-
- News
- Books
Featured Books
- smt007 Magazine
Latest Issues
Current IssueSupply Chain Strategies
A successful brand is built on strong customer relationships—anchored by a well-orchestrated supply chain at its core. This month, we look at how managing your supply chain directly influences customer perception.
What's Your Sweet Spot?
Are you in a niche that’s growing or shrinking? Is it time to reassess and refocus? We spotlight companies thriving by redefining or reinforcing their niche. What are their insights?
Moving Forward With Confidence
In this issue, we focus on sales and quoting, workforce training, new IPC leadership in the U.S. and Canada, the effects of tariffs, CFX standards, and much more—all designed to provide perspective as you move through the cloud bank of today's shifting economic market.
- Articles
- Columns
- Links
- Media kit
||| MENU - smt007 Magazine
Estimated reading time: 4 minutes
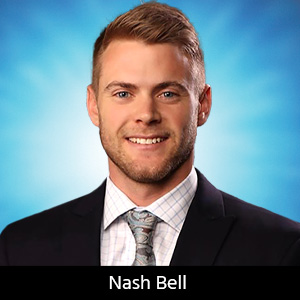
Knocking Down the Bone Pile: Salvaging Components for Other Uses
Electronic components and their availability (or rather their lack of) have been in the news recently. Automotive suppliers are struggling with their supply chain as electric vehicle production, and the associated consumption of electronic components, continues to expand. Fabless semiconductor companies lacking capacity have also been in the news with their deliveries pushed out to 2022. All this news, and the ever-shortening life cycle of semiconductor devices, have left some electronic manufacturers wanting for supply. In some cases, shortages of given components can be met by harvesting them from existing assemblies.
The harvesting (Figure 1) of electronic components from circuit boards allows obsolete, expensive, long-lead-time order electronic components to be re-used. These components can be harvested from scrap piles, from obsolete assemblies, or by other means. Care must be taken to ensure that the components can be reused in a manufacturing environment, and given the greatest chance for a reliable component to be soldered in place.
Disassemble the Hardware
The first step in salvaging components from an assembly where valuable electronic components are soldered in place is the dissembling of the hardware. This operation may include the backing out of screws, and the detachment of sub-assemblies and larger components, such as heat sinks, fans, and power supplies.
Begin the Salvage Operation
Once all the mechanical sub-assemblies have been taken off the board, the salvaging operation can begin. It is critical to understand all the requirements from the end user, including items like the packaging of salvaged components, removal or non-removal of conformal coatings, the MSL level of the components, and many other aspects.
MSL Level
If the PCBs have been held in open storage or are field returns, the moisture sensitivity level, (MSL) of the to-be-removed components generally requires a pre-bake of the components prior to removal. This will help ensure the long-term reliability of the component to be salvaged.
Coatings
Not only should the MSL of the components be considered, but it should be noted whether the boards have been conformally coated, have had components staked in place, or underfill applied to the components. The presence of underfill or conformal coating on and underneath the components to be removed is significant as there are numerous stripping processes which can be employed as part of the removal operation. In some cases, this may cause difficulties, including throughput issues. It is important to determine the overall area of conformal coating removal at the onset. For example, if conformal coating needs to be removed from the component body, this process may have the unintended consequence of part number, date code, and other information being removed from the package.
Adhesives and underfills may soften during removal but their later removal from the component body may take too much time to make the salvaging economically feasible. In addition to the above items, the electrostatic discharge (ESD) sensitivity level of the component should also be considered during the salvaging process. Just because the parts are being salvaged doesn’t mean that they should not be handled like “live” boards. The component datasheet will inform the remover of the type of ESD precaution that needs to be taken.
Labels
Another area of concern is the label on the component or the PCB. All the salvaging processes—including the conformal coating stripper, heat, cleaner and flux—will interact with the board where components are to be salvaged. The part or board label may need to be masked with Kapton™ or liquid mask to prevent the markings from disappearing during processing.
Other Operations
There are several operations on the components themselves which need to be considered. Small legged leads such as high pin count QFPs may need to have their leads straightened and formed to be coplanar upon removal to meet the JEDEC requirements so that they can be placed correctly onto a potentially new PCB. Solder balls will need to be re-attached to a removed BGA or CSP through a re-balling process to place it onto a new assembly. Part datasheets will help determine the correct ball size. Customer order details will determine the correct solder alloy.
For part salvaging, be careful of the maximum temperature the components can withstand. This will be important to understand as the right removal process tool and profile needs to be chosen. Proper profiling will ensure that the temperature limits of the component are maintained during the removal process.
Future Use
One of the criteria important in determining the requirements for the salvaged components is an understanding of how the components will be placed onto their next board. For example, if the components will be hand soldered in place, then co-planarity and amount of remnant solder left over on the component will be less than that of a component to be placed using automation.
One of the final criteria is looking at the kind of component packaging that will be required. The components need to be placed into tape and reel packaging, tubes or trays, in order to deliver the salvaged components to manufacturing operations. It is recommended that the components be marked (Figure 2) in some fashion to keep track of which components are going on to specific assemblies.
This column originally appeared in the March 2021 issue of SMT007 Magazine.
More Columns from Knocking Down the Bone Pile
Knocking Down the Bone Pile: Addressing End-of-life Component Solderability Issues, Part 4Knocking Down the Bone Pile: Tin Whisker Mitigation in Aerospace Applications, Part 3
Knocking Down the Bone Pile: Gold Mitigation for Class 2 Electronics
Knocking Down the Bone Pile: Basics of Component Lead Tinning
Knocking Down the Bone Pile: Package on Package Rework—Skill Required
Knocking Down the Bone Pile: 2023’s Top Challenges in BGA Rework
Knocking Down the Bone Pile: Eliminating Solder Balls in Hand Soldering
Knocking Down the Bone Pile: Opening a Trace on the Surface of a PCB