-
- News
- Books
Featured Books
- design007 Magazine
Latest Issues
Current IssueProper Floor Planning
Floor planning decisions can make or break performance, manufacturability, and timelines. This month’s contributors weigh in with their best practices for proper floor planning and specific strategies to get it right.
Showing Some Constraint
A strong design constraint strategy carefully balances a wide range of electrical and manufacturing trade-offs. This month, we explore the key requirements, common challenges, and best practices behind building an effective constraint strategy.
All About That Route
Most designers favor manual routing, but today's interactive autorouters may be changing designers' minds by allowing users more direct control. In this issue, our expert contributors discuss a variety of manual and autorouting strategies.
- Articles
- Columns
- Links
- Media kit
||| MENU - design007 Magazine
Estimated reading time: 3 minutes
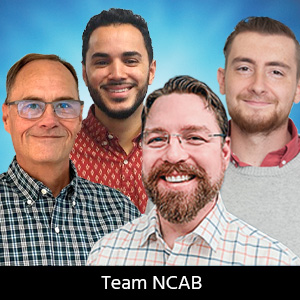
Fresh PCB Concepts: Auditing a Factory—When Everyone Wins in the PCB Supply Chain
One of the most important activities when it comes to maintaining the best quality of PCBs is to be constantly evaluating partner factories. An important tool for this process is auditing those factories on a consistent basis. This includes its processes, procedures, working instructions, and checking upon how well the factory has understood and implemented demands to produce quality, reliable PCBs. If a deviation is found, allow the factory to take the proper steps to improve. When the factory responds, develops better processes and pushes the bar a little higher each time, that’s when we’re in a situation where we all benefit.
Based on my personal professional experience, I truly feel this can only be achieved by being onsite. Particularly when working with overseas factories, being local, speaking the language and sharing the culture will be important factors. If this cannot be achieved in-house, I recommend working with a partner who has local infrastructure in place and is able to perform regular audits on all factories. This is something that should be taken very seriously: Audit hard, but fair; ask the tough questions.
When we complete audits, we focus on these four specific types:
- Full factory audit: This includes an initial qualification audit and then an annual audit
- Process audit: As the name says, it focuses on a specific process, the laser drilling process for example
- Follow-up audit: This is for the purpose of getting onsite regarding any corrective and preventative actions implemented by the factory
- Sustainability audit: We all need to be concerned about sustainable development as well as social responsibility and it is, therefore, important that partner factories have the same focus. Do they have the same business ethics and desire to improve on the environmental and human aspects as you do?
During the audit we look for several key aspects like whether the factories’ quality and measurement systems are running well, measurement maintenance, statistical control, and if the factory itself has a tight control over the process. We also check how the factory translates the specified needs and demands of the customer into the instructions that govern processing on the shop floor. Equally importantly, we audit how these demands measured and confirmed.
Before a follow up, the factory needs to review and understand the complaint data and take the improvement actions needed. To do this the factory needs to use appropriate quality process improvement tools and methods. For example, the Ishikawa fault finding method and the 5 Whys root cause method (these are essentially tools identifying cause and effect, and ultimately the root cause of an issue). From there a responsible person should be assigned with a reasonable improvement schedule. A production quality engineer should follow up the actions taken to evaluate the relevant methods of operation, along with other relevant document changes and assess the effectiveness of actions.
How can you ensure that you remain 100% objective? You must have very clear rules and requirements. For example, at NCAB we have rules that don’t only focus on how to measure, manage, and control the factory’s quality performance but also how to coordinate and guide staff performance and participation. Each audit involves a team of three people for three days minimum. Our production quality engineer, who oversees the specific factory, is not allowed to act as auditor. We report on details and facts (not perceptions) in with the intent that the process gives a truly reliable result.
This process works best when it is methodical, in-depth, and comprehensive, but it can consume a lot of time and resources. So, what does that provide in the end? Aside from a cooperative and fair approach to help our partner factories develop and grow, with this type of auditing approach helps achieve almost 100% quality. In fact, last year in 2020 NCAB, as an example, achieved 99.3% after completing 175 audits. A win-win-win for all involved.
For many companies, an in-house audit process such as this is not attainable, particularly at the local level. However, there are still ways to achieve this level of quality. I recommend working with a trusted supplier that can present a clearly defined audit process and can provide results from that process.
Michael “Mike” Marshall is a field application engineer at NCAB Group.
More Columns from Fresh PCB Concepts
Fresh PCB Concepts: Designing for Success at the Rigid-flex Transition AreaFresh PCB Concepts: More Than Compliance—A Human-centered Sustainability Approach
Fresh PCB Concepts: Assembly Challenges with Micro Components and Standard Solder Mask Practices
Fresh PCB Concepts: The Power of a Lunch & Learn for PCB Professionals
Fresh PCB Concepts: Key Considerations for Reliability, Performance, and Compliance in PCBs
Fresh PCB Concepts: Traceability in PCB Design
Fresh PCB Concepts: Tariffs and the Importance of a Diverse Supply Chain
Fresh PCB Concepts: PCB Stackup Strategies—Minimizing Crosstalk and EMI for Signal Integrity