-
- News
- Books
Featured Books
- smt007 Magazine
Latest Issues
Current IssueSupply Chain Strategies
A successful brand is built on strong customer relationships—anchored by a well-orchestrated supply chain at its core. This month, we look at how managing your supply chain directly influences customer perception.
What's Your Sweet Spot?
Are you in a niche that’s growing or shrinking? Is it time to reassess and refocus? We spotlight companies thriving by redefining or reinforcing their niche. What are their insights?
Moving Forward With Confidence
In this issue, we focus on sales and quoting, workforce training, new IPC leadership in the U.S. and Canada, the effects of tariffs, CFX standards, and much more—all designed to provide perspective as you move through the cloud bank of today's shifting economic market.
- Articles
- Columns
- Links
- Media kit
||| MENU - smt007 Magazine
Estimated reading time: 3 minutes
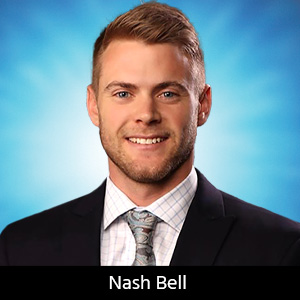
Knocking Down the Bone Pile: X-ray Imaging and BGA Rework
X-ray imaging prior to the removal of a BGA for rework will help the rework technician point out potential issues which may be challenges to successfully removing and replacing the BGA. X-ray imaging of the actual BGA location, as well as the surrounding area, is used to confirm rework challenges such as the proximity of neighboring devices, starved solder joints, and solder balls causing electrical shorts. These images can point to potential root causes for the BGA rework including broken bond wires, or the popcorning or delamination of the package. Furthermore, soldering anomalies such as head-in-pillow or graping defects, which may be causing intermittent connections, can be the cause of the failure. Devices on the opposite side of the BGA location will determine potential problem areas due to heat effects of the rework process.
For example, if a BGA is underneath a shield, X-ray will help determine the location of the BGA and the neighboring devices, as well as the margins for getting a nozzle into the rework location (if using a hot air rework reflow source). X-ray imaging will also provide clues to the physical board problems such as lifted pads or solder that has wicked down the dog bone of the PCB due to mask damage, as well as other anomalies.
Not only does X-ray imaging provide some clues prior to rework of some of the challenges that may lie ahead, but it also confirms that the rework was completed correctly. After visual and endoscopic inspection has been completed, the BGA rework location is inspected by manipulating the controls of the X-ray to where the component of interest is seen in a large field of view. The technician then manipulates the X-ray system to where numerous solder balls can be seen on the screen as the rows are scanned back and forth. The technician reviews the overall ball sizes to make sure they are consistent in size and shape.
Anomalies such as small balls (Figure 1), oversized balls (Figure 2), and misshapen balls all will be caught by an experienced X-ray operator. Especially critical to observe are the corner solder ball locations. If these locations are full and round, then as a rule the overall ball collapse is sufficient. Smaller-sized balls may be a direct result of solder wetting down a dog bone pattern where the mask has been damaged, or in cases where a thermal via has wicked the solder down into the via hole. Oversized balls may be a result of neighboring balls having their solder squirt over to a neighboring ball location.
Obvious anomalies like solder shorts, missing balls, or misshapen balls will also be picked out during this part of the investigation. At this field of view the technician will next investigate areas around the device of interest. Skewed components, solder balls, or handling damage can all be picked up by examining the X-ray image. Solder may have “squirted” out of neighboring locations; such is the case when the board has been conformally coated or neighboring or mirrored devices that are underfilled also show up clearly on X-ray images. Once this larger field of view inspection has been successfully completed, the BGA technician zooms in to review details about the solder balls and their collapse. The technician is looking for misshapen balls, smaller or larger balls, a high voiding percentage, and solder shorts as well as numerous other anomalies. X-ray imaging really is a necessity to “see” these defects and anomalies after BGA replacement.
X-ray inspection of reworked BGAs prior to the rework operation, and both far and near field analysis of the X-ray images, are important to confirm that the BGA rework process has yielded success. Without the use of X-ray imaging, it is very difficult to confirm that the inspection criteria have been satisfied.
Resources
IPC-7095 Design and Assembly Process Implementation for BGAs
IPC-A-610H Acceptability of Printed Wiring Boards
This column originally appeared in the September 2021 issue of SMT007 Magazine.
More Columns from Knocking Down the Bone Pile
Knocking Down the Bone Pile: Addressing End-of-life Component Solderability Issues, Part 4Knocking Down the Bone Pile: Tin Whisker Mitigation in Aerospace Applications, Part 3
Knocking Down the Bone Pile: Gold Mitigation for Class 2 Electronics
Knocking Down the Bone Pile: Basics of Component Lead Tinning
Knocking Down the Bone Pile: Package on Package Rework—Skill Required
Knocking Down the Bone Pile: 2023’s Top Challenges in BGA Rework
Knocking Down the Bone Pile: Eliminating Solder Balls in Hand Soldering
Knocking Down the Bone Pile: Opening a Trace on the Surface of a PCB