-
- News
- Books
Featured Books
- pcb007 Magazine
Latest Issues
Current IssueSales: From Pitch to PO
From the first cold call to finally receiving that first purchase order, the July PCB007 Magazine breaks down some critical parts of the sales stack. To up your sales game, read on!
The Hole Truth: Via Integrity in an HDI World
From the drilled hole to registration across multiple sequential lamination cycles, to the quality of your copper plating, via reliability in an HDI world is becoming an ever-greater challenge. This month we look at “The Hole Truth,” from creating the “perfect” via to how you can assure via quality and reliability, the first time, every time.
In Pursuit of Perfection: Defect Reduction
For bare PCB board fabrication, defect reduction is a critical aspect of a company's bottom line profitability. In this issue, we examine how imaging, etching, and plating processes can provide information and insight into reducing defects and increasing yields.
- Articles
- Columns
- Links
- Media kit
||| MENU - pcb007 Magazine
Agfa Taking Leap to Digital Platform
December 13, 2021 | Pete Starkey, I-Connect007Estimated reading time: 11 minutes
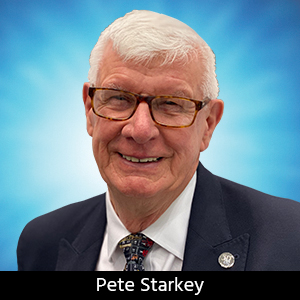
I-Connect007 Technical Editor Pete Starkey spoke with Agfa Business Unit Manager Frank Louwet ahead of last month’s productronica show in Europe. They discuss the company’s desire to reduce its carbon footprint and the benefits of this change, particularly with a move to digital inkjet printing, and describes some of the company’s newest products.
Pete Starkey: I’m speaking with Frank Louwet, the business unit manager of Electronic Print at Agfa in Belgium. Frank, it’s good to speak with you again. I’m sure a lot has happened since we met at the last productronica.
Frank Louwet: Thank you, Pete. Indeed, quite a few things have happened during that time.
Starkey: Just looking back, we talked about developments in inkjet inks for PCB applications, especially solder masks, together with marking inks for flexible and rigid circuits, etch resists for chemical milling, and plating resists for selective ENIG plating. We also talked about flexible solder masks and conductive inks for printed electronics technologies. You clearly had already developed a very broad product portfolio and it’s good to see that your inkjet inks have been validated by a range of leading equipment manufacturers. I like your vendor-neutral strategy.
We discussed the benefits of inkjet techniques for solder mask, economic, environmental, and particularly, technical, in terms of putting ink exactly where you want it, in the thickness that you want, not putting it where you don’t want it, especially in high-frequency applications like 5G where it could cause signal loss.
Frank, you’ve been a leader in the imaging business for a long time, and you’re certainly one of the drivers of the analog to digital transformation, staying ahead of the technology curve in 3D printing and additive manufacturing. What are your comments?
Louwet: Agfa is known in this industry for the analog photo-tooling film. It is thanks to our reliable product quality and our service supply that today we have gained the leading position as the supplier for this PCB film. On the other hand, Agfa is globally recognized as an expert in inkjet inks for the graphics industry. As you mentioned, the combination of these two strengths allows Agfa to become the trusted partner for the PCB manufacturers to go from the analog to the digital platform.
Our claim is “Grow your business, not your footprint.” By going digital you can grow your business without having to increase your waste materials, your processing chemicals, your water, and even your floor space. Moving to the digital platform is a benefit for the PCB industry. Cost pressure and the need for higher flexibility is motivating PCB manufacturers to actively consider digital inkjet printing.
The advantage of having your CAD design and almost printing it directly reduces the set-up time. You also need less infrastructure, as it is an additive process. Inkjet eliminates the waste of material and it’s no doubt more environmentally friendly than classical analog processing. Agfa started its digital product portfolio early on with marking and legend inks, as the entry into the digital platform.
Starkey: Do you think that the industry has turned over now to digital techniques for marking inks and legend inks. Has the old screen-printing technology been pretty well superseded now?
Louwet: Yes, that is correct although it depends on the region. When looking at legend or marking inks, the big benefit of digital is that every print can be different and PCB boards today need to be traced.
Starkey: Oh yes, of course, you can serialize as well.
Louwet: With the conventional process, serialization had to be done in two steps: with laser engraving or whatever other technique. This can now be done in one step; you just inkjet print the marking in combination with that same marking ink for serialization. This demonstrates the advantage and benefit of digital printing over the analog process.
Indeed, if you look at the region, the U.S. and Europe are still on the level of the smaller machines. But if you compare that to China, that is where you see a boost of this digital printing technology. There are a few printer integrators that bring mass production machines for legend printing with up to 15 heads and more in one machine at printing speeds that are faster than screen printing. So, certainly in China, if people invest in a technology for legend printing, it will be inkjet and not the classical process anymore.
From Agfa’s side, we do not have too many new products there. We already had a portfolio for rigid and flex, in different colors. We have brought some newer generations that are improvements of ink, for example, with respect to adhesion or curing, based on customer feedback. That’s what normally happens, but basically the portfolio did not change. We had a recent update of the DiPaMAT Flex white ink.
Starkey: When we spoke the last time, you already had established etch resist inks, particularly for the chemical milling and metal decoration side, but these were acid resists where people would be using ferric or cupric-type etchants. So, you can now offer alkaline etch resists?
Louwet: For the etch resist, you can print on metal in general such as stainless steel, but also aluminum or copper. The application is chemical milling, metal decoration or PCB and either acid or alkaline etching inks are used. Then you have the alkaline stripping. In that respect, we have enlarged our portfolio. We now have a version that strips in flakes and one that dissolves. The inks we currently have in portfolio are for acid etching but we have an ink for alkaline etching in development.
Besides the chemical etching, metal brushing can be an alternative for metal decoration. We have recently added a new ink for this application to our portfolio.
Starkey: We tend to focus our attention on the printed circuit board side of the industry, but I think we are conscious that there’s a very big industry in metal finishing, metal etching, and metal decoration. Provided we keep aware of that side of the industry, we can get some quite useful ideas and useful feedback, which we can apply in the PCB industry.
Louwet: A new development in etch resists, although not really an etch resist, is the plating resist. PCB manufacturers have multiple technologies to finish their boards, for example, OSP, hot-air solder leveling, ENIG, immersion Sn, and so on. In the past, mostly the HASL process was used, but more and more, ENIG is applied because of performance and because it’s more environmentally friendly. But ENIG is an expensive process. Some customers want to use ENIG in combination with something else, like OSP. For that, Agfa developed a plating resist called DiPaMAT PR01. It is an inkjet ink, UV cured—you do not need a thermal cure—and it resists the ENIG process. The ink can be stripped after that process.
Starkey: The ENIG process is particularly chemically aggressive. You must have a very resistant resist and then, to be able to remove that resist once the job is done without damaging the substrate or the other finishes, must be a very well-balanced chemical exercise.
Louwet: We already touched that subject last time when we discussed, and indeed, as you say, it is really a subtle equilibrium between resisting in the ENIG and not being stripped; or the other way around, not resisting in ENIG and easy to strip. It took us quite some time to find that optimum, but we are now field testing it at a few customers. It’s not commercial yet, but it’s promising and coming soon.
Then, of course, we have the Holy Grail, the solder mask. I think solder mask is really an example where all the benefits of digital inkjet printing come together.
Like you said, you print the ink only where you need it. A lot of progress has been made from the side of the printer integrator. During the pandemic, the commercial slowdown in the market freed up time to optimize the printing technology, the printing algorithms, to put down the ink where it’s needed, to have the narrow lines, the straight lines, the solder dams, and so on. There has been a lot of progress and at productronica several of the printer integrators are able to show these big advancements. You can witness that going to print heads with smaller droplet size improves the resolution of the printing. Printer integrators are very confident that with the state of the art they can do what is needed for the solder mask industry.
Starkey: I think you need to see examples of what can be and what has been achieved to really appreciate it. Coming from a traditional solder mask background, you need to clear away all your previous knowledge and take a completely fresh look at what can be achieved. As I said earlier, you’re putting it where you want it, in the thickness that you want; you’re not putting it where you don’t want it. To describe it is one thing, but to see a physical example of it tells a very good story.
Louwet: Again, here you have the environmental aspect. Normally you would curtain coat, spray or screen print solder mask containing a lot of solvent. You have to dry it—quite a long process involving solvent evaporation and energy. You image, develop, cure, and finish it. With respect to the process and the environment, I think it’s very clear. You do not have to do a lot of calculations to convince people of the benefits.
At productronica, we are presenting our new version of the solder mask ink. Last time we talked, we had our SMG01. That is a good ink. Some customers are using it, but we saw that we could improve with respect to image quality, the sharpness of the lines could be better. Also, especially in ENIG finishing, we saw that the process latitude with the first-generation ink was not that wide. We could make it work, but it had to be right-on with respect to the pre-treatments and so on. This new version, DiPaMAT SMG02, is also a green ink for rigid boards which will have these benefits.
Starkey: This involved working closely with the equipment manufacturers, particularly the printhead suppliers, in achieving the image quality and then with your own developments in chemistry to achieve the chemical resistance and the process latitude.
Louwet: The relation with the printer integrators and going together to a customer is crucial. It’s very important that you do not finger-point when something is wrong, but that you find the solution together.
Starkey: Work together, yes.
Louwet: It is indeed very important.
Starkey: This is a serious production-capable process in terms of the throughput that can now be achieved with the equipment that’s available in conjunction with the inks that you can supply.
Louwet: Yes. If you look at the throughput and you compare it—not with a classical film-exposure type of technology, because that goes very fast—but with an DI process for solder mask, I think it’s very competitive. And you can do things that you cannot do with the traditional process.
Starkey: So, it’s the resolution and definition that you can now achieve with your latest formulations and the latest development in print heads. Can these approach the level of resolution that you can achieve with direct imaging?
Louwet: 75 micrometer L/S is state-of-art and that is good enough for most of the solder mask applications. The printer integrators are also looking into an even higher resolution, but I think for what is required today, it’s good enough. It’s really a matter of validation, certification, convincing some OEMs and then going for it. There are a few bigger companies that take the lead, really want to work on this digital track, and make it work. That’s nice to see.
Starkey: The things that can be achieved in resolution, chemical resistance, and selective imaging—is this the sort of thing that the end-user, the OEM, has a lot of influence in, rather than the PCB fabricator who basically does what the specification tells him to do?
Louwet: I think that the benefit for the PCB manufacturer is quite obvious with respect to the process, the flexibility, not having to have the screens and whatever. Of course, the OEM needs to validate and certify. With OEM approval, the technology can roll out fast. There are advantages for the OEM, things that you can do with inkjet that you are not able to do with the classical process. We are working on two tracks: with the OEMs and with the PCB manufacturers.
At productronica, in all the examples of legend ink, etch resist, and certainly solder mask, we want to show that for growing your business, you do not need to grow your footprint.
Starkey: Yes. I’m very impressed by your representation of a footprint formed from a green leaf. It grabs one’s attention and makes one curious as to finding out what other information is behind it.
Louwet: I also like it a lot. It confirms Agfa’s commitment to achieving specific U.N. Sustainable Development Goals (SDG) without neglecting the business aspects from our customers’ perspective.
Starkey: Frank, it’s always a pleasure to talk to you and I’m grateful for the time that you’ve spent with us, the information that you’ve shared, and the openness with which you shared it. I wish you a very successful show and I hope to see you in person soon.
Louwet: Thank you very much for your time, your questions, and interests.
Suggested Items
Silicon Mountain Contract Services Enhances SMT Capabilities with New HELLER Reflow Oven
07/17/2025 | Silicon Mountain Contract ServicesSilicon Mountain Contract Services, a leading provider of custom electronics manufacturing solutions, is proud to announce a significant upgrade to its SMT production capability with the addition of a HELLER 2043 MK5 10‑zone reflow oven to its Nampa facility.
Knocking Down the Bone Pile: Addressing End-of-life Component Solderability Issues, Part 4
07/16/2025 | Nash Bell -- Column: Knocking Down the Bone PileIn 1983, the Department of Defense identified that over 40% of military electronic system failures in the field were electrical, with approximately 50% attributed to poor solder connections. Investigations revealed that plated finishes, typically nickel or tin, were porous and non-intermetallic.
SHENMAO Strengthens Semiconductor Capabilities with Acquisition of PMTC
07/10/2025 | SHENMAOSHENMAO America, Inc. has announced the acquisition of Profound Material Technology Co., Ltd. (PMTC), a premier Taiwan-based manufacturer of high-performance solder balls for semiconductor packaging.
KYZEN to Highlight Understencil and PCB Cleaners at SMTA Querétaro Expo and Tech Forum
07/09/2025 | KYZEN'KYZEN, the global leader in innovative environmentally responsible cleaning chemistries, will exhibit at the SMTA Querétaro Expo & Tech Forum, scheduled to take place Thursday, July 24, at Centro de Congresos y Teatro Metropolitano de Querétaro.
Driving Innovation: Direct Imaging vs. Conventional Exposure
07/01/2025 | Simon Khesin -- Column: Driving InnovationMy first camera used Kodak film. I even experimented with developing photos in the bathroom, though I usually dropped the film off at a Kodak center and received the prints two weeks later, only to discover that some images were out of focus or poorly framed. Today, every smartphone contains a high-quality camera capable of producing stunning images instantly.