-
- News
- Books
Featured Books
- design007 Magazine
Latest Issues
Current IssueProper Floor Planning
Floor planning decisions can make or break performance, manufacturability, and timelines. This month’s contributors weigh in with their best practices for proper floor planning and specific strategies to get it right.
Showing Some Constraint
A strong design constraint strategy carefully balances a wide range of electrical and manufacturing trade-offs. This month, we explore the key requirements, common challenges, and best practices behind building an effective constraint strategy.
All About That Route
Most designers favor manual routing, but today's interactive autorouters may be changing designers' minds by allowing users more direct control. In this issue, our expert contributors discuss a variety of manual and autorouting strategies.
- Articles
- Columns
- Links
- Media kit
||| MENU - design007 Magazine
Estimated reading time: 3 minutes
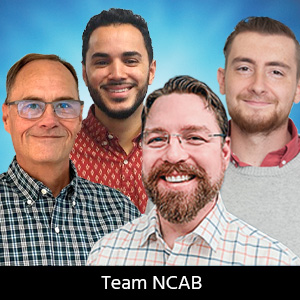
Fresh PCB Concepts: Does the Assembly Process Damage a PCB? (Part 2—Time to Delamination)
In part 1 of this series, I commented upon the effect that the assembly process has upon a printed circuit board. The assembly temperatures applied do, in fact, burn away the epoxy of the FR-4 composite material. The higher the temperature, the faster the rate of burn. I touched upon the relationship between the glass transition temperature (Tg), decomposition temperature (Td), and the maximum continuous operating temperature (MOT). There is another gauge that can be used to help a designer or contract manufacturer understand this point and that is the time to delamination test. These are referred to as either the T260 or T288 tests.
What is the T260/T288 Time to Delamination?
This is a test defined by the IPC under IPC-TM-650 Test Method 2.4.24.1. A test sample is incrementally raised in temperature 10°C/min to 260°C (or 288°C) and then dwells at 260°C (or 288°C). When an event occurs such as delamination, cracking, moisture release, stress relaxation, decomposition, or a sudden movement, a sensor detects the change. The time in minutes from the start of the dwell time to the event at 260°C (or 288°C) is the time to delamination.
How Does This Value Relate to Anything in the Assembly Process?
The T260/T288 test values are a gauge of how durable the FR-4 shall be when exposed to heat for long periods of time. FR-4 is a NEMA grade designation for glass-reinforced epoxy laminate material that is flame-resistant. It is a general designation that applies to many different materials with different performance levels. The performance levels shall vary between different laminate manufacturers and material grades they manufacture. No two grades of FR-4 from different laminate manufacturers are exactly alike. They all meet the minimum NEMA requirements to be labeled as FR-4. Some grades of FR-4 are superior to others.
T260/T288 values are listed on a laminate manufacturer’s material datasheet. The higher the reported value, the better the performance of the FR-4 when exposed to soldering temperatures. There is one important point to remember: The reported values are generated from pristine and uniform test samples. The values are optimal and do not take the PCB design into consideration.
As soon as you start building a printed circuit board you introduce variables. For example, when you form plated through-holes you have to drill holes. When you drill a hole there shall be some fracturing of the laminate at the hole wall. The fracturing is an imperfection but it’s the result of the printed circuit board manufacturing process. Fracturing is a potential weakness and ultimately a source from where delamination may propagate from. The tested value on the laminate manufacturer's datasheet does not reflect the printed circuit board overall performance. It is an indication for the potential of the FR-4 material, not the manufactured printed circuit board.
The higher the T260/T288 values the better the PCB shall perform when exposed to heat. For conventional eutectic soldering consisting of tin-lead the T260/T288 results are not a critical piece of information to have. For lead-free soldering temperatures it’s an important piece of information to consider. For example, compare two grades of FR-4 from the same laminate manufacturer:
Epoxy System #1:
Dicey cured Tg 170°C (Conventional FR-4)
T260 = 10 minutes
T288 = 2 minutes
Epoxy System #2:
Phenolic cured Tg 170°C (Lead-Free Assembly-Compliant FR-4)
T260 > 60 minutes
T288 = 30 minutes
As you can see, the difference between the two results is dramatic. The T260 test is essentially close to lead-free assembly temperatures. Using a dicey cured epoxy system for lead-free soldering applications is not advisable. The closer you are to lead-free soldering temperatures the faster the epoxy burns away. The phenolic cured epoxy system offers much more in regards to thermal resistance and durability. The phenolic cured epoxy still burns away but at a much slower rate. You'll notice that the T260 result for the phenolic cured laminate is greater than 60 minutes. This only means that the test time exceeded 60 minutes without a failure and the laminate manufacturer stopped the test.
David Duross is an engineering director for NCAB Group USA.
More Columns from Fresh PCB Concepts
Fresh PCB Concepts: Designing for Success at the Rigid-flex Transition AreaFresh PCB Concepts: More Than Compliance—A Human-centered Sustainability Approach
Fresh PCB Concepts: Assembly Challenges with Micro Components and Standard Solder Mask Practices
Fresh PCB Concepts: The Power of a Lunch & Learn for PCB Professionals
Fresh PCB Concepts: Key Considerations for Reliability, Performance, and Compliance in PCBs
Fresh PCB Concepts: Traceability in PCB Design
Fresh PCB Concepts: Tariffs and the Importance of a Diverse Supply Chain
Fresh PCB Concepts: PCB Stackup Strategies—Minimizing Crosstalk and EMI for Signal Integrity