-
-
News
News Highlights
- Books
Featured Books
- smt007 Magazine
Latest Issues
Current IssueSupply Chain Strategies
A successful brand is built on strong customer relationships—anchored by a well-orchestrated supply chain at its core. This month, we look at how managing your supply chain directly influences customer perception.
What's Your Sweet Spot?
Are you in a niche that’s growing or shrinking? Is it time to reassess and refocus? We spotlight companies thriving by redefining or reinforcing their niche. What are their insights?
Moving Forward With Confidence
In this issue, we focus on sales and quoting, workforce training, new IPC leadership in the U.S. and Canada, the effects of tariffs, CFX standards, and much more—all designed to provide perspective as you move through the cloud bank of today's shifting economic market.
- Articles
- Columns
- Links
- Media kit
||| MENU - smt007 Magazine
Estimated reading time: 4 minutes
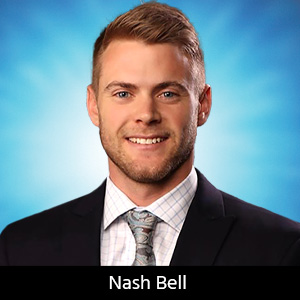
Knocking Down the Bone Pile: Solder Excavation and Rework
To properly perform rework—the removal and replacement of a component on a PCB—the remnant solder needs to be properly removed after the component has been desoldered and removed. This step is important for the following reasons:
- The component, especially if it is a small outline package or an ultra-fine pitched component, needs to lie co-planar to the surface of the pad in order to get the replacement component properly aligned.
- The remnant solder may already have a thick intermetallic layer which may cause the solder joint to prematurely fail.
There are several methods in use for the removal of the remnant solder including but not limited to vacuum extraction, solder braid (wick) and coupon use. Each method has its own advantages as well as drawbacks.
The solder braid approach is outlined in the IPC 7711 Methods for PCB Rework, section 4.1.3 (Figure 1)—surface solder removal-braid method:
- In this method, solder braid, which is a copper mesh, is placed onto the fluxed PCB pad. Some braids are pre-fluxed which increases the wicking action.
- The braid size chosen should be slightly smaller than the pad dimension. It is recommended that paste flux be used to make sure the flux is active during the solder removal process.
- Make sure the tip temperature corresponds to the reflow temperature of the solder alloy being removed. Move the soldering iron tip up and down perpendicular to the pad with the soldering braid in between the tip and pad.
- When solder wicks up into the braid, remove the braid from the pad advancing it such that a non-solder filled section of the braid can be used on the rest of the pad.
- Do not “swab the deck” on multi-leaded components or area array sites moving across the pads as the pads could be lifted or the mask damaged. This operation is operator dependent and requires skills practice in order to not damage the PCB.
- The solder wick method requires the least amount of equipment investment, but it does require intermediate soldering skills.
In addition to the solder wicking method, vacuum extraction is another means for removing the solder from a pad location. This vacuum can be created by a manual spring-loaded pump, a hand tool, as part of a BGA/leadless device rework system, or as a stand-alone programmable tool (Figure 2).
It is not recommended to use a manual pump as there is a lack of continuous suction at the tip as the solder joint is cycled through several heating and cooling cycles. In the case of the other powered vacuum desoldering tools, a hole in the tip center is used as a vacuum to remove solder which has gone into reflow. Matching the diameter of the tip to the width of the pad is recommended as larger-than-pad-sized tips may burn the PCB laminate. After applying flux to the location, place the heated tip onto the pad gently until you sense the solder is going into reflow. Do not exert pressure onto the pad as it may cause pad damage.
Integrated programmable soldering excavation tools usually have a sensor which keeps the distance of the PCB at a fixed height. Reservoirs which contain the excavated solder need to be cleaned out whether it is a manual hand piece or part of an automated system. The vacuum solder extraction method, regardless of the type of system used, is fast and requires less skill and experience compared to the solder braid approach.
The technique which is used the least for solder removal in PCB rework is the copper coupon method. This method uses a flux-dipped copper coupon to remove all the solder at one time. The coupon is placed onto a BGA rework system nozzle and heated, then slowly lowered onto the surface of the PCB. As it gets in the vicinity of the BGA or CSP pads, solder is wicked onto the coupon. One of the advantages of this approach is the speed of excavation. This is offset by potential coplanarity problems for the PCB which may cause damage to the PCB laminate or cause it to not be as effective, the cost of the specially tooled single use coupon, and the need to be able to program or stop the coupon from going down onto the PCB.
Whether using the solder wick approach, a solder vacuum excavation tool, or a wicking coupon, solder removal from the pads prior to placement of the replacement device is important from both a reliability and quality of placement perspective. The use of the technique depends on the kind of tooling capabilities, the sophistication of the rework equipment, and the experience of the operators. Cycle times and potential risks in damaging the PCB laminate factor into choosing the appropriate method for PCB rework.
This column originally appeared in the May 2021 issue of SMT007 Magazine.
More Columns from Knocking Down the Bone Pile
Knocking Down the Bone Pile: Addressing End-of-life Component Solderability Issues, Part 4Knocking Down the Bone Pile: Tin Whisker Mitigation in Aerospace Applications, Part 3
Knocking Down the Bone Pile: Gold Mitigation for Class 2 Electronics
Knocking Down the Bone Pile: Basics of Component Lead Tinning
Knocking Down the Bone Pile: Package on Package Rework—Skill Required
Knocking Down the Bone Pile: 2023’s Top Challenges in BGA Rework
Knocking Down the Bone Pile: Eliminating Solder Balls in Hand Soldering
Knocking Down the Bone Pile: Opening a Trace on the Surface of a PCB