-
- News
- Books
Featured Books
- pcb007 Magazine
Latest Issues
Current IssueInventing the Future with SEL
Two years after launching its state-of-the-art PCB facility, SEL shares lessons in vision, execution, and innovation, plus insights from industry icons and technology leaders shaping the future of PCB fabrication.
Sales: From Pitch to PO
From the first cold call to finally receiving that first purchase order, the July PCB007 Magazine breaks down some critical parts of the sales stack. To up your sales game, read on!
The Hole Truth: Via Integrity in an HDI World
From the drilled hole to registration across multiple sequential lamination cycles, to the quality of your copper plating, via reliability in an HDI world is becoming an ever-greater challenge. This month we look at “The Hole Truth,” from creating the “perfect” via to how you can assure via quality and reliability, the first time, every time.
- Articles
- Columns
- Links
- Media kit
||| MENU - pcb007 Magazine
LPKF: Calculating the Savings Potential for Depaneling
April 14, 2021 | LPKFEstimated reading time: 3 minutes
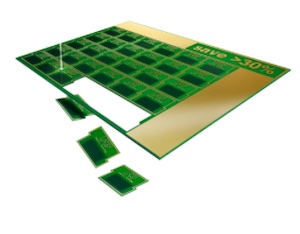
With the Panel Layout Optimization Tool (PLOT), LPKF offers a tool for calculating the materials savings that can be achieved with laser cutting.
In printed circuit board depaneling, laser technology users can achieve significant materials savings and thus considerably lower their costs with full-section cuts through the panels. This can be calculated with the new Panel Layout Optimization Tool (PLOT) from LPKF.
Promises of cost savings abound, but the extent to which they materialize is not always clear in advance – unless it is calculated using specific data. To make this possible, LPKF has developed a calculation tool that calculates the minimum material requirements for PCBs with laser full-section cutting and compares the results to those achieved with mechanical milling. It can be used on the company homepage simply and without any obligations. The user uploads the desired PCB layout and specifies the panel design. From these data, the PLOT calculates the materials savings and displays the result directly and clearly. An analysis document in PDF form is then made available to the user. The calculation runs via a secure server and meets the latest data protection standards.
Why Calculate?
Background for the development of the Panel Layout Optimization Tool: The right design for a panel is an extremely important factor in ensuring cost-efficient and low-error manufacturing of PCBs. If the panel area is used optimally, then more PCBs can be placed on one panel. This is advantageous with respect to both material usage and manufacturing efficiency.
However, the design process is subject to important guidelines and limitations, which are clearly presented on the LPKF website and in a white-paper available there. Challenges lie in the different geometries and component densities as well as in the need for technical cleanliness. The panel size and shape play a role as guidelines. A process-dependent border for handling is indispensable in some cases. These factors must be specified in the PLOT calculation tool from LPKF and are also used as the calculation basis. The calculation thus delivers a well-founded comparison of the utilization of panel sizes for milling and laser cutting.
Laser Technology Has an Advantage Here
Because the spacings between the PCBs and the cutting edge widths can be considerably smaller with a laser process than with mechanical depaneling processes, the material savings potential resulting from laser full-section cutting is very high. Premilled, relatively wide (2–3 mm) channels that are provided in mechanical depaneling processes and in routing for later cutting of tabs can be omitted in the panel design. Because laser processing provides a maximum amount of freedom in terms of geometry, the individual PCBs can be optimally placed and aligned on the panel. Overall materials savings of more than 30% on average, and even higher in some cases, can be achieved.
The maximized panel utilization also provides synergies in downstream process steps in PCB manufacturing because it significantly reduces handling requirements. The bigger the increase in panel utilization, the more significant the cost degression effects, especially for high lot volumes.
The next point chalked up on the laser side is the technical cleanliness, which leads to high-quality and reliable printed circuit boards. Milling dust is not an issue with laser cutting, and with LPKF CleanCut, there is no carbonization of the cut edges. Additionally, with laser cutting, mounting close to the cut edges is possible because there are virtually no mechanical stresses generated in the material in the regions around the cut edges. As a result, PCBs can be implemented more compactly – that’s another positive effect of using laser technology. In the end, there are a few arguments besides the lowered costs that speak in favor of the laser as the tool of choice for depaneling.
Testimonial
"Advertising in PCB007 Magazine has been a great way to showcase our bare board testers to the right audience. The I-Connect007 team makes the process smooth and professional. We’re proud to be featured in such a trusted publication."
Klaus Koziol - atgSuggested Items
Meet the Author Podcast: Martyn Gaudion Unpacks the Secrets of High-Speed PCB Design
07/16/2025 | I-Connect007In this special Meet the Author episode of the On the Line with… podcast, Nolan Johnson sits down with Martyn Gaudion, signal integrity expert, managing director of Polar Instruments, and three-time author in I-Connect007’s popular The Printed Circuit Designer’s Guide to... series.
Intervala Hosts Employee Car and Motorcycle Show, Benefit Nonprofits
08/27/2024 | IntervalaIntervala hosted an employee car and motorcycle show, aptly named the Vala-Cruise and it was a roaring success! Employees had the chance to show off their prized wheels, and it was incredible to see the variety and passion on display.
KIC Honored with IPC Recognition for 25 Years of Membership and Contributions to Electronics Manufacturing Industry
06/24/2024 | KICKIC, a renowned pioneer in thermal process and temperature measurement solutions for electronics manufacturing, is proud to announce that it has been recognized by IPC for 25 years of membership and significant contributions to electronics manufacturing.
Boeing Starliner Spacecraft Completes Successful Crewed Docking with International Space Station
06/07/2024 | BoeingNASA astronauts Barry "Butch" Wilmore and Sunita "Suni" Williams successfully docked Boeing's Starliner spacecraft to the International Space Station (ISS), about 26 hours after launching from Cape Canaveral Space Force Station.
KIC’s Miles Moreau to Present Profiling Basics and Best Practices at SMTA Wisconsin Chapter PCBA Profile Workshop
01/25/2024 | KICKIC, a renowned pioneer in thermal process and temperature measurement solutions for electronics manufacturing, announces that Miles Moreau, General Manager, will be a featured speaker at the SMTA Wisconsin Chapter In-Person PCBA Profile Workshop.