-
- News
- Books
Featured Books
- design007 Magazine
Latest Issues
Current IssueProper Floor Planning
Floor planning decisions can make or break performance, manufacturability, and timelines. This month’s contributors weigh in with their best practices for proper floor planning and specific strategies to get it right.
Showing Some Constraint
A strong design constraint strategy carefully balances a wide range of electrical and manufacturing trade-offs. This month, we explore the key requirements, common challenges, and best practices behind building an effective constraint strategy.
All About That Route
Most designers favor manual routing, but today's interactive autorouters may be changing designers' minds by allowing users more direct control. In this issue, our expert contributors discuss a variety of manual and autorouting strategies.
- Articles
- Columns
- Links
- Media kit
||| MENU - design007 Magazine
Estimated reading time: 5 minutes
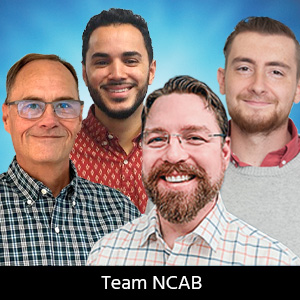
Fresh PCB Concepts: HDI PCBs for New Kids in the Industry
I have been working with NCAB Group for three years, first as an intern while I was in school and now as a full-time quote engineer. When I began I had no experience with PCBs. Since then, I have learned so much working with our customers’ PCB designs. Although I am still new to the game, I would like to share the basic fundamentals and design features of my favorite type of PCB—high-density interconnect, or HDI.
Let’s begin with the reasons why HDI PCBs are my favorite to work on. They’re complex; that’s what’s fun and keeps things interesting. Also, being a Gen Z-er, I’ve learned HDI is found in many of the products that I use every day, like my iPhone. An HDI PCB is going to have denser circuitry, more drill count, blind and/or buried vias, and is built to fit as much circuitry as possible in as small a space as possible. I will explain some of these features later.
With increased density we can accommodate smaller and finer pitched components. Not only do we have more functions with HDI, but also more advanced functions. When creating these designs for smaller PCBs, in many cases, the board also must be lighter, thinner, and faster. This puts a greater demand on the design and production processes to get it right.
With a smaller and tighter design, we are going to see finer traces and narrower spaces. Plated through-holes (PTH) are not enough to accommodate an HDI PCB. We will need laser drilled microvias and buried vias that are smaller, and connect selected layers, rather than going through the whole PCB stackup. To achieve this, we will need thinner prepregs/CCL than in traditional multilayer products. These thinner materials place a greater demand on the factory, particularly with the current material shortage in the industry. However, with the introduction of microvias we are also increasing signal integrity.
Since these designs are more challenging for the factories, we must have good specifications. NCAB uses the internationally known IPC standards as our benchmarks for both input on acceptance criteria, and for some of the design fundamentals. This provides us with a common language while working with agreed and known specifications. This will enable us to get what we specify, helps in factory selection, improves the comparisons for product and total cost, helps to secure the correct quality level, and reduces the risk of misinterpretation.
IPC-6012D defines HDI as a design with an average of 20 electrical connections/cm2 on both sides of the printed board. These designs typically have vias ? 150 µm / 0.006 in, conductor width and spaces ? 100 µm / 0.004 in, vias in SMT pads, and/or where microvias are employed.
According to the definition within both IPC-6012D and IPC-T-50M a microvia is a blind structure with a maximum aspect ratio (a measure of ratio between the depth of the hole to its width) of 1:1, terminating on a target land, with a total depth of no more than 0.25mm / 0.001 in. when measured from the structure’s capture land foil to the target land.
Within IPC-2226 there is more than one type of microvia structure:
- IPC-2226 Type I structures are those that contain a single microvia layer on either one or both sides of core. It uses both plated microvia and PTH for interconnection. This structure employs only blind via holes and does not employ buried vias.
- IPC-2226 Type II structures are a little more complex. There is more drilling, more plating and more lamination/bonding processes. Type II structures are similar to Type I in that they contain just a single microvia layer on either one or both sides of core. It also uses both plated microvia and PTH for interconnection. Yet unlike Type I these structures employ both blind and buried via holes.
- IPC-2226 Type III structures are fairly complex and more challenging. Drilling and plating and bonding is all increasing and each step brings more difficulties including registration, material movement and increased density. Type III structures contain at least two layers of microvia on either one or both sides of core. As with Type II, it also uses both plated microvia and PTH for interconnection as well as both blind and buried vias.
These impressive designs have various impacts on price. Here is a rough guide on how the cost can be impacted the more complex we get.
Figure 1: This design is based on standard 10-layer multilayer technology.
This design is based on standard 10-layer multilayer technology. Nothing special, just PTH and assuming standard track and gap within capabilities. Let’s use this as our base price for comparison.
Figure 2: The impact of being built as a 10-layer type I HDI.
Now we look at the impact of this being built as a 10-layer Type I HDI. Adding two layers of microvia to the board will require more drilling, this time with laser. This increases the price by 40–70% from the base price. The range considers varying batch sizes and lead times, plus different factories and different pricing levels.
Figure 3: A Type II 10-layer structure with a buried via.
Now we go to a Type II 10-layer structure with a buried via. This means more drilling, more plating and more lamination steps. More processes equals more times around the factory and a longer process with more steps. This increases the base price 80–120%. Impact = 80–120%.
Figure 4: A Type III 10-layer structure with a blind and buried via.
Now we go to a Type III 10-layer structure with a blind and buried via and containing at least two layers of microvia on either one or both sides of core. This means even more drilling (4), more plating (3), more lamination (3) steps. This will increase the base price by 180–200%.
This is really a generalization and a rough guide. It’s important to note this cost comparison does not take into account any reduction in layer count or reduction in the size of the PCB, key factors that HDI methodologies also deliver. Each design will be different and the greater the complexity then the greater the impact on these features and cost.
This provides an indication of how complex these boards are to build, the impacts on cost and why it is very important to select the right partner that can do this with the right yields and the right reliability and quality, to get it right from the start.
Nicholas Marks is a quote engineer for NCAB Group.
More Columns from Fresh PCB Concepts
Fresh PCB Concepts: Designing for Success at the Rigid-flex Transition AreaFresh PCB Concepts: More Than Compliance—A Human-centered Sustainability Approach
Fresh PCB Concepts: Assembly Challenges with Micro Components and Standard Solder Mask Practices
Fresh PCB Concepts: The Power of a Lunch & Learn for PCB Professionals
Fresh PCB Concepts: Key Considerations for Reliability, Performance, and Compliance in PCBs
Fresh PCB Concepts: Traceability in PCB Design
Fresh PCB Concepts: Tariffs and the Importance of a Diverse Supply Chain
Fresh PCB Concepts: PCB Stackup Strategies—Minimizing Crosstalk and EMI for Signal Integrity