-
- News
- Books
Featured Books
- smt007 Magazine
Latest Issues
Current IssueSpotlight on India
We invite you on a virtual tour of India’s thriving ecosystem, guided by the Global Electronics Association’s India office staff, who share their insights into the region’s growth and opportunities.
Supply Chain Strategies
A successful brand is built on strong customer relationships—anchored by a well-orchestrated supply chain at its core. This month, we look at how managing your supply chain directly influences customer perception.
What's Your Sweet Spot?
Are you in a niche that’s growing or shrinking? Is it time to reassess and refocus? We spotlight companies thriving by redefining or reinforcing their niche. What are their insights?
- Articles
- Columns
- Links
- Media kit
||| MENU - smt007 Magazine
Estimated reading time: 4 minutes
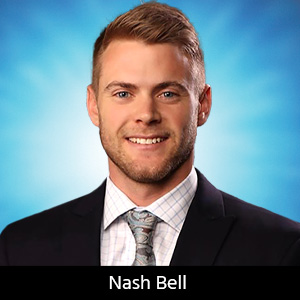
Knocking Down the Bone Pile: Cleaning of ‘No Clean’ Fluxes in PCB Rework
The original intention of a “no clean” solder was to eliminate the post PCB assembly cleaning process while still not risking any performance or long-term reliability degradation. Some industry surveys indicate that about one-half of assemblers using no-clean flux chemistries clean the PCB after assembly. Many times, the first look or inspection of a reworked solder joint is the aesthetic appeal defined by the cleanliness inspection criteria found in IPC-A-610 (Section 10.6). Due to uneven heating from the rework process, corrosive no-clean flux activators may not be completely encapsulated with activated flux. This means the activators are on the exposed circuits and are likely to cause corrosion and dendritic growth, thereby negatively impacting reliability.
In PCB rework, a no-clean flux (Figure 1) is active when spread out on the board and the only way that that residue becomes safe to leave on the board is when it is properly activated via a temperature reflow cycle. That requires all the flux, even that spilling over to neighboring devices and not being subject to a reflow cycle, to be cleaned off the PCB. Hand solder and rework methods that do not sufficiently control flux volume are going to leave dangerous residues such as chlorides and weak organic acids which may, in turn, impact the performance or reliability of the solder joints.
There are several ways to mitigate the problems associated with rework and the associated flux residues left behind:
Limit the volume of flux applied to the rework area. More flux means that there is a greater likelihood of non-benign residue being left on the board.
- Proper training on flux and flux residue removal for any hand assembly or rework technician. This training should include the method of cleaning, the method of rinsing, as well as the disposal of any remnant solution. The training on “when to use” what cleaning solution is also important.
- Proper training on the importance of activating the flux during rework.
Cleaning the flux post rework is defined in Procedure 2.2.1 of the IPC 7711/7721 “Rework and Repair of Printed Circuit Assemblies.” The procedure defines that up to 10 ml of cleaning solution for four square inches of affected area can be used to clean the reworked area. A clean, soft-bristled brush is then used to scrub the area followed by an isopropyl alcohol rinse. This is an important step as soiled brushes may bring unwanted debris and flux residue to the to-be-cleaned area. Any excess and leftover IPA from the rinsing process should then be cleaned with a lint-free cloth. Then the cleaning process inspection occurs per the agreed upon inspection criteria. Other cleaning processes can be used if agreed upon between the builder and the end customer.
For PCB rework, even for a “no clean” flux formulation, the area around a solder joint area post reflow should be cleaned. The idea of a no residue or no-clean flux is a misnomer. Instead, the flux should be described as low residue. These residues, along with other contaminants from the rework area such as airborne contaminants, human skin, tool debris, etc. need to be removed. There are numerous reasons to clean an electronics assembly post rework, namely to:
- Allow for better inspection/better cosmetic appearance around the solder joint
- Promote the surface for better coating adhesion
- Allow for testing to be done where required
- Prevent electrical problems (noise or capacitive coupling)
- Eliminate a longer-term reliability or corrosion problem
As PCB density increases, an understanding of the impact of cleaning becomes more challenging. Premature failure or improper component functionality is site specific and, therefore, a localized testing means of cleanliness is crucial. A localized ionic contamination measuring method using an extraction technique in the area of interest has become more acceptable to measuring the contaminants left behind after PCB rework. Gone are the days of the ROSE testing which measures the ionic contaminants on the entire assembly.
There are several benefits to cleaning the low residue no-clean flux. One of the benefits is to ensure that any underfill or replacement conformal coating will be properly adhered to the PCB. Any residue left behind may outgas and impact adhesion. The right defluxing process and saponifier is used to facilitate better inspection and enhanced cosmetic appearance. A defluxing process is a cleaning process in that everything is cleaned. Contaminant species from board fabrication (like feeder tape residue), component fabrication residues, assembly residues, and human handling residues all are cleaned off in a cleaning process. All of these may cause performance issues and their resultant removal mitigates this risk.
While the cleaning of the flux holds some distinct advantages, there are several disadvantages to cleaning a no-clean flux after rework. Since DI water alone cannot be used to clean off the residue, a saponifier chemistry will need to be used and, therefore, extra expense added in terms of chemicals, cleaning equipment (if not already on site) as well as chemical disposal. By not properly cleaning all of this off, you can end up with active flux on the board and be in a worse position with respect to the reliability of the assembly. These and other drawbacks need to be considered when contemplating the necessity for a post-rework cleaning process.
The choice of the cleaning agent is important. It needs to match the residue and cleaning process. Dissolution of the residue at a fast rate is critical. Equally critical is the cleaning method’s ability to deliver the cleaning agent to the no-clean residues.
Reliable hardware is more challenging to build due to component size miniaturization, bottom termination devices, shortened distance between conductors, and higher pinout devices in a small footprint. These factors require that there is no entrapped flux residue and that the board is properly cleaned post rework.
This column originally appeared in the July 2021 issue of SMT007 Magazine.
More Columns from Knocking Down the Bone Pile
Knocking Down the Bone Pile: Addressing End-of-life Component Solderability Issues, Part 4Knocking Down the Bone Pile: Tin Whisker Mitigation in Aerospace Applications, Part 3
Knocking Down the Bone Pile: Gold Mitigation for Class 2 Electronics
Knocking Down the Bone Pile: Basics of Component Lead Tinning
Knocking Down the Bone Pile: Package on Package Rework—Skill Required
Knocking Down the Bone Pile: 2023’s Top Challenges in BGA Rework
Knocking Down the Bone Pile: Eliminating Solder Balls in Hand Soldering
Knocking Down the Bone Pile: Opening a Trace on the Surface of a PCB