-
- News
- Books
Featured Books
- pcb007 Magazine
Latest Issues
Current IssueInventing the Future with SEL
Two years after launching its state-of-the-art PCB facility, SEL shares lessons in vision, execution, and innovation, plus insights from industry icons and technology leaders shaping the future of PCB fabrication.
Sales: From Pitch to PO
From the first cold call to finally receiving that first purchase order, the July PCB007 Magazine breaks down some critical parts of the sales stack. To up your sales game, read on!
The Hole Truth: Via Integrity in an HDI World
From the drilled hole to registration across multiple sequential lamination cycles, to the quality of your copper plating, via reliability in an HDI world is becoming an ever-greater challenge. This month we look at “The Hole Truth,” from creating the “perfect” via to how you can assure via quality and reliability, the first time, every time.
- Articles
- Columns
- Links
- Media kit
||| MENU - pcb007 Magazine
Estimated reading time: 7 minutes
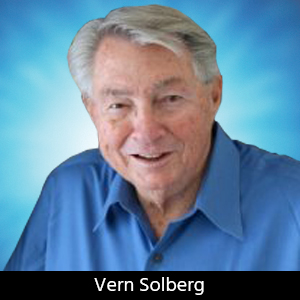
Designers Notebook: The 'New and Growing' Embedded Resistors
Why is embedded resistor technology considered to be “new” and “growing” despite decades of history?
In fact, a broad number of established PCB fabricators are knowledgeable about the materials and processes for embedding resistor elements but not all may be prepared to alter procedures established for their more conventional multilayer circuit board customer base.
The next question is, “What is the motivation for embedding resistors?”
- PCB densification—a primary driver
- Functionality—a contributor
- Performance—an enhancement
- PCB assembly—simplified
The primary benefit of embedding resistor elements within the layers of the multilayer PCB is the ability to more efficiently arrange and interconnect the primary active components placed on the outer surface of the circuit boards surface. Furthermore, embedding most of the passive components can contribute to the development of a more robust PCB assembly, one that will not be physically impacted by environmental extremes or when the end product is exposed to excessive vibration and shock. Additionally, incorporating these passive resistor elements within the circuit board structure simplifies the logistics required for procurement, stocking, and assembly processing for multitudes of damage-prone ceramic-based components.
A key issue facing the PCB designer is to determine which resistors will be more suitable for embedding within the circuit board’s structure and which resistor elements are more appropriate for placement onto the circuit board’s outer surface. The printed board designer really acts as the facilitator and is rarely the sole decision maker for embedding components. Because of the potential cost impact on the printed circuit board, the decision to embed resistors is more likely an engineering and management level issue, typically justified by the restricted surface area reserved for mounting passive components and/or the potential for enhanced performance of the finished product.
In preparation for implementing embedded resistor technology the designer and/or program manager must first seek an experienced supplier company that can furnish practical guidance in selecting a process (thick-film or thin-film) that will meet both technical and budgetary (cost) goals established for the end product.
Formed resistor elements may be furnished as a printed thick-film composition or an imaged and chemically etched thin-film process.
- Thick-film resistor materials are formulated to furnish a wide range of primary values and have been successfully used for a broad number of commercial applications. The resistor formulations are based on carbon-filled polymer chemistry that enables screen printing or deposition to form elements directly onto pre-patterned termination lands furnished on a designated circuit board layer.
- Thin-film resistors are formed using copper foil material that is pre-coated with resistive material. The resist layer is deposited onto the copper sheet material using vapor disposition that provides uniformity of the resistor base value across the entire sheet. Thin-film resistor materials are supplied in a variety of base values using Grade 3 copper foil. The copper sheets developed for the thin-film resistor forming process are available in thicknesses of 18 µm (0.5 oz) and 35 µm (1 oz).
The information furnished in this installment of this series has been prepared to provide guidance to the circuit board design professional considering the implementation for embedding “thick-film” resistors.
When identifying candidate resistors for embedding, the designer must consider both resistor value range, the allowable tolerance bandwidth, and application. The thick-film resistor forming process is generally employed where tolerances are less critical, primarily used in digital and analog circuit applications for terminating resistors, current limiting, transistor biasing as well as for pull-up/pull-down resistors where precise value tolerances are not critical.
Resistor Functionality
Termination resistors are placed at the end of an electrical transmission line or when working with differential pair signals. Pull-up and pull-down resistors on, the other hand, are commonly used in logic circuit applications. For example, the function of the pull-down resistor is to hold the logic signal near to zero volts when no other active device is connected. The pull-up resistor’s function is to ensure that the voltage between power and ground cannot be directly connected. Depending on the circuit logic type, typical values selected for termination, pull-up and pull-down resistors can vary in values that range from 500 ohm to 10K ohm and may tolerate value tolerance limits as high as ±20%. Resistor elements designated for “current limiting” are used for setting an upper limit to the amount of current that flows through a component while “transistor biasing” resistors are commonly used in combination with transistors and semiconductor components.
The overall performance of the thick film resistor materials is related to the optimized circuit design and fabrication process. The materials and process parameters of polymer thick-film resistor must be considered in order to successfully achieve the performance requirements of circuit designs. For example, the decision on what landsize-to-aspect-ratio to use for a particular resistor element depends on a number of factors. These include target resistance values, electrical considerations, available resistivity values, trimming requirements, and the distribution of resistances of all the resistors present on the same layer of the board.
In general, on most printed circuit board designs, resistor value distribution will vary between 1W at the low end and 10MW at the highest. Selecting the most practical composition for the thick-film resistors, the PCB designer should consider the most prominent base-value usage and select a material that facilitates the lower end of the value range. From a statistical standpoint, the greater number of resistors in a digital or analog circuit will likely fall into a range between 10W and 10KW (Table 1). With that in mind, selecting the 10W material as the base value will provide greater flexibility in expanding the resistor geometry to accommodate a wide range of finished resister values.
Geometry Principles
The geometry of the resistance material can be as simple as a square or rectangle, or for more complicated resistor values, a serpentine shape designed to maximize resistor element length while minimizing area. The values provided are based on the resistance measured between opposite edges of a square. For example, a single square of 1K material printed or deposited between two copper lands will provide a 1K resistor element while a pattern that is twice the length, or two squares, furnishes a 2K resistor.
The rectangular “bar” geometry (Figure 1) is most common for resistors with values close to the basic thick film composition selected while the serpentine geometry is employed when resistor values are significantly greater than the thick film materials base value. The “top-hat” shaped resistor geometry is commonly applied for elements that will likely require extensive laser trimming to reach their target value.
Suppliers recommend that designers furnish resistor widths and lengths greater than 0.25 mm (0.010 in). Larger resistor dimensions will reduce the reliance on the print variations or accuracy of the copper etching processes. Regarding terminating the resistor elements, the land pattern geometry provided for the resistor termination should allow for a nominal 0.25–0.50 mm overlap of the thick-film resist material and consider allowances for printing process variables.
As noted, the thick-film resistor ink formulations are based on a carbon-filled polymer chemistry. By adjusting the ratio of carbon content within the polymer medium, the material can be formulated to furnish a wide range of primary values. Following printing or deposition of the resist compound the circuit boards are transferred to an oven for curing at temperatures in a range between 150–250°C. Five commercial sources for printable or deposited thick-film resistive materials and the base value range that they offer are furnished in Table 2.
When the application requires a value modification or a tolerance that is better than that noted in Table 2, laser trimming systems can be employed to make the necessary adjustments. The examples shown in Figure 2 illustrate thick film resistors that have been modified using laser technology to achieve a specific value or tolerance target.
Laser trimming systems developed for high volume PCB fabrication are equipped with multiple flying probe contactors that are preprogrammed to reach any component location, size, orientation and layout within the board or multi-unit panel. The probe contactors sweep across the board’s surface contacting the embedded component lands or dedicated test point locations to measure and transmit the resistor value and tolerance as printed to direct the laser in making the required cut (Figure 3). Automated calibration routines ensure cut placement accuracy within 15 microns. Cut widths are typically in the 10–50-micron range.
Those considering thick-film resistor technology must understand that the process requires precise imaging and consistent material density to ensure that the printed image will meet the target resistor value range. And due to the printing and curing complexity for printed thick-film resistors, the printed board fabricator will prefer applying only one resistor base value material onto a single substrate layer. If the fabricator can use an inkjet-type of deposition process, however, they will have greater latitude in applying two or more base value resistive ink compounds onto a single circuit layer.
Although the thick-film resistor forming process has a long history and remains a popular, low-cost solution for embedding, many PCB fabrication companies may not offer this capability. This is because thick-film resistor forming is considered a wet process requiring controlled storing, careful mixing, printing and curing operations. PCB fabricators that do offer embedded resistor capability will often prefer to adopt alternative thin-film processing solutions.
In Part 2, I will review the materials, design rules, and process parameters for embedding formed thin-film resistors.
This column originally appeared in the April 2021 issue of Design007 Magazine.
More Columns from Designer's Notebook
Designers Notebook: Basic PCB Planning Criteria—Establishing Design ConstraintsDesigners Notebook: Layer Stackup Planning for RF Circuit Boards
Designers Notebook: Addressing Future Challenges for Designers
Designers Notebook: Impact of Advanced Semiconductor Packaging on PCB Stackup
Designers Notebook: Implementing HDI and UHDI Circuit Board Technology
Designer's Notebook: Heterogeneous Integration and High-density SiP Technologies
Designers Notebook: PCB Design and IPC-CFX for Assembly Automation
Designer’s Notebook: What Designers Need to Know About Manufacturing, Part 2