-
- News
- Books
Featured Books
- pcb007 Magazine
Latest Issues
Current IssueInventing the Future with SEL
Two years after launching its state-of-the-art PCB facility, SEL shares lessons in vision, execution, and innovation, plus insights from industry icons and technology leaders shaping the future of PCB fabrication.
Sales: From Pitch to PO
From the first cold call to finally receiving that first purchase order, the July PCB007 Magazine breaks down some critical parts of the sales stack. To up your sales game, read on!
The Hole Truth: Via Integrity in an HDI World
From the drilled hole to registration across multiple sequential lamination cycles, to the quality of your copper plating, via reliability in an HDI world is becoming an ever-greater challenge. This month we look at “The Hole Truth,” from creating the “perfect” via to how you can assure via quality and reliability, the first time, every time.
- Articles
- Columns
- Links
- Media kit
||| MENU - pcb007 Magazine
LPKF Develops Depaneling Process For Insulated Metal Substrates With Metal Cores
August 16, 2021 | LPKFEstimated reading time: 2 minutes
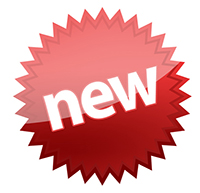
With a laser as the separation tool, cutting can be performed economically and with excellent results on many different types of materials. This now also applies to Insulated Metal Substrates (IMS), or metal core printed circuit boards. LPKF has developed a special solution for depaneling and IMS processing that involves cutting of the printed circuit boards by a powerful laser. The laser brings with it several advantages and is thus more than just an economically attractive alternative to mechanical depaneling processes.
With this solution, printed circuit boards with aluminum, copper, or stainless steel metal cores are cut and depaneled in a specially developed LPKF laser process. The laser source works with process parameters that have been optimized for the specific application. Due to the noncontact nature of the process, no mechanical stresses are induced in the material. The board and the components retain their stability and quality because the material in the vicinity of the cut is minimally affected by the process.
Due to the sensitive applications in which the technically challenging IMS circuit boards are used, the demands on the cutting quality are high. The laser impresses here, too: deposition of metal chips on the material is precluded by the process. It can, however, occur with milling and other mechanical machining methods and can trigger short circuits. Thanks to the LPKF laser technology, this danger is avoided. The reliability of the laser-cut printed circuit boards is just as high as before the cutting process.
Due to the high volumes used in the respective printed circuit board applications, the process speed is an important factor in production. To take this into account, the laser systems from LPKF allow very high effective cutting speeds, which vary depending on the desired cut quality as well as the printed circuit board material thickness and material composition.
Insulated Metal Substrates, also known as metal core printed circuit boards, can be found in a multitude of applications with strict heat dissipation requirements. Foremost among them are power electronics applications. Measuring transducers, transistor arrays, and motor drivers can all be equipped with IMS. Other important applications can be found in the automotive/transport sector, where those substrates are used in headlights/lights, GPS, and power modules. IMS are also indispensable in today’s communications and consumer electronics, for example, in power amplifiers, transmitters, microstrip circuits, motor and voltage regulators, amplifiers, and equalizers.
Compared with conventional printed circuit boards – made of FR4, for example – Insulated Metal Substrates offer a range of advantages for the above-mentioned applications: high thermal conductivity, savings resulting from the reduction in material thickness and the lowered need for heat sinks, and a reduced operating temperature.
Now that LPKF laser technology has made a reliable and fast cutting process available for these IMS circuit boards, the range of applications for them will be extended even further.
Testimonial
"In a year when every marketing dollar mattered, I chose to keep I-Connect007 in our 2025 plan. Their commitment to high-quality, insightful content aligns with Koh Young’s values and helps readers navigate a changing industry. "
Brent Fischthal - Koh YoungSuggested Items
I-Connect007 Editor’s Choice: Five Must-Reads for the Week
08/29/2025 | Nolan Johnson, I-Connect007This week, we bring you Global Electronics Association’s Chris Mitchell’s government relations column on—you guessed it—trade deals. TTM is balancing its facilities between East and West. The Global Electronics Association released July numbers for North American PCB shipments, and the news is good. Meanwhile, the corresponding report for EMS might seem like bad news, but that’s misleading. Be sure to look deeper for the rest of the story. Finally, for a bit space-science palate cleansing, I’m sharing news of the latest launch of NASA’s X-37B.
ICZOOM Launches PCB & SMT Services to Strengthen One-Stop Electronics Industry Solution at IIC Shenzhen 2025
08/28/2025 | PRNewswireICZOOM Group Inc., a B2B electronic component products e-commerce platform, successfully exhibited at the 2025 International Integrated Circuit & Component Exhibition and Conference (IIC Shenzhen 2025) held from August 26 to 28 at the Shenzhen Convention & Exhibition Center in Futian District.
AT&S Fuels Future Innovation with 'Young Wilds' Program
08/28/2025 | AT&SToday’s ideas are tomorrow’s innovations: Following a successful debut in the financial year 2024/25, the “Young Wilds” program offers ambitious young professionals at AT&S the opportunity to take on responsibility and accelerate their personal and professional growth.
North American PCB Industry Shipments Up 20.7 Percent in July
08/27/2025 | Global Electronics AssociationThe Global Electronics Association announced today the July 2025 findings from its North American Printed Circuit Board (PCB) Statistical Program. The book-to-bill ratio stands at 1.00. Total North American PCB shipments in July 2025 were up 20.7% compared to the same month last year.
Mastering PCB Floor Planning
08/28/2025 | Stephen V. Chavez, Siemens EDAPlacement of PCB components is far more than just fitting components onto a board. It’s a strategic and critical foundational step, often called “floor planning,” that profoundly impacts the board’s performance, reliability, manufacturability, and cost. Floor planning ties into the solvability perspective, with performance and manufacturability being the other two competing perspectives for addressing and achieving success in PCB design.