-
- News
- Books
Featured Books
- design007 Magazine
Latest Issues
Current IssueProper Floor Planning
Floor planning decisions can make or break performance, manufacturability, and timelines. This month’s contributors weigh in with their best practices for proper floor planning and specific strategies to get it right.
Showing Some Constraint
A strong design constraint strategy carefully balances a wide range of electrical and manufacturing trade-offs. This month, we explore the key requirements, common challenges, and best practices behind building an effective constraint strategy.
All About That Route
Most designers favor manual routing, but today's interactive autorouters may be changing designers' minds by allowing users more direct control. In this issue, our expert contributors discuss a variety of manual and autorouting strategies.
- Articles
- Columns
- Links
- Media kit
||| MENU - design007 Magazine
Estimated reading time: 2 minutes
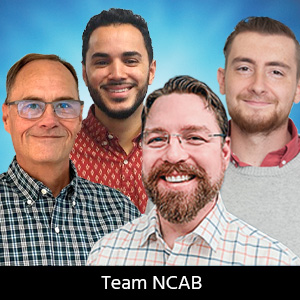
Fresh PCB Concepts: HDI Microvia Features in Illustrations
Often, when I work with a customer or a designer on an HDI board, I hear questions about the different types of microvias and even what exactly a microvia is. I thought this would be a good opportunity to explain microvias and discuss aspect ratios with microvias. This is important to know when designing an HDI PCB because the different types vary in complexity. And the more complex, the more this affects the cost.
According to the new definition within IPC-T-50M, a microvia is a blind structure with a maximum aspect ratio (which is a measure of the ratio between the depth of the hole and its width) of 1:1, terminating on a target land with a total depth of no more than 0.25 mm measured from the structure’s capture land foil to the target land.
Figure 1: An illustration of a microvia.
In the case of microvia boards, we’re most likely to see the depth be the dielectric thickness or the distance between layers one and two. For example, when we consider our design guidelines, typically we see layer one to layer two dielectrics’ thickness or depth, being 60–80 microns.
The size of the microvia hole (its width) is within the 80–100 micron range. Considering these values, this provides an aspect ratio ranging from 0.6:1 to 1:1; keep in mind that as the dielectric thickness increases so must the size of the microvia.
Microvias are not just limited to the outer layers, or the dielectrics between layers one and two. We can see them within the inner layers and this ability to have more than one layer of microvia dictates the different types and its features as defined in IPC-2226.
Type I structures are those that contain a single microvia layer on either one or both sides of the core (Figure 2). It uses both plated microvia and PTH for interconnection so, in effect, it employs only blind via holes. They do not employ buried vias.
Type II structures are similar to Type I in that they contain just a single microvia layer on either one or both sides of the core and use both plated microvia and PTH for interconnection (Figure 3). Yet unlike Type I, these structures employ both blind and buried via holes.
Type III are a little more complex in that this structure or build contains at least two layers of microvia on either one or both sides of the core (Figure 4). It also uses both plated microvia and PTH for interconnection as well as both blind and buried vias.
The graphics we created are really the best visual to illustrate the various types of HDI features and the varying complexities. Many times when I get these questions I will send the illustrations rather than trying to explain the different features, or at least send the graphics first while I explain them. Of course, if you would like more details about the specific features (blind vias, buried vias, PTHs, etc.) I am more than happy to explain (or illustrate) that further, or perhaps on another column.
Ruben Contreras is a program manager and field application engineer at NCAB Group.
More Columns from Fresh PCB Concepts
Fresh PCB Concepts: Designing for Success at the Rigid-flex Transition AreaFresh PCB Concepts: More Than Compliance—A Human-centered Sustainability Approach
Fresh PCB Concepts: Assembly Challenges with Micro Components and Standard Solder Mask Practices
Fresh PCB Concepts: The Power of a Lunch & Learn for PCB Professionals
Fresh PCB Concepts: Key Considerations for Reliability, Performance, and Compliance in PCBs
Fresh PCB Concepts: Traceability in PCB Design
Fresh PCB Concepts: Tariffs and the Importance of a Diverse Supply Chain
Fresh PCB Concepts: PCB Stackup Strategies—Minimizing Crosstalk and EMI for Signal Integrity