-
-
News
News Highlights
- Books
Featured Books
- design007 Magazine
Latest Issues
Current IssueAll About That Route
Most designers favor manual routing, but today's interactive autorouters may be changing designers' minds by allowing users more direct control. In this issue, our expert contributors discuss a variety of manual and autorouting strategies.
Creating the Ideal Data Package
Why is it so difficult to create the ideal data package? Many of these simple errors can be alleviated by paying attention to detail—and knowing what issues to look out for. So, this month, our experts weigh in on the best practices for creating the ideal design data package for your design.
Designing Through the Noise
Our experts discuss the constantly evolving world of RF design, including the many tradeoffs, material considerations, and design tips and techniques that designers and design engineers need to know to succeed in this high-frequency realm.
- Articles
- Columns
- Links
- Media kit
||| MENU - design007 Magazine
It’s FR-4, Jim, But Not as We Know It!
July 8, 2021 | Alun Morgan, Ventec International GroupEstimated reading time: 4 minutes
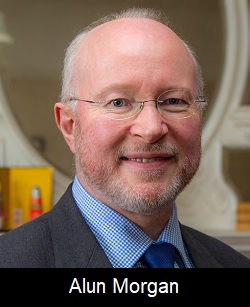
Whilst Gene Roddenberry was writing Star Trek in one corner of the U.S., another group of engineers was working on a less daring project, but one which was nonetheless ground-breaking and continues to influence our language to this day.
That group was the National Electrical Manufacturers Association (NEMA), and their magnum opus, at least as far as the PCB industry was concerned, was the “L1” specification. As Star Trek was responsible for adding terms such as photon torpedo, dilithium crystal, and warp drive to our language, so NEMA were responsible for the terms G-10, FR-4, and FR-5. “FR” was the NEMA abbreviation for “flame retardant” and materials so classified were marked with a red manufacturer’s logo. The terms also marked a change from the early 1960s where materials produced solely from paper reinforcement were used to produce PCBs. NEMA defined the terms used during the transition to glass-reinforced PCB materials that were to become the mainstay of our industry.
The evolution of printed circuit board substrates has necessitated a change of view in how performance is classified. The NEMA classifications are based on the physical properties of the basic chemical makeup of the materials used. We are, for example, used to classifying substrates according to their glass transition temperature, Tg. Accordingly, we refer to “standard,” “mid-range” or “high” Tg substrates. It is no surprise, therefore, that many designers and users of PCBs have assumed that the Tg value has a direct relationship to the thermal endurance of the substrate and have specified a “high Tg” product for an application requiring high thermal resistance. I am reminded of Spock’s words, “Insufficient facts always invite danger.”
The Tg value merely marks a phase change in the resin chemistry whereby enough energy (temperature) is available to increase the rotational freedom of the polymer to allow it to transition from a glassy to a rubbery state. If energy is continued to be applied, then the next transition that would be expected is the Tm, or melting temperature. Here is where thermoset plastics spring a surprise. In theory, there is indeed a Tm; however, the temperature required to melt a thermoset exceeds the thermal decomposition temperature, Td. The consequence of this is that a thermosetting material never reaches the Tm—it decomposes into carbon and a variety of gases long before it can ever get there. The Tg has no direct correlation with the thermal decomposition temperature.
To specify thermal performance, we need to set our phasers to stun and to consider all performance aspects relevant to the end application. This marks a shift in the classification. It is not sufficient to specify a “high Tg” substrate; instead, performance should be specified according to the application. This may include the Tg, Tm, time to delamination, coefficient of thermal expansion in the Z-axis, and thermal conductivity to fully characterize a substrate suitable for applications requiring a focus on thermal management.
Since the days of Star Trek, we have also moved from impulse power, and believe it or not, my first job after leaving university was in a research laboratory where a space impulse engine was developed to “warp speed.” I am, of course, referring to the continuing journey of increasing signal speeds and data rates. James Montgomery Scott (Scotty) famously said, “I canna' change the laws of physics.” So far as we know, he was correct; however, we can certainly exploit them.
The PCB world of the 1960s was a much simpler place. Our reference frequency was 1 MHz and circuits were largely comprised of analogue devices, with very few of the nasty square waveforms with theoretical bandwidths tending toward infinity to deal with. The high-frequency spectrum in the past was divided into two bands—one where FR-4 worked and one where it didn’t. Where it didn’t, many designers faced a no-win scenario where they couldn’t use FR-4 and the only alternative was PTFE which could push the project into an insurmountable position of unaffordable cost and limited materials availability.
When Captain James T. Kirk faced his no-win scenario in the simulated encounter with the Klingons in “The Kobayashi Maru,” his solution was to cheat. Circuit designers today are indeed fortunate that they have no need to cheat as the gap between FR-4 and PTFE performance and cost has been filled by entirely new ranges of substrate materials based on their performance at high frequency and high data rates for digital circuity. These new generations of material allow the designer the flexibility to select the appropriate substrate for the application without over-engineering performance that is neither required nor can be afforded.
FR-4 itself has also evolved. In the 1960s, it was a single grade, but today it encompasses a range of materials with diverse properties and chemistries. The recent split into FR-4.0 and FR-4.1 (characterizing brominated and non-brominated flame retardants, respectively) came about in recognition of the fact that all FR-4s do not perform the same and test results of one variant could no longer be considered representative of another. “It’s FR-4 Jim, but not as we know it!”
Despite the recent years of tremendous upheaval in our industry, I hope that you share my enthusiasm and excitement for our continuing mission to aggressively seek out and develop the material solutions of tomorrow. May we all live long and prosper as we boldly go where no one has gone before.
Alun Morgan is technology ambassador for the Ventec International Group.