-
- News
- Books
Featured Books
- pcb007 Magazine
Latest Issues
Current IssueVoices of the Industry
We take the pulse of the PCB industry by sharing insights from leading fabricators and suppliers in this month's issue. We've gathered their thoughts on the new U.S. administration, spending, the war in Ukraine, and their most pressing needs. It’s an eye-opening and enlightening look behind the curtain.
The Essential Guide to Surface Finishes
We go back to basics this month with a recount of a little history, and look forward to addressing the many challenges that high density, high frequency, adhesion, SI, and corrosion concerns for harsh environments bring to the fore. We compare and contrast surface finishes by type and application, take a hard look at the many iterations of gold plating, and address palladium as a surface finish.
It's Show Time!
In this month’s issue of PCB007 Magazine we reimagine the possibilities featuring stories all about IPC APEX EXPO 2025—covering what to look forward to, and what you don’t want to miss.
- Articles
- Columns
Search Console
- Links
- Media kit
||| MENU - pcb007 Magazine
Estimated reading time: 4 minutes
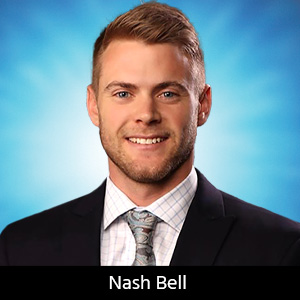
Knocking Down the Bone Pile: Humidification for ESD Control in PCB Rework/Repair
The amount of charge generated in an electronics rework and repair area is affected by a variety of factors, including but not limited to, the materials used and the amount of frictional interaction between materials, as well as the relative humidity of the environment. During the cold winter months in northern climates when the heating systems dry out the plant air and the relative humidity falls, higher electrostatic charges develop, all other things being equal. Lower humidity can increase the number of ESD events, so theoretically it stands to reason that keeping the rework area at higher humidity levels will reduce the chances for charged-induced damage to components.
To get to the “right” relative humidity level in the PCB rework/repair area, several variables need to be taken into consideration. The electronic components being reworked need to fall within their specified RH operating range. In addition, the rework processing steps, such as the length of time the repair epoxy takes to cure or the amount of time the conformal coating material needs to cure, are some of the process steps which will be impacted by the humidity level. Too high of a relative humidity level may result in unwanted quality problems such as corrosion, hand soldering defects, and unwanted MSD damage to moisture sensitive devices. Solder paste will not have the right printing and slump properties at higher relative humidity levels. This may impact paste printing rework processes such as leadless device or BGA component site printing. Typical relative humidity ranges for the PCB rework and repair area are between 30-60%. With a 40% relative humidity level, surface resistance is lowered on floors, carpets, table mats, and other susceptible areas (Figure 1).
Increased humidity levels can be accomplished through humidification systems. Humidifiers add water vapor to the air, which forms a thin protective film on surfaces and serves as a natural conductor to dissipate electrostatic charges. When humidity levels drop below 40% RH, this protection disappears, thereby increasing the possibility of damage or defects within electronic components and devices.
There are numerous risks to operating the PCB rework and repair area when the air is at low relative humidity. If any existing static monitoring or control systems fail (e.g., a ground connection becomes disconnected, operators missing a wrist strap, foot grounders, or grounding mats will have had coating spilled on them making them insulating surfaces), there is no backup to controlling static charging impacts. Secondly, any reworked board which is not touching an ESD-safe surface or handled properly by an ESD-protected rework technician can be damaged. In many cases, controlling the humidity levels is easier than ensuring that non-charge-generating material does not enter the workspace. These are some of the risks to operating the rework area in a low humidity environment.
Adding humidity to the rework area cannot replace a robust ESD control system just by employing humidification, rather it may be used in conjunction with such a control program. Such a program should contain the following elements:
- A training/retraining program of PCB rework/repair technicians
- Operators wearing wrist straps when handling ESD product
- A static dissipative floor
- All ESD benches identified as such and properly connected, each with its own connection to ground
- Operators wearing dissipative footwear
- Operators wearing ESD-safe smocks correctly
- Charting/monitoring of the relative humidity along with monitoring alarms
- Keeping insulators out of the rework/repair operating zone per EOS/ESD 2020 requirements
- An audit system in place to monitor all the above, with sufficient frequency for each method to ensure compliance and effectiveness
Air humidifiers cannot replace these and other ESD control measures. Adding moisture to an environment where two materials of differing electrostatic potential come into contact and separate (like Kapton™ tape being pulled off a dispenser) will not stop the charging from occurring. However, adding moisture to the environment will reduce the number of ESD events. No humidity control system will prevent this.
Commercially available industrial humidification systems have a variety of features as part of their design. The systems designed for electronics assembly are typically closed-loop systems where moisture is measured, and the level is controlled. The water used passes through hygienic multi-stage filtering systems including UV lighting. This helps ensure that the water vapor being dispensed does not damage machinery and electronic assemblies. Many systems have line flushers to purge out impurities from time to time.
At the end of the day, in the deep of winter in northern climates, the heating systems employed in the PCB rework area will dry out the air and move the relative humidity to low levels. This in turn will allow ESD events to occur more readily, putting pressure on the robustness of the ESD control and monitoring program. While humidification systems are not required in all cases, their use in certain conditions may be warranted.
References
- “Coaxing better performance from electrostatics demonstrations in humid conditions,” Thomas Jones, class notes, University of Rochester.
This column originally appeared in the January 2022 issue of SMT007 Magazine.
More Columns from Knocking Down the Bone Pile
Knocking Down the Bone Pile: Basics of Component Lead TinningKnocking Down the Bone Pile: Package on Package Rework—Skill Required
Knocking Down the Bone Pile: 2023’s Top Challenges in BGA Rework
Knocking Down the Bone Pile: Eliminating Solder Balls in Hand Soldering
Knocking Down the Bone Pile: Opening a Trace on the Surface of a PCB
Knocking Down the Bone Pile: Soldering for QFPs and Other Gull Wing Leaded Parts
Knocking Down the Bone Pile: Reworking of SMT Connectors with Center Ground Connection
Knocking Down the Bone Pile: Solder Mask Repair Techniques for PCB Repair