-
- News
- Books
Featured Books
- design007 Magazine
Latest Issues
Current IssueProper Floor Planning
Floor planning decisions can make or break performance, manufacturability, and timelines. This month’s contributors weigh in with their best practices for proper floor planning and specific strategies to get it right.
Showing Some Constraint
A strong design constraint strategy carefully balances a wide range of electrical and manufacturing trade-offs. This month, we explore the key requirements, common challenges, and best practices behind building an effective constraint strategy.
All About That Route
Most designers favor manual routing, but today's interactive autorouters may be changing designers' minds by allowing users more direct control. In this issue, our expert contributors discuss a variety of manual and autorouting strategies.
- Articles
- Columns
- Links
- Media kit
||| MENU - design007 Magazine
Estimated reading time: 3 minutes
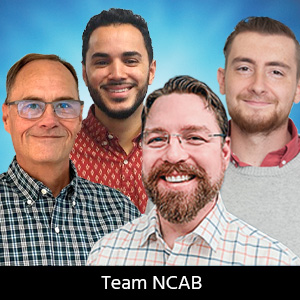
Fresh PCB Concepts: Mitigating the Increasing Prices of PCBs
By now, you might have noticed that the cost of PCBs is increasing. What’s worse is that there are also supply chain issues causing additional delays on PCBs. You can’t redesign every board in order to reduce cost, so instead, try these tips to help you reduce manufacturing costs.
There are many articles that have explained the reasoning for the increased pricing, including this I-Connect007 article. We are going to focus on how you can respond, and develop some understanding of the factors driving this increased price and lead time.
One of the biggest impacts to a board’s lead time is the callout of a specific material in the fab notes. Customers are sometimes shocked when they find out boards can’t even start manufacturing until the factory can order the hard-to-find material. Why is that?
Most likely it’s because the fab notes call for a specific material that isn’t widely available, or is primarily common to a local region. Not only does it take time for a factory to source and receive the material, but it also often means this material will come at a premium price. In previous years it was easy to overlook the added cost of material, but now it’s time to take another look at how changes to material can save both time and money.
When assessing material, the first thing an engineer should do is assess the end equipment application. You should think twice before changing material on medical and RF applications, but a majority of boards aren’t going into high performance or harsh environment electronic products. Two magic words—“or equivalent”—can unlock availability of material. This means that the factory is allowed to use an IPC identified equivalent to the material choice you called out. This can often be confirmed by checking the material datasheet, but essentially it comes down to having strong relationships with the factory in order to have both the control and the knowledge that you are risking quality over a shorter lead time and possibly a lower price.
Another hint about the material: look at the Tg requirement. Understanding your reflow/soldering cycles for your end application means that you can chose the right Tg requirement for the PCB and save the extra material cost.
In addition to the material, you should check into the copper weight used on your board. Increasing copper weight is great way to increase current carrying capacity, but also comes at a premium. We’ve noticed that many boards designed with 2 oz. copper don’t actually need the current carrying capacity. These boards could have been designed with a lesser copper weight, thus reducing both cost and availability without hampering the final application.
If you’re adding extra copper weight because of reliability, consider that if you’re working with a quality partner for your PCBs, you shouldn’t have to worry about inconsistencies in copper thickness. At NCAB, for example, we always plate vias to Class 3 CU thickness in holes, as the vias are usually are the weakest link.
We also recommend that you consider the surface finish your boards have. Did you know that immersion gold (ENIG) surface finish can increase your PCB cost by approximately 20% on otherwise standard 2L boards? This is a way to save significant costs on your PCBs. There are cost-effective options like lead-free HASL that can be used instead for some PCBs. Here are a few indicators that you can use lead-free HASL (LF HAL) instead of ENIG.
- Consider the characteristics of the ENIG finish. ENIG has an electroless layer of nickel followed by a thin layer of immersion gold plating. The plating method results in a flat surface finish that is great for assembly rework on quite specific components.
- ENIG works best for BGA components due to the flat finish. If your design is mostly through hole components, or at least don´t have critical BGA components, ask your PCB manufacturer how much you could save if you switched to a LF-HAL surface finish.
Adapting to changes in supply chain will help you to maximize profit without sacrificing quality. There will always be nuanced questions. Feel free to reach out to your local NCAB office if you’d like to discuss further.
Harry Kennedy is a field application engineer at NCAB Group.
More Columns from Fresh PCB Concepts
Fresh PCB Concepts: Designing for Success at the Rigid-flex Transition AreaFresh PCB Concepts: More Than Compliance—A Human-centered Sustainability Approach
Fresh PCB Concepts: Assembly Challenges with Micro Components and Standard Solder Mask Practices
Fresh PCB Concepts: The Power of a Lunch & Learn for PCB Professionals
Fresh PCB Concepts: Key Considerations for Reliability, Performance, and Compliance in PCBs
Fresh PCB Concepts: Traceability in PCB Design
Fresh PCB Concepts: Tariffs and the Importance of a Diverse Supply Chain
Fresh PCB Concepts: PCB Stackup Strategies—Minimizing Crosstalk and EMI for Signal Integrity