-
- News
- Books
Featured Books
- design007 Magazine
Latest Issues
Current IssueProper Floor Planning
Floor planning decisions can make or break performance, manufacturability, and timelines. This month’s contributors weigh in with their best practices for proper floor planning and specific strategies to get it right.
Showing Some Constraint
A strong design constraint strategy carefully balances a wide range of electrical and manufacturing trade-offs. This month, we explore the key requirements, common challenges, and best practices behind building an effective constraint strategy.
All About That Route
Most designers favor manual routing, but today's interactive autorouters may be changing designers' minds by allowing users more direct control. In this issue, our expert contributors discuss a variety of manual and autorouting strategies.
- Articles
- Columns
- Links
- Media kit
||| MENU - design007 Magazine
Estimated reading time: 4 minutes
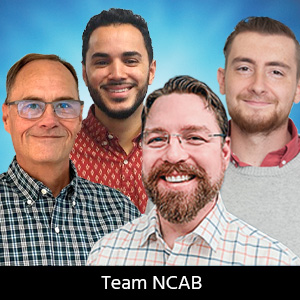
Fresh PCB Concepts: Holy Cow, What a Lead Time
It's summer and we are adapting to our second COVID summer. However, things are most definitely a bit different these days. Recently I got an order, just like every day. The designer had spent the last three weeks completing the design and got it approved for order placement. The next step in the flow is when the purchaser spends a few days to get prices right, and then the order can be placed.
Anything Wrong With This?
No, it’s business as usual to make sure the design is correct, and prices are negotiated to save money. This is an everyday operation in this industry. However, in a normal year, with normal material lead times, and without escalating material prices, that is how it works.
Today, Things Are a Bit Different
Let me elaborate on an example from the last few weeks. I was contacted by a designer requesting a stackup for an eight-layer PCB. This was a quite standard stackup that could work for most eight-layer designs, meaning that he would need impedance per design, but not controlled, no microvias, and no critical thickness requirements.
But this designer always requests a stackup including the exact materials used, to match his lines to the stackup. Basically, this stackup works for most eight-layer designs, even for those with impedance lines. As long as we don’t change the track, gap, and stackup, it will work. After this, the designer spends two to three weeks on the design. After one week he was more or less done, but had the design sent for verification before he closed it and submitted it to procurement.
What About the Stackup and Changes?
The purchaser received the Gerber files and submitted his request for quotation to two or three of his most trusted PCB suppliers. He got the first quotation within eight hours but decided to wait another two days to make sure he had the best price. Order placed as usual, but now things started to happen.
The PCB factory replied that the material supplier for this brand and type suddenly had eight-week lead time. He sent back an engineering query for alternative materials that would keep the stackup and those designed impedance lines. Designer rejected; the stackup had been approved by the end customer with no chance to change it now. So, what happens next? The EQ is sent back to the PCB supplier, with the result of a five- to six-week increased lead time compared to the original offer.
What Can We Learn?
First, in a normal situation this is not necessarily an issue, but today with increased and less predictable material lead times, and on top of unpredictable material prices, we need to adapt to the situation and be smart.
But How?
First, make sure the stackup and material selection is as open as possible.
- Don’t lock your stackup to one material brand or type of material. Allow for factory standard materials to be used.
- Try to use IPC 4101 slash sheet numbers, unless you have special needs.
- If you have impedance lines designed in, make sure to describe what you need. The factory will in 99% of the cases be able to tune track and gap to meet their standard materials.
- If you ask for a factory stackup, make sure you allow standard materials to be used.
- Also consider releasing the stackup for material to be allocated, or even placing a material preorder.
By these actions, you can simplify the process of approving the design, and, as we currently face an unpredictable material situation, avoid sudden increased material lead times from when the stackup is approved, and up to order placement. Remember that the PCB factory doesn't order material before all EQs have been closed, adding on another two to seven days.
Is Price the Key to Success?
We all know price matters when procuring printed circuits. Some buyers only target on price, benchmarking, and swapping suppliers more often than the Kardashians shoot selfies. Long term relationships might sound boring, but also offer predictability, priority, and dual source if needed. Just to specify, I am only talking about relationships with your PCB supplier.
In a market like today, a few pennies saved can be at a high cost. My advice after decades in the industry and facing the current challenges daily:
- Place the material allocation order as early as possible—as soon as the stackup is fixed.
- Don’t start negotiation prices and lead times the day you expect to place the order; it is too late. Not even the same week.
- Select a trusted supplier that accepts material allocation on orders and stay with them.
- Work on long time trust and be predictable within the nature of your business.
Be Realistic
The last thing I want to mention is the need for a PCB supplier that has skills and knowledge to guide you in the right direction. As in all matters of life, procuring printed circuits is also about finding solutions. We aim to guide our customers in a material selection, available within reasonable time. Finding solutions that combine function and availability is vital.
Today, the best direction is not necessarily to meet all the customers' needs, finding special materials, or processes, but maybe all of this in combination with a realistic view of what can be done, within a reasonable time.
Until last autumn, we did not have this understanding. Today, it is vital to reach the market in time. My senior technical advisor colleagues and I aim to maintain the attitude, “Nothing is impossible, we will find a solution.”
That is still true, and in 90% of the cases it's possible. However, “the material availability ghost” is haunting the industry every day, which means we also need to use all our skills and knowledge about material lead times to find good solutions for the customers, and maybe most importantly, realistic, and reliable solutions.
This column originally appeared in the August 2021 issue of PCB007 Magazine.
More Columns from Fresh PCB Concepts
Fresh PCB Concepts: Designing for Success at the Rigid-flex Transition AreaFresh PCB Concepts: More Than Compliance—A Human-centered Sustainability Approach
Fresh PCB Concepts: Assembly Challenges with Micro Components and Standard Solder Mask Practices
Fresh PCB Concepts: The Power of a Lunch & Learn for PCB Professionals
Fresh PCB Concepts: Key Considerations for Reliability, Performance, and Compliance in PCBs
Fresh PCB Concepts: Traceability in PCB Design
Fresh PCB Concepts: Tariffs and the Importance of a Diverse Supply Chain
Fresh PCB Concepts: PCB Stackup Strategies—Minimizing Crosstalk and EMI for Signal Integrity