos Now Available for Apollo Seiko’s EF and AF Selective Soldering Lines
06/30/2025 | Apollo SeikoApollo Seiko, a leading innovator in soldering technology, is excited to spotlight its expanded lineup of EF and AF Series Selective Soldering Systems, now available for live demonstrations in its newly dedicated demo room.
Indium Corporation Expert to Present on Automotive and Industrial Solder Bonding Solutions at Global Electronics Association Workshop
06/26/2025 | IndiumIndium Corporation Principal Engineer, Advanced Materials, Andy Mackie, Ph.D., MSc, will deliver a technical presentation on innovative solder bonding solutions for automotive and industrial applications at the Global Electronics A
Fresh PCB Concepts: Assembly Challenges with Micro Components and Standard Solder Mask Practices
06/26/2025 | Team NCAB -- Column: Fresh PCB ConceptsMicro components have redefined what is possible in PCB design. With package sizes like 01005 and 0201 becoming more common in high-density layouts, designers are now expected to pack more performance into smaller spaces than ever before. While these advancements support miniaturization and functionality, they introduce new assembly challenges, particularly with traditional solder mask and legend application processes.
Knocking Down the Bone Pile: Tin Whisker Mitigation in Aerospace Applications, Part 3
06/25/2025 | Nash Bell -- Column: Knocking Down the Bone PileTin whiskers are slender, hair-like metallic growths that can develop on the surface of tin-plated electronic components. Typically measuring a few micrometers in diameter and growing several millimeters in length, they form through an electrochemical process influenced by environmental factors such as temperature variations, mechanical or compressive stress, and the aging of solder alloys.