-
- News
- Books
Featured Books
- design007 Magazine
Latest Issues
Current IssueProper Floor Planning
Floor planning decisions can make or break performance, manufacturability, and timelines. This month’s contributors weigh in with their best practices for proper floor planning and specific strategies to get it right.
Showing Some Constraint
A strong design constraint strategy carefully balances a wide range of electrical and manufacturing trade-offs. This month, we explore the key requirements, common challenges, and best practices behind building an effective constraint strategy.
All About That Route
Most designers favor manual routing, but today's interactive autorouters may be changing designers' minds by allowing users more direct control. In this issue, our expert contributors discuss a variety of manual and autorouting strategies.
- Articles
- Columns
- Links
- Media kit
||| MENU - design007 Magazine
Estimated reading time: 5 minutes
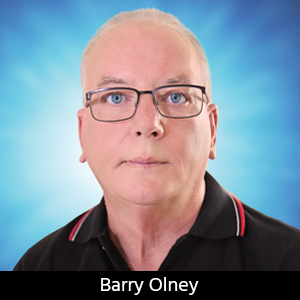
Beyond Design: The Impact of No-Clean Flux Residue on Signal Integrity
Most electronic products today are assembled using the no-clean soldering process. The need for no-clean solder pastes emerged in response to legislation against the use of ozone-depleting chemicals, and the appeal of removing the costly flux cleaning operations in the assembly of PCBs. However, the impact of no-clean flux residue on signal integrity is a concern for many high-frequency products such as 5G and other high-speed communications. No-clean flux residue can lower the characteristic impedance of an interconnect, create an alternative path to the signal, and degrade the signal integrity performance, especially at high frequency.
With the predominance of no-clean soldering processes and the ever-decreasing component standoff, the electronics industry has had to consider the reliability of what may be partially activated flux residues under component bodies. Similarly, questions have also arisen about the reliability of flux residues resulting from the reflow of no-clean solder pastes that are entrapped under RF shields, where the escape of the volatile ingredients of the flux is greatly hindered. The residue left behind is generally clear in appearance and tends to flow uniformly away from the joint. And due to the small quantity of solids, this residue is extremely thin in most places. This allows for a camouflage effect; upon visual inspection, the joint looks to be free of virtually all residues.
Little information exists about the effects of flux residues on electrical circuit functionality. But, with requirements for increased rise times and higher operating frequencies, there is particular concern about the magnitude of such effects on high-frequency, digital, microwave, and RF circuits. The effects of flux residues are measured in terms of their effective dielectric properties on microstrip structures. In this way, the change in microstrip circuit performance caused by the presence of flux residues can be deduced.
Microstrip resonator structures are widely used for determining the dielectric constant of substrate materials at high frequency. The results are applied to the design of controlled impedance interconnects, microwave, and RF circuit elements. By measuring the response of resonators that have been covered with and without no-clean flux, the change in effective dielectric constant (Dk) and dielectric dissipation (Df) caused by the presence of residues can be deduced and incorporated in the design.
The frequency response of a typical T-resonator consists of a series of resonant dips (Figure 1), measured at the input port S12, the first of which occurs when the stub length (l stub) equals one-quarter wavelength (when the impedance of the stub tends towards zero). Subsequent resonant dips occur at the odd harmonics of the fundamental frequency. The resonant frequency of the T-resonator depends on the length of the stub (l stub) and the effective dielectric constant (?eff)—where ?eff is a combination of the material Dk and that of the flux (?flux). The presence of flux residue reduces the resonant frequency over the entire bandwidth but has its greatest impact at higher harmonics.
When the flux residue is deposited around a microstrip signal conductor, it also contributes to the effective dielectric constant of the structure. Figure 2 illustrates the results for different values of thickness and dielectric constant of the flux residue layers. It can be clearly seen that increased values of ?flux also increase the effective dielectric constant.
The dielectric constant of a laminate is an important electrical property needed to accurately design a target characteristic impedance. It will affect the characteristic impedance of a transmission line and the propagation delay of the line. The strength and quality of the signal are augmented by a low dielectric constant of the materials. Low-loss and ultra low-loss materials, while being a bit more costly, can dramatically improve the propagation and quality of the signal at high frequencies. However, the presence of flux residue tends to increase the dielectric constant thereby reducing the signal quality.
Figure 3 shows how the change in flux residue affects the impedance of the microstrip trace. For a 15-µm residue, the impedance can drop by about 2.8 ohms, depending on the dielectric constant of the particular flux used. The impact of flux residue on microstrip impedance is not very large. However, the tolerance for controlled impedance boards is now regularly set at ±5%, making the use of no-clean fluxes borderline for high-density interconnects (HDI).
Changes in a PCB material’s dielectric constant can adversely affect the performance of broadband high-frequency analog circuits as well as high-speed digital circuits, because it will change the impedances of transmission lines in unexpected ways. In particular, these undesirable changes in dielectric constant and impedance result in distortion to the higher-order harmonics making up a high-speed digital signal, with loss of digital signal integrity. In general, PCB materials with low and stable Dk values (with frequency and temperature) will support high-speed digital circuits with low distortion of the higher-order harmonic signal components2.
Generally, we try to use low-Dk materials in the construction of HDI boards, which contributes to reduced interconnect delays and loss in the circuit. Consequently, an effective higher Dk caused by the no-clean flux is detrimental to high-speed design. Also, keep in mind that flux tends to congregate in the inner corners of right-angle bends which will add to this issue—another reason not to use right-angle bends when routing. RF and microwave signal interconnects are typically routed on the outer microstrip layer. However, if critical digital signals are routed embedded between the planes, then this issue can be totally avoided.
Key Points
- The majority of electronic products today are assembled using the no-clean soldering process.
- No-clean flux residue can lower the characteristic impedance of an interconnect, creating an alternative path to the signal.
- One should consider the reliability of partially activated flux residues under component bodies and RF shields.
- The effects of flux residues are measured in terms of their effective dielectric properties on microstrip structures.
- Microstrip resonator structures are widely used for determining the dielectric constant of substrate materials at high frequency.
- The presence of flux residue reduces the resonant frequency over the entire bandwidth but has its greatest impact at higher harmonics.
- When the flux residue is deposited around a microstrip signal conductor it also contributes to the effective dielectric constant of the structure.
- The dielectric constant of a laminate affects the characteristic impedance of a transmission line and the propagation delay of the line.
- Low-loss materials can dramatically improve the propagation and quality of the signal at high frequencies.
- The presence of flux residue tends to increase the dielectric constant, reducing the signal quality.
- Unexpected changes in dielectric constant and impedance result in distortion to the higher-order harmonics making up a high-speed digital signal, with loss of digital signal integrity.
References
- RF Characterization of No-clean Solder Flux Residues, Maeve Duffy, et al.
- Selecting PCB Materials for High-Speed Digital Circuits, John Coonrod, Rogers Corp., Microwave Journal.
This column originally appeared in the October 2021 issue of Design007 Magazine.
More Columns from Beyond Design
Beyond Design: Effective Floor Planning StrategiesBeyond Design: Refining Design Constraints
Beyond Design: The Metamorphosis of the PCB Router
Beyond Design: Radiation and Interference Coupling
Beyond Design: Key SI Considerations for High-speed PCB Design
Beyond Design: Electro-optical Circuit Boards
Beyond Design: AI-driven Inverse Stackup Optimization
Beyond Design: High-speed Rules of Thumb