-
- News
- Books
Featured Books
- design007 Magazine
Latest Issues
Current IssueShowing Some Constraint
A strong design constraint strategy carefully balances a wide range of electrical and manufacturing trade-offs. This month, we explore the key requirements, common challenges, and best practices behind building an effective constraint strategy.
All About That Route
Most designers favor manual routing, but today's interactive autorouters may be changing designers' minds by allowing users more direct control. In this issue, our expert contributors discuss a variety of manual and autorouting strategies.
Creating the Ideal Data Package
Why is it so difficult to create the ideal data package? Many of these simple errors can be alleviated by paying attention to detail—and knowing what issues to look out for. So, this month, our experts weigh in on the best practices for creating the ideal design data package for your design.
- Articles
- Columns
- Links
- Media kit
||| MENU - design007 Magazine
EIPC Technical Snapshot: Cleanliness
March 1, 2021 | Pete Starkey, I-Connect007Estimated reading time: 5 minutes
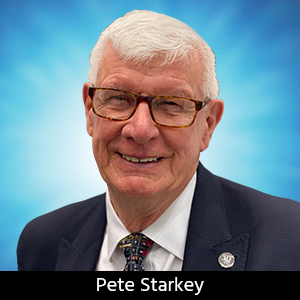
John Ling’s invitation to the fifth in EIPC’s series of Technical Snapshots was as droll as we have come to expect: “In these confined days of lockdown, and exhortations to stay at home and only go out for exercise, this only exercises the natural inclination to hop on a ‘plane to some sunshine.’ Although not the same as Factor 20, one of our webinars gives a high degree of protection from harmful ignorance, and you do not have to go out in the cold.”
Cleanliness was the focus of this informative and enlightening event on Feb. 17, 2021, introduced by EIPC technical director Tarja Rapala-Virtanen and moderated by EIPC board member Christian Behrendt, CEO of German PCB fabricator ILFA.
Freddy Gilbert
His first speaker was Freddy Gilbert, technology analyst with Zestron Europe, with a presentation that described in detail the technique of ion chromatography and its benefits in assessing the cleanliness of PCB assemblies by determining the nature and extent of ionic contamination.
Gilbert explained that specific ions could trigger corrosion on specific areas of electronic assemblies and that because of differences in their hygroscopic properties, the moisture-related failure mechanisms that each could induce would be related to the ambient relative humidity. Ion chromatography could identify the presence and concentrations of anions and cations as well as weak organic acid residues from fluxes and solder pastes. It could also reveal quality problems with PCB materials, for example, under-cured solder mask. The test procedure was defined in the IPC Test Methods Manual: IPC TM 650 2.3.28A.
How did it work? Gilbert described the five stages:
- Sample extraction with a suitable solvent mixture.
- Injection of the sample into the separating column.
- Separation as different species moved at different speeds through the column.
- Detection by conductivity measurement.
- Analysis of the results in terms of identification of ionic species and calculation of their concentration.
IPC-CH-65B gave guidelines for acceptable limits. Interpretation of the analysis results helped in identifying the source of the contamination.
He made it very clear that ion chromatography was entirely different from ROSE testing. Ion chromatography was a complex analytical technique, most useful for validation procedures and risk analysis. ROSE testing gave a global value for contamination, expressed in terms of sodium chloride equivalent, and was more suitable for process control. An ion chromatography test could take 20 hours, whereas a ROSE test could be completed in one hour. Each procedure had its particular area of applicability and the results were not directly comparable.
Gilbert discussed the effects of varying extraction parameters on response characteristics: Standard values according to IPC TM 650 TM 2.3.28 were one hour at 80°C with 75/25 v/v isopropanol/water. He demonstrated that extraction time and isopropanol content had little influence on the extraction of most anions and cations; higher temperatures increased measured ion concentrations and the measured concentrations of weak organic acids tended to increase with increasing extraction time and isopropanol content.
Professor Rajan Ambat
The second presentation was given by Professor Rajan Ambat from the Centre for Electronic Corrosion at the Technical University of Denmark, who discussed the significance of the cleanliness of electronic assemblies in improving their intrinsic humidity robustness and corrosion reliability.
He remarked that cleanliness-related effects could result from PCB fabrication, assembly, handling or end-use, although the assembly process was the predominant source. The chemistry of residues was significant because the responses of different ionic residues to humidity depended on critical humidity levels and other factors. Regarding flux residues, the overall chemistry depended on the soldering method, and the activator component was particularly critical. It was important to optimise the amount of flux used and to avoid excessive application. The residue from reflow processes was different from other residues, and components such as rosin, resin, and binder were also important.
Two effects were considered critical: the opening-up of the residue, enabling activator components to be released; and the spreading of residue, enabling adjacent points on the assembly to be potentially connected under humidity. The stand-off height of a component was an important factor in determining the amount of residue and how it interacted with humidity. The cleanliness of the assembly was also an important factor affecting the performance of conformal coating, whose adhesion could be adversely affected by the chemistry of the residue.
Professor Ambat concluded his presentation by announcing a virtual seminar on climatic reliability of electronics: global challenges and perspectives, March 4-5, 2021.
Emma Hudson
The presentations of Freddy Gilbert and Professor Ambat provided an appropriate background for EIPC vice-president Emma Hudson to review the proposed changes to the cleanliness section of the IPC-6012DA-WAM1 Automotive Applications Addendum, which would provide a more comprehensive approach to determining acceptable contamination levels on bare PCBs.
IPC-6012DA: Automotive Applications Addendum to IPC-6012D had originally been issued in 2016 to cater for PCBs specifically used in the automotive industry, and Amendment 1, which was issued in 2018, had included revisions to the cleanliness requirements, where the task group believed there was a need to differ for automotive applications. The existing required techniques were considered inadequate and there was a need to expand the required testing to ensure that PCBs being supplied would continue to meet the needs of the automotive assembler. The Technical Cleanliness proposal would allow a move toward a risk-based approach on the level of foreign-object-debris present rather than a zero-tolerance approach.
Test methods recommended for process and material qualification and for quarterly verification were listed as ion chromatography (IC), surface insulation resistance (SIR) and resistance of solvent extract (ROSE). Hudson made clear the differences between “recommended,” “should,” and “shall” in the wording of IPC specifications as she reviewed the current cleanliness section in which there were very few “requirements” and lots of “recommendations.” The decision had been made to review the whole cleanliness section, as well as adding Technical Cleanliness, and she listed the proposed changes. Significantly, it was proposed that major PCB qualification “shall” include IC, SIR, and ROSE testing, and that ROSE or other available test methods would be allowed for daily process control, as agreed between user and supplier. The requirement for lot qualification would be the same as for daily process control. An added requirement was for the manufacturer to monitor measured contamination by statistical process control, and OSP-finished boards would no longer be exempt from testing. Test results and frequency were still required to be as agreed between user and supplier.
The justification for these proposals was that the current addendum had only the ROSE test as a requirement, whereas the other tests were “recommended” or “should” be conducted. ROSE did not tell whether contamination levels would lead to failures, or identify what specific contaminants were on the PCB. Therefore a more comprehensive approach was needed in determining and monitoring acceptable contamination levels.
Christian Behrendt led a very constructive interactive discussion session with the presenters, which brought an impressive technical webinar to a close.
Grateful thanks to the presenters for generously sharing their knowledge, and to EIPC for organising another in their excellent series of Technical Snapshot events.
Suggested Items
Silicon Mountain Contract Services Enhances SMT Capabilities with New HELLER Reflow Oven
07/17/2025 | Silicon Mountain Contract ServicesSilicon Mountain Contract Services, a leading provider of custom electronics manufacturing solutions, is proud to announce a significant upgrade to its SMT production capability with the addition of a HELLER 2043 MK5 10‑zone reflow oven to its Nampa facility.
Knocking Down the Bone Pile: Addressing End-of-life Component Solderability Issues, Part 4
07/16/2025 | Nash Bell -- Column: Knocking Down the Bone PileIn 1983, the Department of Defense identified that over 40% of military electronic system failures in the field were electrical, with approximately 50% attributed to poor solder connections. Investigations revealed that plated finishes, typically nickel or tin, were porous and non-intermetallic.
SHENMAO Strengthens Semiconductor Capabilities with Acquisition of PMTC
07/10/2025 | SHENMAOSHENMAO America, Inc. has announced the acquisition of Profound Material Technology Co., Ltd. (PMTC), a premier Taiwan-based manufacturer of high-performance solder balls for semiconductor packaging.
KYZEN to Highlight Understencil and PCB Cleaners at SMTA Querétaro Expo and Tech Forum
07/09/2025 | KYZEN'KYZEN, the global leader in innovative environmentally responsible cleaning chemistries, will exhibit at the SMTA Querétaro Expo & Tech Forum, scheduled to take place Thursday, July 24, at Centro de Congresos y Teatro Metropolitano de Querétaro.
Driving Innovation: Direct Imaging vs. Conventional Exposure
07/01/2025 | Simon Khesin -- Column: Driving InnovationMy first camera used Kodak film. I even experimented with developing photos in the bathroom, though I usually dropped the film off at a Kodak center and received the prints two weeks later, only to discover that some images were out of focus or poorly framed. Today, every smartphone contains a high-quality camera capable of producing stunning images instantly.