-
- News
- Books
Featured Books
- design007 Magazine
Latest Issues
Current IssueAdvanced Packaging and Stackup Design
This month, our expert contributors discuss the impact of advanced packaging on stackup design—from SI and DFM challenges through the variety of material tradeoffs that designers must contend with in HDI and UHDI.
Rules of Thumb
This month, we delve into rules of thumb—which ones work, which ones should be avoided. Rules of thumb are everywhere, but there may be hundreds of rules of thumb for PCB design. How do we separate the wheat from the chaff, so to speak?
Partial HDI
Our expert contributors provide a complete, detailed view of partial HDI this month. Most experienced PCB designers can start using this approach right away, but you need to know these tips, tricks and techniques first.
- Articles
- Columns
Search Console
- Links
- Media kit
||| MENU - design007 Magazine
Peters: LED Curing Perfected Thanks to DELO
November 19, 2021 | PetersEstimated reading time: 2 minutes
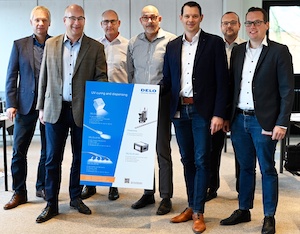
The cooperation with the equipment and material manufacturer DELO has proven successful and is renewed for another year. DELO provides Peters with a system for UV LED curing consisting of the DELOLUX 202 lamp head and the DELOLUX pilot. Through homogeneous exposure, the UV flood lamp from DELO enables curing within seconds of the coating systems used in LED technology. In the Peters laboratory, the ELPEGUARD® thick film coating Twin-Cure® DSL 1602 FLZ/400 is in the focus.
“The DELO device is an important factor in the Peters showroom, not only for the processing of our conformal coatings, but also for the further development of future technologies such as inkjet solder resists for digital manufacturing," says Stefan Schröder, Conformal Coatings Product Manager at Peters in charge of the DELO project. From Peters' point of view, the future belongs to LED curing in many respects. All ink systems chosen here are solvent-free; this application consumes far less energy than conventional systems. "And there is less heat stress," emphasises Dirk Kall, Group Head of Research and Development in the Peters laboratories for the ELPEGUARD® and ELPECAST® product lines.
Peters and DELO agree that the trend in the industry is moving in this direction - including the factors of energy efficiency, environmental protection and temperature sensitivity. "Peters is responding to this trend by further developing their conformal coating systems," says Johannes Tekath, Laboratory Manager "Research and Development" at the Peters headquarters in Kempen. He says that not only research in this field is exciting, but also dealing with special technologies, printed circuit board systems and inkjet technology, a field where Peters has a proven expert in their ranks by project manager Kevin Poth.
For Markus Wieler, Global Business Development Manager, the energy balance factor is decisive for the Peters/DELO model. "With a flexible equipment manufacturer at our side, we are confident that we will successfully promote further ink systems at this level," says the ink engineer. Via this tandem between the Ammersee region where DELO is located and Peters' home in the Lower Rhine Area, the conformal coating is state of the art with regard to LED technology, he says.
The three-man DELO delegation took advantage of this visit to Peters to present their latest developments in appliance technology and to continue to propose themselves as a flexible partner. The aim of the two owner-managed family companies is to meet customer requirements and further elaborate the competence axis created so far.
Suggested Items
Book Excerpt: The Printed Circuit Assembler’s Guide to... Low-Temperature Soldering, Vol. 2, Chapter 5
12/23/2024 | I-Connect007 Editorial TeamChapter 5 introduces the advantages of using low-temperature soldering for through-hole components, including cost efficiency, reliability improvement, and reduced warpage. Also covered: the evaluation of different fluxes and the performance of HRL3 in wave soldering and selective soldering processes.
Overview of Soldering Systems With Vacuum
12/18/2024 | Dr. Paul Wild, Rehm Thermal Systems GmbHWhen soldering electronic assemblies, the focus of the vacuum application is on the removal of volatile substances from the solder joints and the associated reduction of pore formation. Particularly in the thermal management of power electronics components, pores can cause so-called hotspots with higher temperatures due to their poor heat conduction. These hotspots can lead to overheating of the components on the one hand and to thermally induced destruction of the solder structure on the other.
I-Connect007 Editor’s Choice: Five Must-Reads for the Week
12/13/2024 | Andy Shaughnessy, I-Connect007This week, Peter Tranitz discusses the upcoming Pan-European Electronics Design Conference, set for Jan. 29-30 in Vienna, Austria. Pete Starkey brings us a review of the most recent EIPC Technical Snapshot webinar, which featured a global PCB maker update by Dr. Hayao Nakahara. Don't miss our interview with Manfred Huschka, who explains how companies can begin their own China Plus One plan. Stan Farnsworth breaks down photonic soldering and discusses its use in soldering materials that are not typically compatible. I also enjoyed Dan Beaulieu’s discussion on the value of consistency, and why just showing up for work is half the battle, especially in an inconsistent, evolving industry like ours.
Advancing Photonic Soldering
12/11/2024 | Nolan Johnson, SMT007 MagazineStan Farnsworth, director of customer satisfaction at PulseForge, discusses the advancements in photonic soldering that highlight its energy efficiency and versatility. Over the past two years, the company has refined its applications for flexible substrates and energy reduction, finding that photonic soldering allows the processing of materials that typically aren’t thermally compatible and offers significant energy savings compared to traditional methods.
Indium Introduces New ROL0 and Halogen-free Flux-cored Wire
12/11/2024 | Indium CorporationIndium Corporation announced the global availability of CW-807RS, a new high-reliability, halide- and halogen-free flux-cored wire that improves wetting speeds and cycle times for electronics assembly and robot soldering applications.